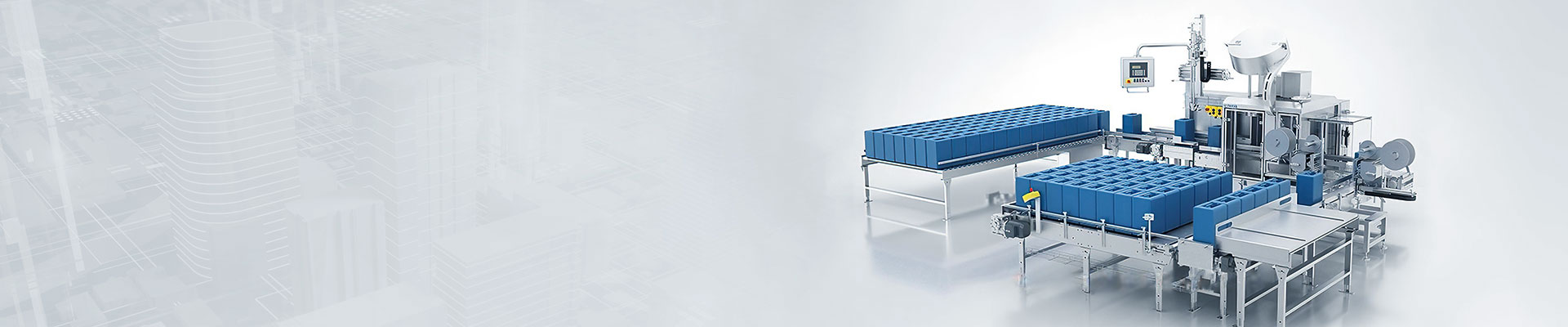
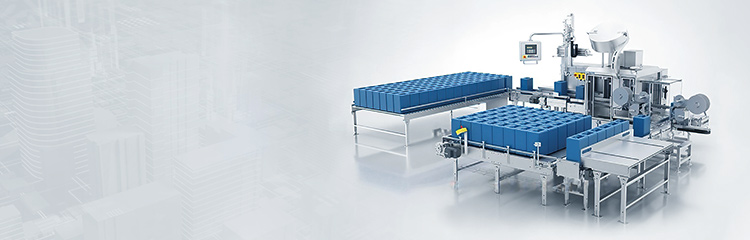
The reaction pot weighing system converts the digital signal into digital signal through internal amplification A/D and transmits the digital signal to the CAN bus through the communication sub-module. The instantaneous flow rate of the material can be measured, and the analog signal from the weighing module and the motor frequency conversion speed regulation can be received in the system, and the instantaneous flow rate and cumulative flow rate can be displayed after integration. At the same time, the instantaneous flow is sent to the computer system with 4~20mA analog current signal as the input signal, and the computer compares the signal with the set value and outputs 4~20mA analog current signal through the inverter to control the speed of the feeding motor, realizing the closed-loop control of the material discharge flow.

The feeding system is a complete set of automation equipment to realize dynamic weighing and dosage control through electrical control management and visualization man-machine software configuration. The electrical control part of the system adopts Siemens PLC, which is programmed according to the production requirements; the software adopts man-machine configuration, which controls the weight and flow of the materials loaded into the weighing hopper according to the process requirements through the monitoring system and the PLC program, so as to realize accurate weighing and dosage. With strong stability and high cost performance, the system can provide accurate measurement data and control means for production control and management of various industrial sites. Reaction pot Weighing system composition of the type of weighing instrument by the display control module and weighing module composed of CAN bus connection data, sensor data acquisition module continuously collects the sensor analog voltage signals, through the internal amplification A/D conversion into digital signals and digital signals through the communication sub-module to the CAN bus to go up through the instantaneous flow of the measured material, in the system to accept the analog signals from the weighing module and the motor frequency conversion and speed control. The system accepts the analog signal from the weighing module and the motor frequency conversion speed control, displays the instantaneous flow rate and the cumulative flow rate after calculation, and at the same time, the instantaneous flow rate will be sent to the computer system as an input signal with 4~20mA analog current signal, the computer will compare the signal with the set value and output the 4~20mA analog current signal through the frequency converter to control the speed of the feeding motor to achieve the closed-loop control of the flow rate of the material under the material.
The Dosage system adopts a stainless steel sensor and stainless steel hopper to form a 20Kg small weighing dosage hopper, and another stainless steel tank and a carbon steel scale to form a 300Kg deionized water weighing tank. The small batching hopper and deionized water weighing hopper can be operated at the same time, and both of them can automatically derive the dosage amount. The solid and liquid materials are mixed according to the recipe requirements, the mixing process, the order and amount of material and water, the number of batches of material and water added to each additive tank according to the recipe requirements, add the appropriate amount of deionized water, and do a good job of total control of all the mixed materials and deionized water transported to the corresponding additive tank. The system is equipped with 6 stainless steel raw material storage hoppers of which 4 are used for solid materials and 2 for liquid materials, the solid materials are fed by electric vibration Feeder and precision control, and the feeding of liquid materials is controlled by gas-controlled ball valves. Small weighing hopper dosage is completed by adding a small amount of (by the program to control the amount of water) many times deionized water to dissolve the material and many times the output, the discharge is equipped with an automatic angle valve. The deionized water weighing tank is equipped with an automatic angle valve for water inlet and an automatic angle valve for water outlet. Select the auxiliary tank (1 out of 8) manually and open the corresponding hand valve while confirming that the hand valve of other auxiliary tanks is closed, start the pump according to the program setting, and transfer the water and the mixed material to the auxiliary tank.
The main control part of the weighing system is placed in an electric control cabinet, with load cell (small weighing hopper), W6000L weighing tank (deionized water weighing tank) and LD.AS industrial weighing terminal, and Siemens S7-200 PLC system is placed in the electric control cabinet, and the PLC communicates with Siemens touch screen through the communication port by using the MPI communication method. The touch screen displays the running status of the material and the selection of the recipe. The friendly man-machine interface makes it more convenient for users to use. Users can deposit the recipe according to their needs, and when they need to use the recipe, they can use the relevant parameters by calling the corresponding recipe number, instead of inputting the parameters one by one, which simplifies the user's operation. After the formula is selected, the formula program is started, PLC controls the whole dosage process, automatically starts the automatic feeding equipment according to the formula sequence and stops it according to the preset value, automatically opens the feeding valve and pump to send the material to the auxiliary cylinder, and stores the data related to each dosage.