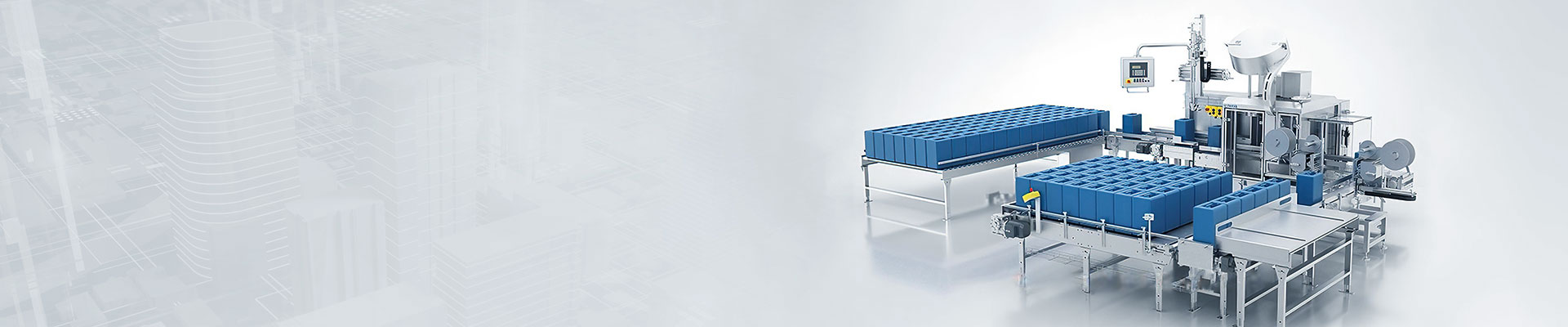
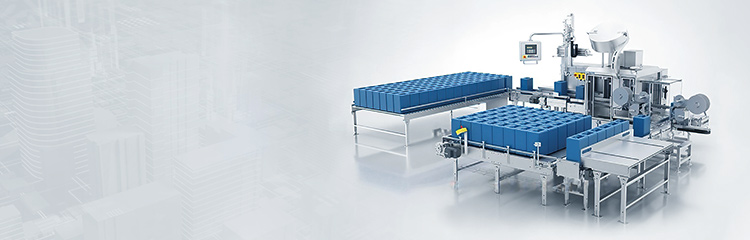
Reaction pot weighing system to be weighed after the start of the weight signal and speed signal to the weighing instrument, through the amplification of the A/D conversion, calculated instantaneous flow and cumulative amount, and displayed in the field weighing instrument. The indicator uploads the signals to the PLC module, the PLC analog input module collects the weight signals and speed signals from the screw and feeding device, and carries out the self-tuning operation according to the parameters set by the user, and the level weight of the materials in the reaction tank measured by the weighing module of the reaction tank regulates the flow rate of each downstream port of the dosage reaction tank, so as to guarantee the balance of the inlet and outlet of the mixing and storage tanks.

Weighing control system is a kind of batching equipment widely used in industrial production, indicating and controlling the material level in the silo or tank by weighing, and displaying it directly in the form of weight. Silo weighing has the advantages of intuitive display, simple structure, stable operation, high reliability, simple and convenient operation and maintenance. It can be applied to both intermittent control and measurement or batching of lumpy, powdery or liquid raw materials, and continuous control and measurement of lumpy, powdery or liquid raw materials. As a result of the characteristics of the material, from the top of the silo after charging the material in the silo or tank formed on the top of the material state is diverse, such as in the silo or tank body liquid top layer produced foam layer. Contact or non-contact level meter may not be able to truly reflect the bin or tank material level situation. And according to the level of the estimated volume is difficult to be accurate, so the use of Weighing system, to be weighed after the start of weight signals and speed signals sent to the weighing instrument, through the amplification of the A/D converter, the calculation of the instantaneous flow and the cumulative volume, and displayed in the field weighing instrument. The weight indicator uploads the signals to PLC module, the PLC analog input module collects the weight signal and speed signal of the screw and feeding device, and carries out the self-tuning operation according to the parameters set by the user, and the level weight of the materials in the reaction tank measured by the weighing module of the reaction tank carries out the flow rate adjustment of the downward feeding ports of the dosage tanks, so as to ensure the balance of the inward and outward materials in the mixing storage tanks.
Automatic dosage machine is a dosage control for different types of materials (solid or liquid) for conveying, proportioning, heating, mixing and packaging of finished products and other whole production process, using PLC control and novel frequency conversion feeding mechanism, with the dosage control software package, to achieve the material transfer, dosage control, recipe design, production data management and other functions. And it can realize the aggregate control of multiple batching through network.
The feeding system reads the main totalization, instantaneous flow rate, set flow rate, weighing instrument status and other related data from the weighing instrument. Weighing instrument status display (zero state, interval state, running state or alarm state), online monitoring and management by computer, with high requirements on weighing speed, weighing accuracy, system compatibility and expandability.
In the automatic feeding system in the middle layer or different layers of the bus dosage equipment are used between digital signals for communication, while a pair of wires can be realized on the transmission of multiple signals (including a number of operating parameter values, a number of dosage equipment status, fault information), a large number of reduced wires and connecting accessories to improve the reliability of the system and the ability of anti-jamming.
The dosage controller is connected to the upper computer and the on-site weighing instrument, reads the formula data sent by the upper computer and returns the real-time data, collects the on-site weighing data sent by the on-site weighing instrument, and controls the on-site actuator to carry out the weighing action. The on-site weighing instrument converts the signals from the pressure weighing module into standard signals, connects to the bus through the bus interface of the weighing instrument, and transmits the weighing data to PLC, which carries out the corresponding control according to the received data. The field actuator is controlled by the controller and works according to the instruction to realize the functions of feeding, unloading, receiving and rotating the turntable.