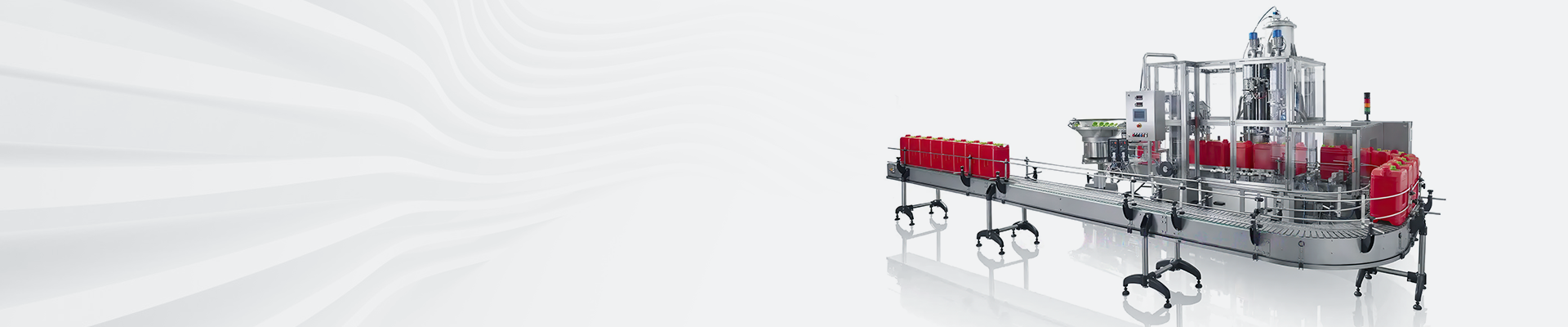
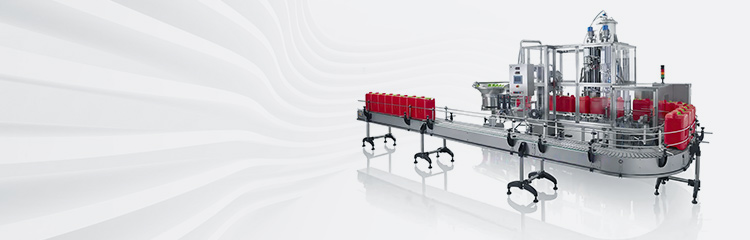

Summary:The weighing and batching machine adopts the "fast first, then slow, inching" control feeding method, deducting the weight (tare weight) of the hopper itself, and after the host computer issues the batching instruction, it will perform rapid feeding for a period of time after the batching is started. When the detection When the target value of rapid feeding is reached, slow feeding begins; when it is detected that the weight of the ingredients reaches the target value in advance, the feeding valves are all closed, and the target weight is reached by relying on the dead weight of the material.
High-precision automatic weighing system in industrial control is not only a single instrument to provide weight data, but also promotes the automation of industrial production and modernization of management as an integral part of industrial control system, and plays a role in shortening operation time, improving operation conditions, improving product quality, and strengthening enterprise management, and improving operation. Baosteel 3# silicon steel unit belongs to Baosteel independent integration unit. A large number of independently developed new processes and new technologies are used in this unit.
1 process flow
The process flow is as follows: when the liquid mixing process needs to be filled with the agent, the upper computer (HostPLC) sends weighing instructions and the amount of agent to be added to the weighing and batching machine. The weighing and batching machine above the hopper to accommodate the agent, weighing, from the entire weighing system to control the amount of agent added, when the amount added to reach the set amount, the weighing end, and the agent injected into the next level of the tank, and other agents mixed with the liquid distribution.
In this system, the main need to solve the following two key issues: batching machine weighing and dosing accuracy guarantee. The weighing and batching machine is controlled by the host computer (HostPLC) and communicates with the host computer, dispenses the liquid according to the time sequence and weight specified by the host computer, and gives real-time feedback on the actual weight weighed to the host computer.
2 System Composition
The high-precision automatic weighing control system is composed of feeding device, weighing and batching machine and weighing control instrument.
2.1 Feeding device
Due to the high weighing accuracy of the weighing and feeding system, the following control method is adopted for the feeding device to ensure the automatic weighing accuracy by controlling the feeding accuracy.
Weighing dosage machine adopts "first fast and then slow, point to move 's control of the feeding mode, deducting the weight of the dosage machine hopper itself (tare), in the upper computer dosage instruction in the beginning of a period of time, fast feeding, when the detection of the target value to reach the fast dosage, began to slow down the dosage; when the detection of the dosage weight to reach the target value of the amount of time ahead of time when the feed valve is closed all the way to rely on the material self-weight to reach the target weight. Rely on the self-weight of the material to reach the target weight. In the weighing control, the feed valve is set to "big open", "small open" and "close" three states "big open" state is mainly used for coarse precision dosing when the dosage weight reaches the target value, the feed valve is closed. State is mainly used for coarse precision charging when charging tends to be close to the set value, "small open" action, when the set value is completely reached, the feed valve "closed". In accordance with the above ideas, through the preparation of the software module to control the feeding of fast and slow feeding and pointing down the material, as well as in order to eliminate the influence of the air falling material on the weighing accuracy, the preparation of the software module to automatically find the amount of early stopping software and other software measures.
In order to make the upper computer can obtain the feeding valve state, install the limit switch at the feeding valve, feedback the feeding valve state open/close to the upper computer.
2.2 Weighing and batching machine
The working principle of the feeding system is as follows: weighing objects placed on the scale, under the action of gravity, the electromagnetic weighing module elastomer cattle deformation, so that the balance of the circuit is out of balance to produce current, in order to restore balance to the circuit, the need to provide the size of the reversal of the current is equal to the microprocessor inside the weighing and batching machine will be the current signal by amplification, filtering, A/D (analog/digital) converter transformed into a digital signal, the digital signal is transmitted to the instrument to be processed into a weight signal. The digital signal is transmitted to the instrument to be processed into a weight signal and the weighing data is shown directly on the JAGXTREME instrument display.
In order to ensure the weighing accuracy of the automatic batching machine, METTLER TOLEDO KB60.2 series weighing batching machine is used. Its main technical indicators are as follows.
Rated weighing capacity 60Kg.
Maximum safe overload 125%FS; Calibration index value 10g (static) reading stabilization time t<10s; Table size 400mm (L) x 400mm (W); Structure weighing platform all-steel structure: the base form desktop.
Total weight about 25Kg.
Precision OIML(II) grade.
Power supply 220VAC(-15%~+10%), 50Hz+2%.
KB60.2 weighing and batching system adopts METTLER TOLEDO's patented TB15 electromagnetic weighing module, each electromagnetic metering module has its own A/D converter and digital signal output interface. It eliminates the problem of transmitting low-voltage signals over long distances, and each digital weighing module has been all in the factory for a variety of digital compensation, such as range output, non-linearity, hysteresis, creep, temperature, etc. are adjusted to the best output. At the same time, the microprocessor controlling the digital signals is protected in a sealed environment, and wide temperature range components are selected for their anti-interference properties. As each electromagnetic balanced weighing module contains a microprocessor, a wealth of self-diagnostic functions make maintenance and setup easier and faster.
With the above configuration of the batching machine, the weighing accuracy of the display scale reaches 1g and the calibration scale value reaches 10g, which meets the control accuracy required by the process. The weighed weight of the batching machine KB60.2 is transmitted in real time to the control instrument JAGXTREME of the batching machine through the IDNET bus dedicated to METTLER TOLEDO.
2.3 Weighing control system
The weighing instruments are METTLER TOLEDO JAGXTREME controllers, which are mounted on the machine-side operation panel of the weighing batching machine.
In the whole weighing control system, the JAGXTREME controller is the core, and JAGXTREME communicates with the upper computer Melsec0 series PILC by RS-422, accepts the dosage instruction from the upper computer, and at the same time feeds back the actual weight of the weighing to the upper computer: JAGXTREME controls the feeding valve to add the material through external I/0 (PIO), and at the same time the feeding valve gives feedback to the PLC through the PIO. JAGXTREME controls the filling of the feed valve through external I/0 (PIO), at the same time the feed valve feeds back the status of the feed valve to the PLC through the PIO; the weighing and batching machine sends the weighed weight to the JAGXTREEM through the dedicated bus IDNET: the operating panel is connected to the JAGXTREME through the PIO and through the panel it chooses the way of working of the system (on-site/remote), when choosing the on-site way it allows to carry out the manual operation of the batching through the on-site panel, at the same time the JAGXTREME sends the At the same time, JAGXTREME sends the information about the operating status to the PLC through the PIO.
JAGXTREME consists of a control unit, a high precision unit and a multifunctional unit. On the control unit, there are two serial ports COM1/2, and this time the RS-422 interface is used to communicate with the upper computer. On the control unit, there are 4 independent input/output ports.
When the number of input/output signals on the control unit does not meet the control requirements, you can add a multifunctional unit to expand the number of input/output points. In addition, the multifunction control unit is equipped with COM3 and COM4 ports. Among them, COM3 provides all input and output handshaking signals and modem docking signals. COM3 is only used for the multifunction expansion board, while COM4 is connected in the same way as the RS-232 of COM2.
The high precision board is mainly used for the connection of the JAGXTREME meter to the weighing mixer KB60.2, which is connected using the IDNET network of METTLER TOLEDO.
Communication interfaces The weighing and control instrument JAGXTREME supports various interfaces such as RS-232, RS-422, RS-485 Profbus. In this project, RS-422 interface is used. The host computer is a Mitsubishi MELSEC series PLC, in the host computer, the use of MELSECOJ71C24 plug-ins to communicate with JAGXTREME where the data bits are transmitted using ASCII code. This technology weighing mixer control instrumentation using METLLER-TOLEDO's JAGUAR table, so RS-422 programming data format to JAGUAR system syntax and instructions for programming. Communication parameters baud rate 2400 / 8 data bits / no parity / 1 stop bit transmission data type ASCII. process parameters weighing set value for 0 ~ 5000 g. Data transmission format to accept the upper computer dosage value and to the upper computer to send the weight of the current weighing are realized using JAGXTREME special instructions.
When the upper computer sends the dosage value, the following format is used (the serial port of the instrument does not answer, the IO port is used to answer)
AW323001$$
(target weight L)~(unit)~$$
(Fast charging weight Lm2)~(unit)~$$
(Tolerance value)~(unit)~$$
(Advance Lm)~(unit)~$$
~0D0A
Where, ~ indicates a space, when the data bit is less than 4 bits before the complementary space 0DOA for the end of the flag.
If the host computer transmits a target weight target weight L is 1000g fast refill weight L is 600g, tolerance value is 20g, and lead time Lm is 40g. the following statement is used.
AW323001$$1000~g~$$~600~g~$$~~20~g$$~~40~g~$$~0D0A
The following condition is satisfied between the data: target value > (fast dosage value + advance). In the secondary table of the weighing and batching machine, judgment is made for the above conditions. When the above conditions are not satisfied, the system reports error and waits for reset to re-receive the command from the upper computer.
When sending the current weight data to the upper computer, the following format is used to send the real-time weight: AB+Weight data+g~0DOA, the weight data is fixed to 4 digits, less than 4 digits before the complementary space programming language.
The weighing control instruments are programmed in JagBASIC, the language dedicated to JAGXTREME. On the basis of retaining the standard JAGXTREME instrument program, it enables the user to use JagBASIC to have the ability to develop applications for JAGXTREME, and enables the user to program JagBASIC to match the tasks of the control instrument JAGXTREME instrument.
Weighing batching machine operation mode and control process weighing batching machine should be designed for local (Local) and remote (Remote) mode, usually use remote (Remote) mode to accept the upper computer control for automatic liquid dispensing; when there are abnormalities in communication with the upper computer, you can use the local (Local) mode to manually dispense the liquid in the field.
Manual mode
When the mode selection is Local, the control instrument of K agent automatic dosage system informs the upper computer PLC (DCS) that it is in Local. At this time, the manual dosage value is input according to the weighing target value, the fast dosage value and the advance amount, and each data input needs to be confirmed manually. If confirm, select current input cancel, then automatically return to the previous step. When all the values are input, the target value, fast dosage value and advance quantity will be displayed. If the input is confirmed, the dosage process will be started manually by pressing the SupplyStart button: in the process of dosage, if any abnormal situation occurs, it can be terminated manually by pressing the EmergencyStop button; if there is no abnormality, the dosage speed will be switched to the slow dosage gear when the fast dosage value is reached and the advance quantity will be reached, the dosage will be stopped. Advance amount, the dosage stops, relying on the self-weight of the dosage, first into the final dosage.
When the mode selection for Remote, K agent dosage system control instrument panel operation is invalid, by the upper computer PIC (DCS) to send dosage data and start and emergency stop signal. The control process is as follows: the weighing control system detects whether there is an interrupt request generated, when the interrupt request is generated, it determines whether it is the upper computer that sends the dosage data, otherwise it returns to the previous process. After receiving the dosage data, on the one hand, clear the buffer, at the same time, judge whether the last round of weighing is completed and whether the dosage data sent is valid or not (target value > fast dosage value + advance)), such as the data is valid, the dosage is carried out, or else judge that there is an error in the dosage data and the end of the dosage data. In the process of dosage, detect whether the upper computer queries the current weighing weight, if it is in the query state, then upload the weighing weight and clear, buffer, wait for the next query. If the process of dosage is abnormally terminated, it ends. Otherwise the dosage is terminated normally after reaching the advance quantity and ends normally.
3 Conclusion
Through the use of a large number of self-developed new processes and technologies, the application of high-precision weighing and batching machine in Baosteel's 3# silicon steel batching system has been successfully realized, and its accuracy fully meets the process requirements and achieves the expected results. It shortens the operation time, improves the operation conditions, improves the product quality, and promotes the automation of industrial production and modernization of management.