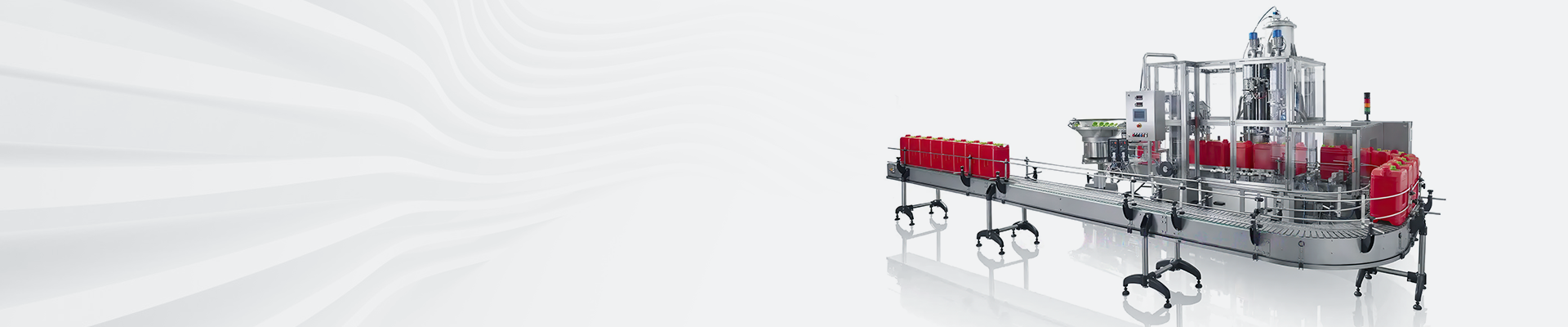
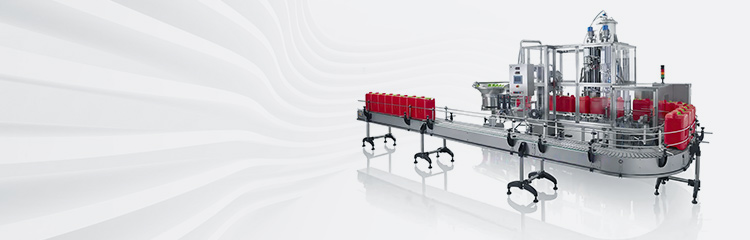

Summary:The automated batching system adopts PID-regulated frequency conversion technology. The feeding task is mainly controlled by the proportion input and calculation from the host computer. That is, the process parameters of various raw materials are input into the computer, and the computer directly sets and prepares the various materials. Than coordination.
The traditional batching process mainly relies on work experience to regulate, there are the following aspects of the problem:
1, can not be adjusted at the right time, the production efficiency is low.
2, due to the lack of measuring and dosing equipment, human influence factors are more, the material can not be well controlled, waste phenomenon is serious, the production cost is greatly increased, the failure rate is more, resulting in a large number of waste products.
3, due to the material dust pollution is more serious, seriously affect the health of workers. In recent years, the degree of automation of industrial processes is getting higher and higher and people's awareness of environmental protection is increasing, frequency conversion technology with its excellent performance, widely used at home and abroad.
Main functions and characteristics of dosing
Main functions of dosing
Monitoring function: detects and monitors the instantaneous flow rate, daily, monthly and yearly totalization of the dosage process of the screw weigher;
Screen display: through the computer monitor, it can display the operation status of the control parameters in the dosage process, as well as display real-time dosage curves and tables;
Printing management: dosage reports can be printed at any time for storage and inquiry;
Communication function: two-way data and information exchange between the industrial computer, PLC and meters;
Data processing: the collected signals can be automatically operated and processed, and output to the corresponding control quantity;
Control function: according to the corresponding set value before operation, the normal operation of dosage equipment, including PID regulation;
Alarm function: the upper computer alarms the various parameters exceeding the limit or the abnormal equipment status by means of screen and sound and light signals.
Main features of dosage
Small and medium-sized centralized system is adopted in the structure of automatic batching system, which realizes "decentralized control and centralized management" and overcomes the problem of "dangerous concentration";
The upper and lower machines are relatively independent. With manual, automatic, semi-automatic switching function, online, each other according to a specific protocol to share information, offline, a single scale can be independently realized process closed-loop process control;
The upper computer is far away from the operation site, which improves the stability of the methanol automated batching system and the working environment of the operator;
The lower computer uses programmable controller, which has strong anti-interference ability, simple programming and easy to master, and can operate reliably for a long time in the harsh environment;
The dosing control system adopts PID regulation to improve the dosing accuracy, according to the production requirements of the best work switching time sequence, to solve the problem of material head and material tail, and automatically modify the material ratio of dosing;
Dosing structure
The feeding system consists of a set of PLC system and a set of upper computer monitoring system, PLC system consists of STEC series controller and weighing instrument and communication cable, Ethernet communication between STEC controllers, controllers also provide RS232, RS485 interfaces and ADSL, GPRS, CDMA, fiber optic and other communications, the upper computer monitoring Windows operating system, the installation of batching programming software and HOM. Installation of dosage programming software and HOMS5.0 configuration software.
Batching principle
Upper computer: real-time monitoring, screen display and report printing for the whole wetting agent weighing and batching system;
PLC: realize the automatic control of dosage;
Dosage meter: used for PID regulation of dosage and display of instantaneous and cumulative flow and other parameters;
Control cabinet: for dosage logic control and power supply and distribution;
On-site manual control box: for start/stop control of single batching equipment on site.
Operation mode of dosage: each dosage scale is equipped with manual, semi-automatic and automatic control modes. When manual, the change-over switches of the on-site control box and the weighing instrument box will be played to the manual position, and the control will be realized by the start-stop buttons, potentiometers, and frequency meters on the on-site control box, and the weighing instrument will display the instantaneous and cumulative quantities of the materials. It is mainly used for emergency operation in case of network system failure, PLC system failure or other reasons, which requires manual overhauling and commissioning. When semi-automatic, the conversion switch of the field control box and weighing instrument box will be set to automatic position, and the control will be realized by the start/stop button on the field control box, the frequency meter and the weighing instrument, etc. The formula set by the weighing instrument will automatically adjust the batching quantity, and display the instantaneous and cumulative quantity of the material; and the formula can be set through the operation screen on the site to adjust the quantity of the material. It is mainly used to realize on-site operation when no upper position control is needed. When it is fully automatic, the change-over switch of the weighing instrument box will be played to the linkage position, and the upper computer will control the starting and stopping of the screw, and dynamically display the amount of each material, the operation status of the screw, and all kinds of alarm indications, and the amount of each ingredient will be uniformly set by the upper computer according to the requirements of the process, and it can collect and deal with weighing signals and switching status of the ingredient control circuits, so that it can realize the whole screw feeding, weighing detection, and the adjustment of material amount, and selection and switching.
Start and stop of operation
Four types: sequential start, sequential stop, emergency stop and simultaneous start.
Sequential start: the initial start of the dosage or the restart of the dosage system after a sequential stop. The sequential start function can control the feeding equipment participating in the dosage to start sequentially at certain time intervals in accordance with the running direction of the screw to ensure that the material heads can be aligned.
Sequential stop: this function is used when a long stop is desired, so as to ensure that the material on the conveying screw is transported cleanly, so that the screw is in the material state, and to ensure that the ends of the material are aligned.
Emergency stop: for emergency situations where all the dosage equipment involved stops immediately.
Simultaneous start: This is used to restart the machine after an emergency stop, so that the dosage can continue to run at the previous "break point", as if nothing had happened.
Note: The four buttons cannot be clicked randomly and without order, but must be operated according to the operating requirements.
Control of material quantity
When the required proportion of a certain amount of material is determined, it will be input into the upper computer as the set value and transmitted to the weighing instrument through the network. When the material falls on the weighing screw, its weight is detected by the weighing module, and the feedback voltage signal of the material flow (measured value) is obtained to the weighing control instrument and operated to become the current value of PV, and then the 4-20mA control signal is output to the frequency converter through the PID operation to change the output value of U/F, so as to change the speed of the screw to control the size of the material quantity, and to realize the automatic dosage.
Control of material proportioning: This dosage feeding task is mainly controlled by the proportion input and calculation from the upper computer, i.e. the process parameters of various raw materials are inputted into the computer, and the computer directly coordinates the setting and proportioning of various materials. When the upper computer has problems.