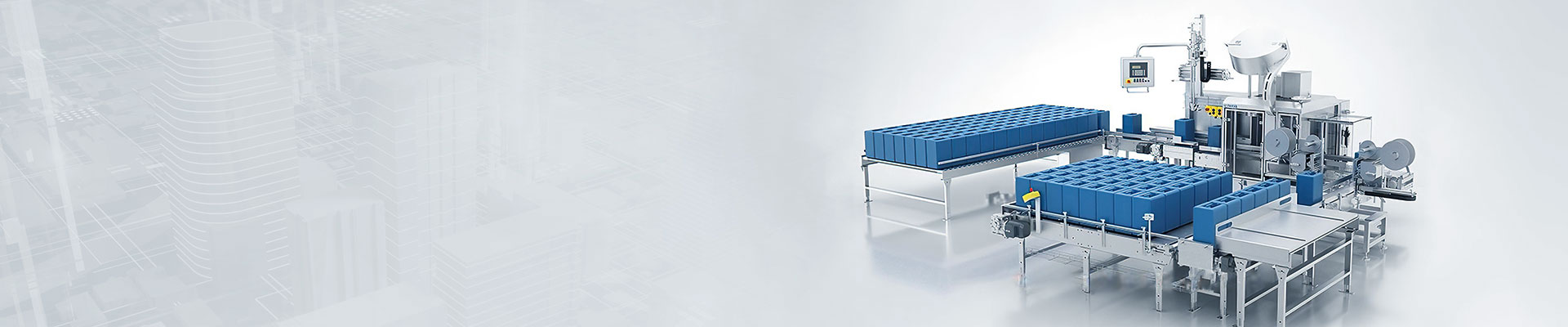
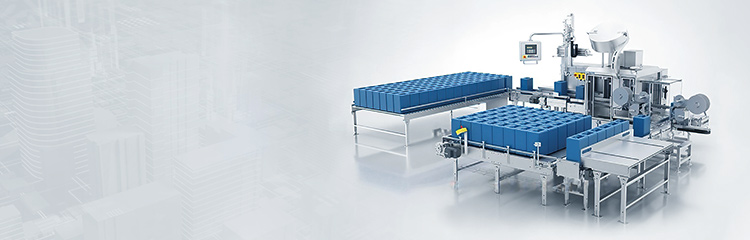
Weighing system is suitable for petroleum, chemical and proportioning industries. It is based on computer technology, control technology, communication technology and graphic display technology (i.e., 4C technology), and connects field control stations, control management stations, testing stations and operation management stations and engineer stations of operation and control centers which are distributed in the industrial site (nearby) through the communication network, and completes the decentralized control and the centralized operation and management in one integrated control system.

Batching control system is an automated and intelligent system solution to change the production batching process, utilizing dynamic weighing, PLC automatic intelligent control, computer information management and other technologies, which has the advantages of fast batching speed, high control accuracy, displaying and sharing of weight values, intuitive and dynamic display of the batching process screen, automated batching of a variety of materials, and flexible modification of formulas, etc. The system adopts an open control mode, and is compatible with all kinds of automation systems. The system adopts open control mode, strong compatibility, high flexibility, and can be connected to the enterprise information network, realizing real-time commonality of production data, and realizing the integration of production control and informationization.
Adopting the dynamic weighing technology of spiral scale, the material weighing precision is high, the digital weighing module has strong anti-interference ability, high detection accuracy, and the conveying material fully considers the uniformity and stability of the material flow. After dynamic weighing, the PLC controls the motor to realize automatic quantitative feeding, and the system adopts multiple inputs and multiple outputs to realize the coordination and real-time control of multiple materials and various batching and conveying lines, and timely and accurate monitoring and adjustment of material flow. It can realize the automation of complicated dosage of many kinds of materials, reduce the labor intensity, reduce the manual work and labor cost.
The feeding system adopts the centralized and decentralized control system (DCS). Each kind of material conveying line is controlled decentralized, but centralized management can be realized through the upper computer. Parameter setting and various management operations, including monitoring, alarming and processing, are realized through the upper computer, which improves the operability and reliability of the whole feeding system. In addition to the overall operation mode is different, all user-facing equipment pages in the system adopt man-machine dialogue, menu-guided operation, simple and easy to get started.
When the production process and the actual production formula change, the system formula parameters should be modified at any time, and the traditional dosage method has a certain lag and the formula modification process is cumbersome. With bulk dosage control system, new formula parameters are set in the upper computer, and the system automatically executes according to the new parameters, which is flexible and convenient. Recipe modification will also be recorded, convenient for future inquiries.
The system monitoring function is powerful, real-time collection, analysis and display of the actual situation on the scene, the manager can remotely through the host computer real-time, intuitive grasp of the production situation, equipment operation, shift information, and so on. For the system equipment operation automatic monitoring, when found operating faults or abnormalities, automatic alarm and record abnormal information to facilitate maintenance personnel to quickly troubleshoot the problem, minimize or avoid equipment failure to affect the production schedule.