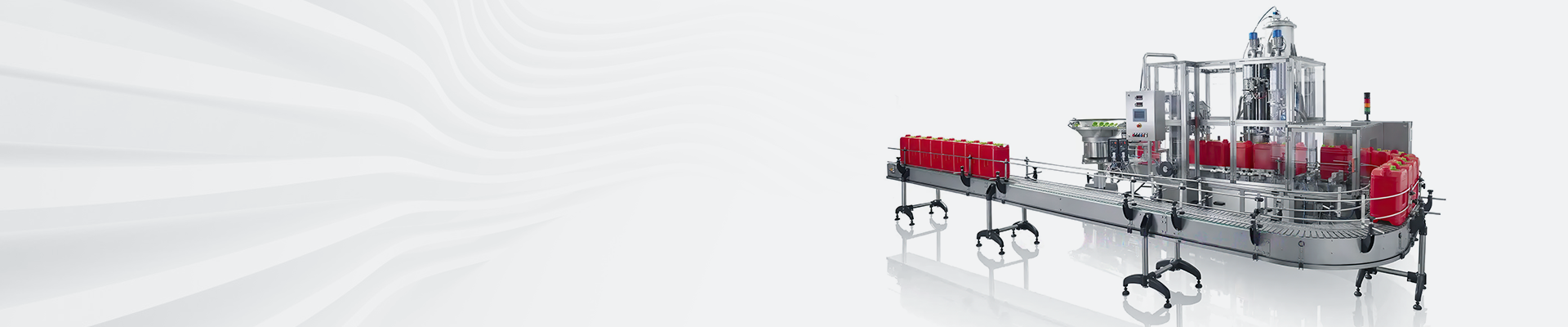
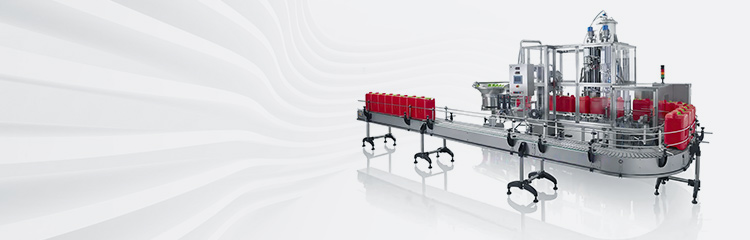

Summary:The automatic batching system can be used in industrial measurement control automated production of coatings, paints, food, beverages, chemicals, pharmaceuticals, etc., where a variety of liquid raw materials are proportioned and weighed according to formulas.
PLC as the logic control center according to the process recipe requirements for the implementation of electronic weighing operations. The industrial computer (fully compatible with general computers, more compliant with the harsh industrial environment) as the upper computer is the operation terminal of the dialogue between man and machine, whose main function is to monitor the operation of the entire weighing system based on electronic scales, and to give operation orders and calibration correction parameters to the PLC.
It is controlled by computer, weighs all kinds of materials automatically according to the user's pre-set dosage program, and controls each link of dosage automatically to complete the dosage process. The key to accurate dosage of automatic dosage system is to control the rotating speed and starting and stopping of dosage motor. In the process of dosage, the rotating speed of motor is controlled according to the amount of dosage, which is divided into different dosage modes such as high-speed dosage and low-speed dosage to not only improve the working efficiency of the system, but also enhance the accuracy of dosage. When the difference between the actual feeding and the set value is large, the dosage accuracy of the dosage system meets the requirements.
The automatic feeding system adopts high-speed feeding mode, which can improve the working efficiency of the system. When the feeding value has been weighed batching system is a high-tech product of electromechanical integration, which consists of three major parts: mechanical, detection and electrical control. The role of the mechanical system is to complete the storage of the material concerned, conveying and other functions, mainly by the feeder, conveyor, hopper, material gate switch, etc.; Detection part of the role of the dosage process is to weigh a variety of materials, mainly by the scales, load cells, etc., commonly used in the detection part of the weighing module, elastic components through the strain gauge will be the weight of the material into a micro-strain signal, through a bridge circuit The elastic element converts the weight of material into micro-strain signal through strain gauge, which is converted into electric signal through bridge circuit, and outputs the analog signal proportional to the value of material, which can be calibrated in kind or electrically calibrated to determine the accurate weight value corresponding to the electric signal. The function of the electrical control part is to control in the process of batching, control the transportation, feeding and unloading of materials, which mainly consists of electric motor, frequency converter, weighing indicator and computer.
The feeding system sets the given value of each material according to the proportion of preparation, and the weighing controller or computer sequentially controls the feeding of various materials and detects the amount of material added, and controls the rotation speed of the motor for discharging materials according to the amount of materials set by the system, and closes the feeding valve of the material when the amount of material added reaches the set value, until all the materials are finished being added according to the set value of adding to the end of the dosage.
According to the production requirements, the automatic batching system can work in the following three ways:
1. Manual mode of work: the operator uses manual buttons to carry out dosage work, the computer is only used as a meter to display. This way of working is inefficient, generally only used for system debugging or some special circumstances.
2. Semi-automatic working mode of computer: according to the instruction of the operator, the computer realizes the proportion of the corresponding materials.
3. Automatic working mode: the dosage system completes the dosage tasks automatically according to the selected dosage process, during which basically no personnel intervention is needed. In normal production process, the system generally works in automatic mode.
In the process of automatic dosage, there are many factors affecting the dosage accuracy, mainly including feeding speed and uniformity, hopper vibration, drop (air residual material) and overshoot and other factors. The vibration of the hopper makes the weight signal obtained by the sensor does not accurately reflect the actual weight of the material in the hopper. Dropout is caused by the material in motion (the flow of material from the feeder or valve into the hopper on its journey), which has not yet reached the surface of the material in the hopper. The overshoot is due to a delay from the time the electronics send a stop signal until the valve actually closes or until the feeder actually stops rotating. Which the specific gravity of the material, the flow and the size of the fall caused by the different random changes in the amount of overshoot, to the dosage of precision control has brought greater difficulties.
When it is close to the setting value, it adopts low-speed discharging mode, and the motor stops rotating when the control lead time is reached due to the material retained in the air between the discharging port and the material tray. When the actual dosing process reaches the control lead time, due to the difference in material density, the quality of the material left in the air after the motor stops rotating is different, so the system should be able to set the lead time for the motor to stop according to the actual running condition. Determine the end moment of feeding according to the fall compensation coefficient of each material, read the final weight of the material in the hopper after the weighing hopper is stabilized and compare it with the set value, which will be used as the basis for choosing the correction coefficient of the fall of dosage for the next time. That is, the current dosage using the last dosage of measured fallout value and fallout compensation value of the average value of fallout compensation, this way to make the dosage system dosage accuracy with the increase in the number of dosage and improve.
PLC can realize highly flexible and reliable industrial control by combining computer technology with traditional relay control system. In the automatic dosage system, PLC is mainly responsible for receiving external switching signals to determine the current operating status of the system, and output various control signals to control contactors, relays, solenoid valves and other components to carry out the corresponding action. According to the specific dosage process, at the beginning of dosage, the motor runs normally and the feeding system discharges materials at high speed; when the weight of the materials is close to the target value, PLC is used to discharges the materials in the pointing control mode, so as to ensure the requirements of the material metering accuracy. In addition, PLC is also responsible for receiving control commands from the upper computer to complete the control of automatic dosage.