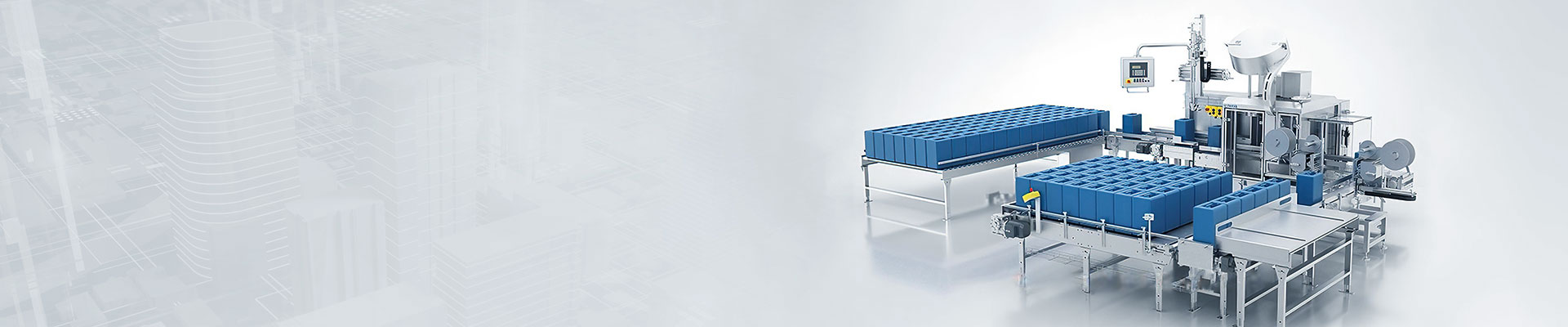
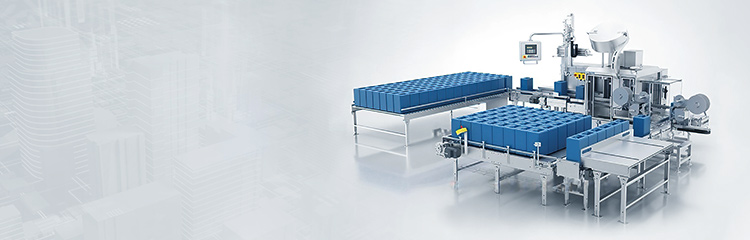
Powder dosing system is a device used for additives and pre-mixing, PLC as the main control of the unit, weighing module to collect the weight of the material in the mixer, and should be located (when the material is lost). The limit switch, when the lifting action reaches the position, should send a signal in the appropriate position.

Automatic feeding system is a device for additives and pre-mixing, PLC as the main control of the unit, weighing module to collect the weight of the material in the mixer, and should be located (when the material is lost). The limit switch, when the lifting action reaches the position, should send a signal in the appropriate position. Analog output signal, 4-20mA to 4 valve switches, control the opening, with the S-type tension to collect the material position, and close the valve when the weight reaches the required batching weight.
The lifting action of each mixer shall use a switch plate to give a start and stop signal to the brake motor. Has a communication circuit module, its function is to communicate with the console. The communication data is bidirectional, requiring the reception of the material specific gravity information from the console and the weight distribution of each material mixer. The working conditions, amount of materials used and time of use will also be packaged and uploaded to the console. A specific GPRS communication module (i.e. wireless network, done by the phone's SIM card) is required. The protocol can stop the mixer directly through the console command, which requires remote control function. To achieve one-click start and stop function. This can be achieved through the GPRS module.
Through the processing and judgment of the digital input signal, the host sends a control signal to start the Feeder corresponding to the first component in the formula to feed the mixer, and the weighing sensor converts the weight of the material into a signal according to a certain functional relationship and transmits it to the host. The host collects data quickly, processes it in real time, and sets up components in the recipe. The host sends a control signal to stop the feeder operation and the component feed stops. The next component in the recipe is then fed in the same procedure until all components have been distributed and the batch is complete.