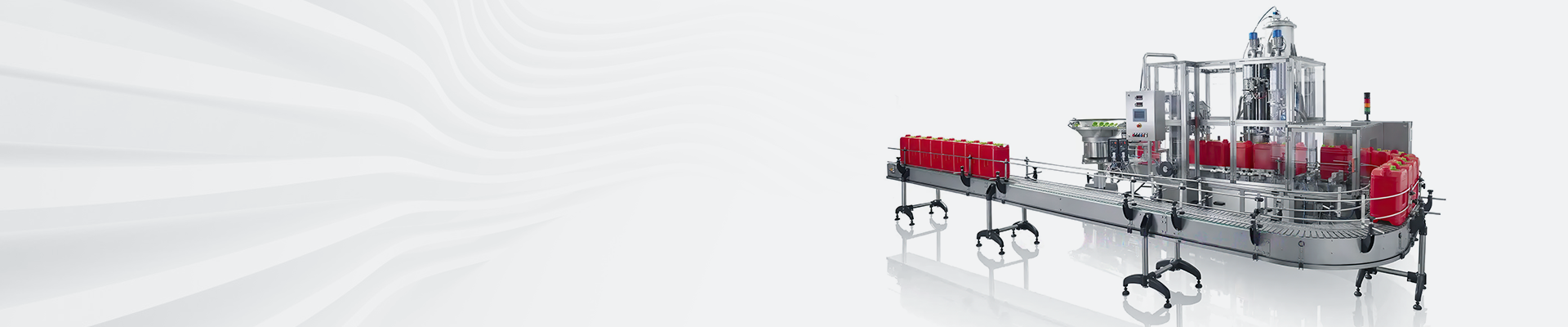
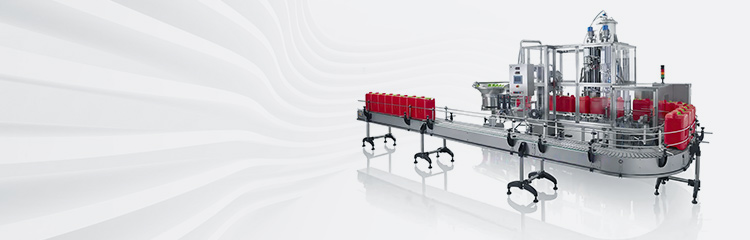
摘要:自动配料系统具有暂存器空间且独家提供档案暂存器空间,保证系统的配方量足够多足够大,透过公用指令操作保证配方的绝对安全。
称重配料系统的流程控制几乎全部由可编程控制器(PLC)来实现,上位计算机主要用于配方管理、屏幕人机对话和称重资料的存储打印等工作。随着微处理器技术的发展,配料系统中的称量仪表由最初的专用积木式仪表发展为智能化的工业控制终端以及专门的配料控制器。配料控制器是用来控制一种或多种物料的配制的微电脑触摸屏系统,可以完全或部分取代可编程控制器,实现配料的自动化。称量仪表的功能也由最初的资料显示发展为具有自诊断、自动零位跟踪、置零去皮、预置点输出、动态称重、数据通信等多项功能。
近年来,随着现场总线技术的推广,将传统的配料控制系统改进为基于现场总线的控制系统成为科技进步的必然趋势。目前许多基于触摸屏配料的称重仪表已经有了Profibus、Modbus等现场总线接口,使基于现场总线的配料控制系统成为可能,基于现场总线的配料控制系统正在迅速推广。
根据西门子s7—200PLC和称重仪表作为控制器,以完成控制过程,上料系统主要由s7-200PLC,称重仪表,HMI和四通道配料设备构成。通过对称重仪表清零和标定等参数的设置,来完成相应的设置质量的精确称重。设置校准标定值为1Kg,允许误差范围在10g以内,设置空中飞料时间为1s。当计量开始时启动开关,此时给s7-200PLC输入通道一个上升沿,此时输出通道q0.0和q0.1置1,快喂阀和慢喂阀同时打开,一同向桶中注入液体,当称重仪表测量到桶中液体质量达到慢喂量的预设值时,将Q0.1置0快喂阀关闭,剩余质量由慢喂阀注满,直到达到1Kg,慢喂阀开关Q0.0置0,慢喂阀关闭。系统采用慢喂阀和快喂阀两种方式添加原料,是为了达到高速、准确的目的,误差允许范围10g。系统过程中影响系统误差诸多因素,如液体在空中停留的时间即空中飞料时间、和影响流速快慢的压力大小即液位等。为了进一步减小误差,可以通过设置空中飞料时间来调整。当所称液体质量达到预设值时,称重仪表将反馈信号到s7—200PLC,输出Q0.3置1,阀接通,开始放料。当称重仪表称的桶中液体质量为0时,此时放料结束,同时Q0.3复位,完成一次原料称重,整个过程可以通过触摸屏设置并观测。把各物料分别在四个通道称重,当且仅当四个通道放料阀都处于复位状态时,搅拌电机开始工作,原料进行搅拌,完成一个工业配料的实际应用。
投料系统采用称重仪表共同组成计量配料控制主件,称重仪表的去皮、清皮和归零经过RS232C通信的基础上,利用VB中的MSComm控件编写上位机与称重仪表通信程序,进行称重数据采集,并将数据存入Access数据库。在以太网通信的基础上,调用称重仪表厂家提供的上位机流水回收软件对其称重数据进行回收,并写入上位机的Access数据库。同时数据库调用有效数据,将称重仪表的称重数据集中存放在数据库。称重仪表的数据通过串口实时发送给上位机,上位机将读取的数据进行数据截取、转换,称重数据就可以实时显示在VB运行画面中,与此同时,称重数据可以存储到数据库中,以便于对数据进行查询追溯功能。
自动配料系统由4个储料槽及计量槽构成,由称重控制仪表驱动,按生产流程举措顺次为储料、落料、搅拌、计量、卸料等构成。
配料战略如下:
1、当配料按钮按下时,启动配料
2、确认计量槽清空,重量归零
3、半闭卸料阀112,开启配原料A101,直到原料A101到达设定值时(即原料A101=秤以重量减去空秤皮重),封闭原料A101配料,延时1秒搅拌系统任务,一定时间后启动配原料A102标志位。
4、当配原料A102标志成立时,开启配原料A102,开始配原料A102,直到原料A102到达设定值时(即原料A102=秤重量减去空秤皮重再减去原料A102重量),封闭原料A102配料,延时1秒搅拌系统任务,一定时间后启动配下一配料标志位。以此类推至完成配方。
配料系统的功能有如下特点:
1)完成进料、上料、搅拌、卸料的自动联锁和控制;
2)完成计量、进料、上料、搅拌、卸料的手动操作的功能;
3)能显示实时的任务情况和各种物料参数。可随时运用调用并显示、打印任何时间的报表与客户表。具有配比预存,可随时运用输出、修正或删除某种配比。
4)美观适用的静态模仿。应用静态画面将计量和卸料进程中的配料阀门、落料控制、进出料形态(混合机料位变化)进行模拟显示。
5)具有粗计量和细计量功能。(精称提前量有自动调整功能,消除落差影响),超差自动报警、自动扣除功能。
6)具有操作员权限管理功能。