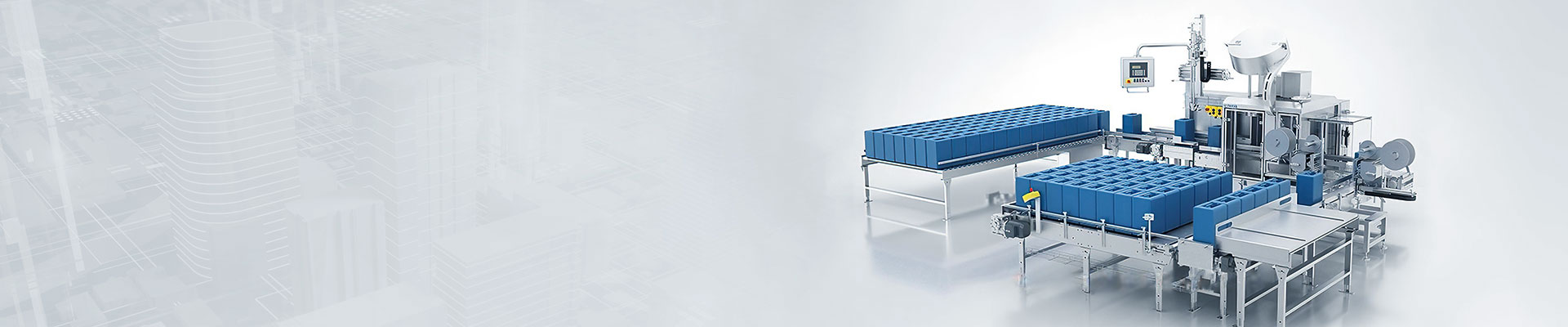
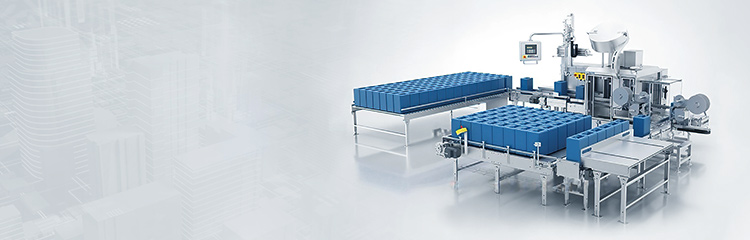
Reduction scale from the raw material delivery pump until the qualified materials sent to the reaction tank, which will include all the transmission and discharge valve control and interlock, each material delivery pump start and stop, fast and slow charging control, state detection, and all the data processing functions. It is composed of weighing unit, data processing unit and logic control unit, based on programmable intelligent module, industrial control computer and RS485 field bus to realize signal acquisition, processing, control and output, which constitutes a cost-effective bucket scale weighing system; and it adopts LAN to realize the communication between on-site monitoring computer and management computer.

Reduction scale weighing control system can make two or more different substances among each other dispersed and stirred, so as to achieve uniform mixing weighing and batching, but also can accelerate the process of heat and mass transfer. In industrial production, stirring operations began in the chemical industry, around the food, fiber, paper, oil, water treatment, etc., as part of the process is widely used. When the Electronic scale starts production, the PLC sends the dynamic metering start signal to the metering instrument, which then starts to collect and display the weight of each link, and uses the fast feed and slow feed strategies at different weight stages to take into account the need to improve efficiency and metering accuracy. When it reaches the target value, it outputs a stop measuring signal and closes the relevant valves and pumps of the reaction kettle under PLC control. At the same time, the action of unloading to the reaction tank is completed, and the metering instrument is automatically zeroed and tared.
Reduction system based on programmable intelligent module, industrial control computer and RS485 fieldbus to achieve the signal acquisition, processing, control and output, constitutes a cost-effective bucket scale Weighing system; the use of local area network (LAN) to achieve the field monitoring computer and the management of the communication between computers; the weighing system software using a modular approach to the use of VC + + + compiled. The actual operation shows that the system is reliable, easy to maintain and use, with friendly man-machine interface and good control effect. The weighing system will start from the feeding pump of raw materials until the qualified materials are sent to the material tank. It will include the control and interlocking of all feeding and discharging valves, the starting and stopping of each feeding pump, the control of fast and slow feeding, the status detection, and all the data processing functions. The dosing control system is composed of weighing unit, data processing unit and logic control unit.
At the end of dosage, the upper computer stores the actual data, analyzes them with certain accuracy and generates various reports for production statistics and management. According to the user's needs, online or offline printing of all kinds of required reports, such as the daily output of the finished product of the reaction tank, raw material consumption, raw material inventory, finished product inventory and so on.