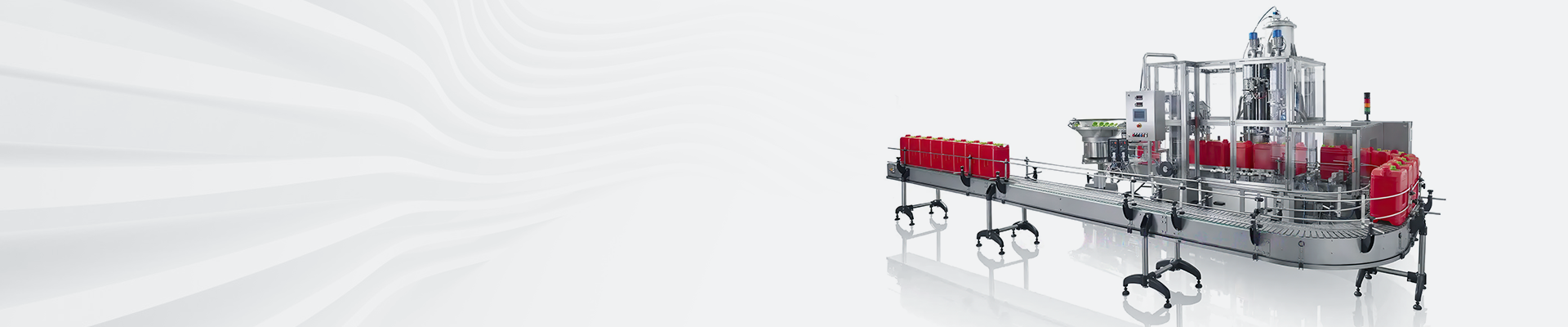
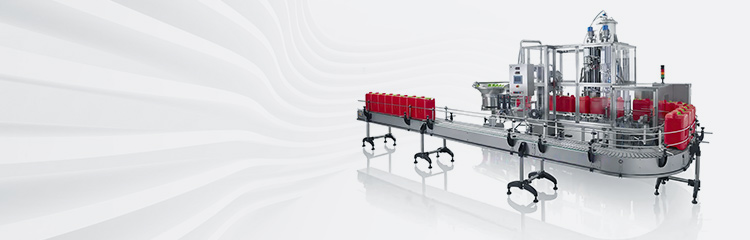

Summary:The automatic batching system has register space and exclusively provides file register space to ensure that the system's recipe volume is large enough and the recipe is absolutely safe through common command operations.
The process control of weighing and batching system is almost entirely realized by programmable controller (PLC), and the upper computer is mainly used for formula management, screen human-machine dialogue and the storage and printing of weighing data. With the development of microprocessor technology, the dosage system weighing instrumentation from the initial special building block type instrumentation for the development of intelligent industrial control terminals and specialized dosage controllers. Batching controller is used to control the preparation of one or more materials microcomputer touch screen system, can completely or partially replace the programmable controller, to achieve the automation of batching. The function of weighing instrument is also developed from the initial information display to have self-diagnosis, automatic zero tracking, zero tare, preset point output, dynamic weighing, data communication and other functions.
In recent years, with the promotion of fieldbus technology, the traditional dosage control system to improve the fieldbus-based control system has become an inevitable trend of scientific and technological progress. At present, many weighing instruments based on touch-screen dosage have Profibus, Modbus and other fieldbus interfaces, which make the fieldbus-based dosage control system possible, and the fieldbus-based dosage control system is being promoted rapidly.
According to Siemens s7-200PLC and weighing instrument as a controller to complete the control process, the feeding system is mainly composed of s7-200PLC, weighing instrument, HMI and four-channel dosage equipment. The accurate weighing of the corresponding set mass is accomplished by setting parameters such as zeroing and calibration of the weighing instrument. The calibration value is set to 1Kg, the permissible error range is within 10g, and the air flying time is set to 1s. When the measurement starts, the switch will be activated, and the input channel of s7-200PLC will be given a rising edge, and the output channels q0.0 and q0.1 will be set to 1, and the fast-feeding valve and slow-feeding valve will be opened at the same time, so that liquids can be injected into the drum together, and the liquid in the drum will be injected into the barrel when the liquid in the drum reaches the preset value, and then Q0.0 will be set to 1, and Q1 will be set to 1. When the weighing instrument measures that the liquid mass in the drum reaches the preset value of the slow-feeding quantity, Q0.1 is set to 0 and the fast-feeding valve is closed, and the remaining mass is injected by the slow-feeding valve until it reaches 1Kg, then the slow-feeding valve switch Q0.0 is set to 0 and the slow-feeding valve is closed. The system uses slow feed valve and fast feed valve two ways to add raw materials, in order to achieve high-speed, accurate purpose, the error tolerance range of 10 g. The system process affects the system error of many factors, such as the liquid in the air to stay in the air time that the air flying material time, and the impact of the flow rate of the size of the pressure that is the liquid level and so on. In order to further minimize the error, it can be adjusted by setting the time of flying in the air. When the weighed liquid mass reaches the preset value, the weighing instrument will feedback signal to s7-200PLC, the output Q0.3 will be set to 1, and the valve will be turned on to start discharging. When the mass of liquid in the barrel weighed by the weighing instrument is 0, the discharging will be finished, and Q0.3 will be reset at the same time, completing the weighing of raw materials, and the whole process can be set and observed through the touch screen. The materials are weighed in the four channels, when and only when the four channels discharge valve are in the reset state, the mixing motor starts to work, the raw materials are stirred, to complete an industrial dosage of practical applications.
Feeding system using weighing instruments together with the main component of measurement and dosage control, weighing instrument tare, tare and zero through the RS232C communication based on the use of VB in the MSComm control to write the upper computer and weighing instrument communication program, weighing data collection, and the data stored in the Access database. On the basis of Ethernet communication, call the software provided by the manufacturer of the weighing instrument to recover the weighing data from the host computer and write them into the Access database of the host computer. At the same time, the database calls the valid data and stores the weighing data of the weighing instrument in the database centrally. The data from the weighing instrument is sent to the host computer through the serial port in real time, and the host computer intercepts and converts the read data, and the weighing data can be displayed in the VB running screen in real time, and at the same time, the weighing data can be stored in the database, so as to facilitate the querying and tracing function of the data.
The automatic dosing system consists of 4 storage tanks and metering tanks, driven by weighing control instrument, according to the production process initiative in turn for the storage, drop, mixing, metering, unloading and other components.
The dosing strategy is as follows:
1、When the dosing button is pressed, start dosing
2、Confirm that the measuring tank is empty and the weight is zeroed.
3, half-closed discharge valve 112, open with raw materials A101, until the raw material A101 reaches the set value (i.e., raw materials A101 = weighing the weight minus the empty weighing tare), closed with raw materials A101 dosage, delayed for 1 second mixing system tasks, after a certain period of time to start with raw materials A102 sign bit.
4, when the raw materials A102 logo was established, open with raw materials A102, start with raw materials A102, until raw materials A102 to reach the set value (i.e., raw materials A102 = weighing the weight of the scale minus the empty scale tare and then minus raw materials A102 weight), closed raw materials A102 dosage, delayed by 1 second stirring system tasks, a certain amount of time to start with the next ingredient dosage logo bit. And so on until the completion of the recipe.
The function of the dosage system has the following characteristics:
(1) Complete automatic interlocking and control of feeding, loading, mixing and unloading;
(2) Completing the functions of manual operation of measuring, feeding, loading, mixing and unloading;
(3) Can display the real-time task situation and various material parameters. It can be utilized to call and display and print any time report and customer table at any time. With ratio pre-storage, can be used at any time to output, amend or delete a certain ratio.
(4) Beautiful and applicable static imitation. Application of static screen will be measured and unloaded in the process of dosage valves, drop control, in and out of the material form (mixer level changes) to simulate the display.
(5) with coarse measurement and fine measurement function. (Fine weighing advance has automatic adjustment function to eliminate the impact of fallout), over the difference of the automatic alarm, automatic deduction function.
(6) It has the function of operator authority management.