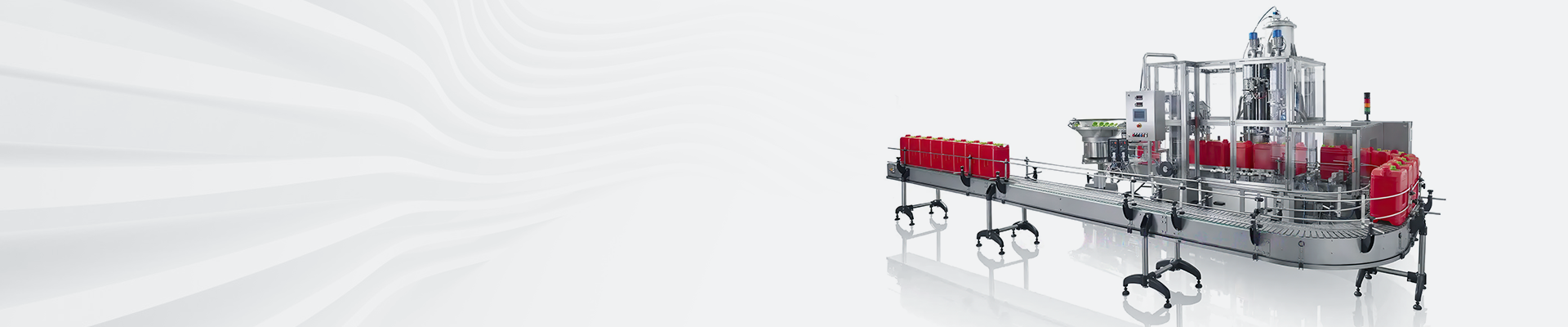
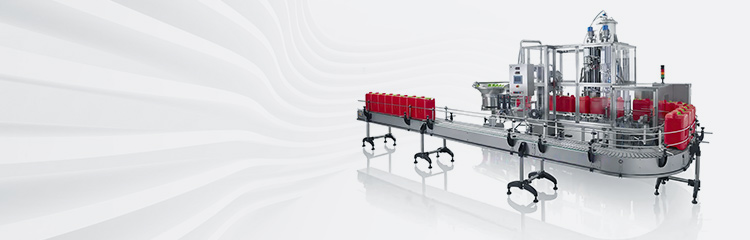

Summary:The pulverized coal pneumatic conveying system is mainly composed of three parts: coal storage bin, feed tank and distributor. The role of the coal storage bin is to store and provide pulverized coal to the feed tank, the external pulverized coal through the pipeline, with nitrogen transported to the coal storage bin, generally can be stored 24h coal: the role of the feed tank is to use nitrogen to make the pulverized coal fluidization, at the same time, to provide pulverized coal to the distributor, which works at the working pressure and atmospheric pressure in the two states; the role of the distributor is the use of compressed air as a carrier for the quantitative delivery of pulverized coal to the QSL furnace, which can be accurately controlled for each pair of lances to give coal to the distributor. The distributor uses compressed air as a carrier to quantitatively deliver pulverized coal to the QSL furnace, which can precisely control the amount of coal fed to each pair of lances, thus effectively controlling the reduction degree and temperature of the QSL furnace.
1、Preface
Solid material pneumatic conveying technology refers to the use of airflow energy, in the closed pipe along the direction of airflow conveying granular materials, which has the advantages of airtight, safe, materials and environmental cleanliness, easy to realize the advantages of automated continuous operation, it is widely used in the chemical industry, power generation, pharmaceuticals, food, construction, metallurgy and other industries".
In 2011, the global refined lead production was 10.372 million tons, China was 4.648 million tons, accounting for 44.8% of the world, is the world's largest lead producer, however, China's crude lead smelting technology and equipment level is generally low, the traditional lead concentrate sintering a blast furnace reduction process is still predominant in lead smelting, but there are defects of large energy consumption and serious pollution, and can not meet the increasingly stringent QSL method, i.e. oxygen bottom blowing melting pool smelting method, is one of the direct lead smelting methods, which omits the sintering process compared with the traditional lead smelting process, so it has the advantages of short process, convenient furnace operation, high heat utilization, high concentration of SO in the flue gas, and high lead recovery rate, especially the introduction of pulverized coal pneumatic conveying technology into the process, which is very important for realizing highly automated and improving the lead smelting process, and also for improving the lead smelting process. It is of great significance for realizing high automation, improving the working environment of lead smelter workers, and improving the utilization rate of raw materials.
2、Powder Coal Pneumatic Conveying Machine
Pulverized coal pneumatic distribution machine is mainly for the QSL furnace to provide heating and reduction of pulverized coal. The pulverized coal is metered and then transported by compressed air to the pulverized coal spray gun and shot into the liquid oxidized slag in the reduction section of the QSL furnace at a high speed, so that the lead oxide and lead silicate in the slag can be reduced to lead metal and enter into the crude lead slag: C+O₂=CO₂; C+CO₂=CO; PbO+C=Pb+CO; PbO+CO=Pb+CO₂.
2.1 System process flow
The pulverized coal pneumatic conveying system is mainly composed of three parts: coal storage bin, feed tank and distributor. The role of coal storage silo is to store and provide pulverized coal to the feed tank, external pulverized coal through the pipeline, with nitrogen transported to the coal storage silo, generally can be stored 24h coal: the role of the feed tank is to use nitrogen to make the pulverized coal fluidization, at the same time, to provide pulverized coal to the distributor, which works at the working pressure and atmospheric pressure in the two states; the role of the distributor is the use of compressed air as a carrier for the quantitative delivery of pulverized coal to the QSL furnace, which can be accurately controlled for each pair of lances to feed the coal. It can precisely control the amount of coal fed to each pair of lances, so as to effectively control the reduction degree and temperature of the QSL furnace.
2.2 Dosing system assembly and design points
Assembly of pulverized coal pneumatic conveyor
(1) Coal storage silo: the upper part of coal storage silo is equipped with a bag dust collector using pulse blowback vibration to filter the conveying gas, the lower part is equipped with a star feeder to control the speed of the material; the wall of the silo is equipped with a fluidization device to improve the fluidity of the pulverized coal; the lower pivot is equipped with a load cell to measure the level of the coal silo, and the level is reflected in the instrument as a control parameter, and the coal storage silo and the feeding canisters are connected with pipelines to be fed by the feeding canister through the bell valve, with the pipeline equipped with a load cell for feeding coal, with the pipeline equipped with the bell valve to be fed with coal. The coal storage silo is connected with the feeding tank by a pipe, and the feeding tank is controlled by a bellows valve, and a bellows is set on the pipe to buffer the connection force so that the coal storage silo can be weighed accurately, and the pipe is equipped with a maintenance gate valve for use during maintenance.
(2) Feeding tank: the feeding tank is the equipment between the coal storage bin and distributor, the upper part of which is equipped with bag dust collector for filtering the gas during decompression; the bottom center is arranged with mechanical stirring device and gas stirring device, when feeding to the distributor, the stirring device will start, so that the pulverized coal can enter into the distributor smoothly; the bottom is equipped with a mechanical level sensor to ensure the reliability of the work: when the feeding tank is at the low level, the request for refilling will be issued, and the pressure relief valve will be opened. When the feeding tank reaches the low level, it will send out the request of feeding, the pressure relief valve will open to reduce the pressure, and when the pressure reaches the normal pressure, it will open the feeding valve to feed the coal from the coal storage bin; when it reaches the high level, it will send out the request of stopping the feeding, close the pressure relief valve, and the feeding valve will close to increase the pressure to the working pressure. The feeding tank and distributor are connected by pipeline, and the feeding to the distributor is controlled by bellows valves. In order not to affect the weighing and measuring of the distributor, two bellows valves are set up between the feeding tank and the distributor, and the pipeline between the bellows valves is kept at atmospheric pressure in normal operation, and two sections of bellows are set up to isolate the effect of the connecting force.
(3) Distributor: the distributor is equipped with two mechanical level sensors, when the material level is low, the weighing and measuring will be stopped, the request for adding material will be issued, the conveying pipe will be pressurized to the working pressure, and then the bell valve will be opened and the feeding will start, when the material level is high, the bell valve will be closed, the lower pipe will be depressurized to the atmospheric pressure, and the metering will be resumed: at the bottom of the distributor, there is a dividing wheel and a stirring device, which rotates synchronously along with the dividing wheel to ensure that the pulverized coal will be distributed uniformly in the spraying gun. The distributor tank support is equipped with a load cell to obtain information about the weight loss and thus the instantaneous feeding quantity, against which the rotational speed of the dividing wheel can be adjusted to regulate the amount of coal to be added.
2.3 Technical operating conditions
(1) Pulverized coal particle size and moisture content: the particle size of pulverized coal has an important effect on the reduction of lead.
It can be seen that as the size of pulverized coal increases, the lead content of the final slag decreases. This is due to the QSL method of lead refining process, the lead phase precipitated on the surface of pulverized coal will form a liquid film covering the reaction surface, easy to isolate the slag phase and pulverized coal contact, such as pulverized coal radius is larger, it is easier to rupture the liquid film and expose the surface of the pulverized coal to increase the reaction rate, which reduces the final slag in the lead content. However, if the particle size is too large, poor fluidity of pulverized coal, the wear rate of the pipeline is also increased, so we need to find a critical radius of pulverized coal, so as to ensure the transmission efficiency, but also to ensure that the pulverized coal and the slag phase have enough reaction interface to make the reduction reaction proceed continuously.
Moisture content is an important parameter affecting the flow characteristics of the material, which plays an important role in the friction characteristics, fluidity, dispersion properties and compression properties of the powder. When the moisture in the coal powder is high, the free water existing between the coal powder particles is mainly in the form of adhesion liquid . Wedge liquid and capillary rise liquid, etc., the contraction of water surface tension will cause the traction force between the 2 particles, the formation of liquid bridges, resulting in agglomeration of particles, granulation phenomenon; at the same time, cause the friction coefficient and viscosity increase. It has been shown that the mass flow rate of pulverized coal gradually decreases with the increase of the moisture content of pulverized coal, and when the moisture content of pulverized coal is increased to 6%, the transportation is very difficult, and the phenomenon of pipe blocking often occurs. Generally speaking, in order to ensure the efficiency of pulverized coal reduction and smooth conveyor, the particle size of pulverized coal used shall be less than 0.05mm, and the moisture content is less than 1%.
(2) Conveying pressure: pulverized coal pneumatic conveyor valves and the formation of pneumatic drive, in the safety considerations, all using nitrogen, the highest driving pressure of 1.1Mpa. pulverized coal and oxygen flow to achieve the QSL furnace reduction section of the process technology is very important to the operating conditions. The control system can give the pulverized coal flow rate of each nozzle according to the amount of coal feeding and pulverized coal conveying carrier, and automatically adjust the oxygen flow rate of each nozzle. The pulverized coal delivery carrier pressure should be kept stable at about 0.35-0.5 MPa. nitrogen, and the oxygen pressure is 0.6-1.0 MPa. When the oxygen pressure drops to the lowest value (about 0.6 MPa), the oxygen channel will be automatically switched to nitrogen, preventing the melt from being filled in the oxygen channel.
3、Conclusion
In recent years, China's lead production has been growing steadily, and has become a global lead production and consumption center, and it is very important to improve the equipment level and process design level of lead smelting in China to improve the overall backwardness of China's lead smelting industry, to improve the working and atmospheric environment, and to improve the industrial automation and the enterprise's comprehensive economic efficiency. In QSL one-step lead smelting process, reasonable pulverized coal conveying and control system should be selected to improve the safety and reliability of the work, and play the role of reducing energy consumption and pollution; reasonable technical operating conditions should be selected to improve the efficiency of pulverized coal conveying and reducing effect to reduce the wear and tear of pulverized coal on the pipes and lances, and reduce the lead content in the liquid slag.