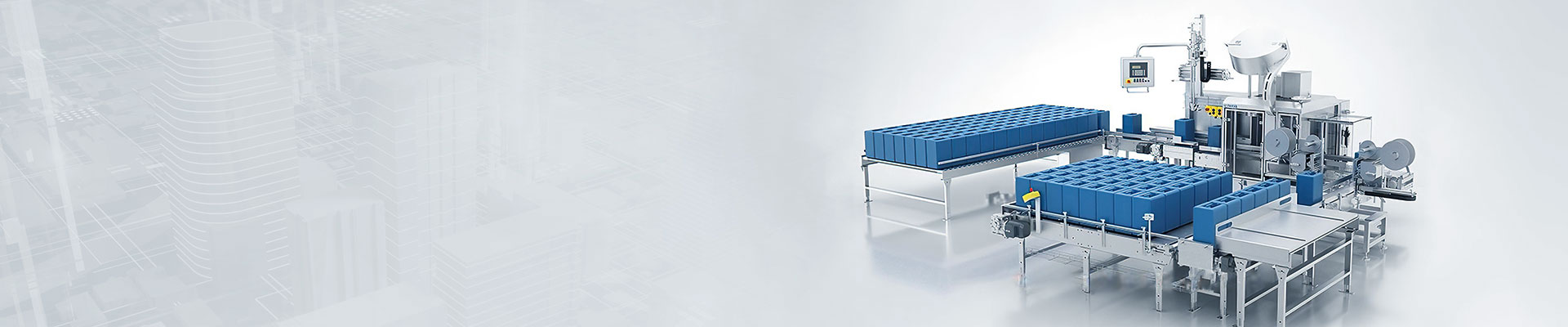
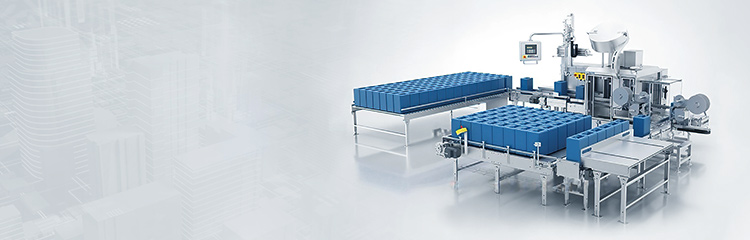
The batching equipment adopts S7-300 and ET200 as the control, data calculation, storage and management of the whole batching to realize centralized monitoring and decentralized control. It mainly consists of feeding system, weighing system, mixing and conveying system and central control system, and through the central control system, each sub-system will be integrated and intelligently controlled to achieve the purpose of energy saving and consumption reduction. The batching production and melting production are closely connected to complete the seamless linkage of resin raw material supply and consumption, eliminate the misjudgment of production conditions, reduce the stagnation, misbehavior and disturbance, and improve energy efficiency. Relying on the monitoring of the current dosage operating parameters introduced into the production process, automatic correction at each process conversion point, so that each process dosage in the entire system production process to give full play to the unit time brought about by the improvement in accuracy, to achieve the best fit.

Reactor weighing (batching equipment) adopts advanced SIEMENS PLC, industrial weighing computer and PANTHER electronic weighing equipment. Its main components include power part, weighing part, feeding and discharging part and weighing part, etc. It is a computerized full reactor weighing and batching designed for the production of float materials.
The batching plant uses toning tank type storage, with a total of powder raw material tanks, powder reaction pots, activation funnel at the outlet of the reaction tank, activation funnel outlet through a soft connection to the inlet of the storage tank, according to the flow of materials to determine the activation of the funnel to start the situation, to ensure that the supply of materials is normal.
Three Weighing modules are installed underneath the hopper of the metering and dosing system, and there is a dust removing port on the hopper scale, which is connected with the collector pipeline and the guide material crystallization tank to prevent dust from leaking out, and the metering and dosing method of "reduced quantity method" is adopted.
Electromagnetic vibrating Feeder is adopted, and the discharging should have the function of time-sharing operation, so that the materials can be evenly spread into the sandwich state. The powder material is mixed into the premixer first, and the premixer is discharged at the same time with other materials. The powder material is evenly spread on the mixer.
With the material pipeline will be put into the extraction tank through the intermediate composite scale to complete the mixing operation of the material. Mixed material is discharged from the mixer into the emulsion tank through the flow color mixing kettle to the mixed material pipeline machine into the mixing color mixing tank.
The dosing kettle has the function of full-automatic, semi-automatic and manual, from the outlet of the horizontal storage tank until the qualified mixed material is sent to the mixing silo.
The weighing of the dosage section, mixing section and conveying section are all from the dosage scale, with a display screen and industrial TV to monitor the whole production process.
Concentration tank, batching machine, mixer and other equipment ammeter, the batching equipment should have a chain function.
The computer data system adopts the form of upper computer + programmable weigher, which should have the following functions:
The system shall have power-down protection function; the upper computer manages to collect data automatically; it has self-diagnosis function;
With automatic correction of overshoot and spot replenishment function; management and transmission of formula and set value;
Automatic weighing; overdifference alarm and fault printing;
Friendly man-machine interface, multiple use rights multiple password restrictions; displaying, printing the current formula and production reports;
Displaying, printing and storing the single and total consumption of various materials on shift, day and month;