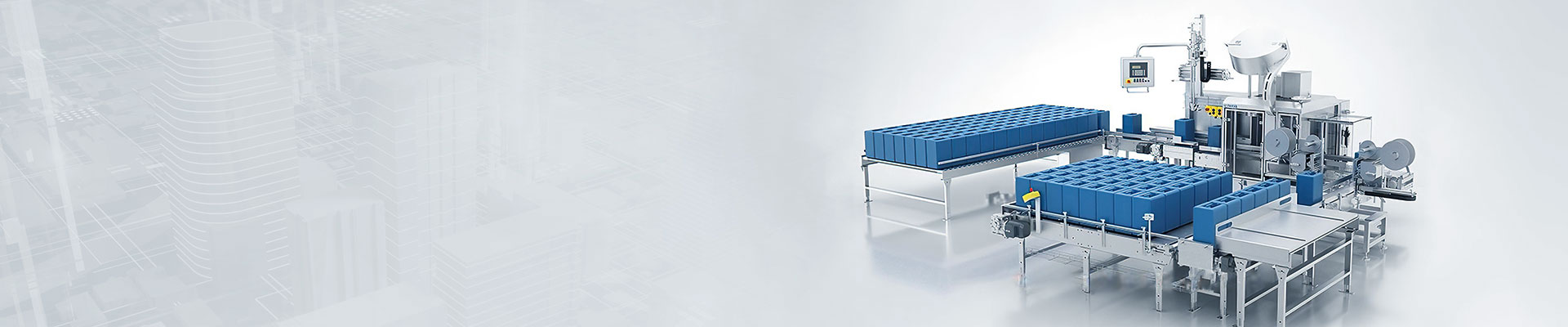
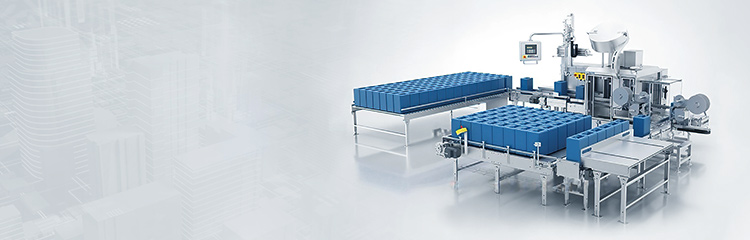
The automatic mixer communicates with PLC through serial port. According to the actual process of dosage process in the form of dynamic screen to reflect the feeding, dosage, feeding and related equipment operating status, operation when there is an overrun fault, alarm prompts, and start the alarm (sound, light) alarm, or shutdown, or change the warehouse, according to the operating data to make the state of the control analysis, with a different color bar graph to reflect the system's dynamic dosage process. According to the operation data, it can give the ratio or feeding quantity, and truly reflect the dosage status. Batching also has other functions, such as shift report, daily report, monthly report, annual report and other functions. It provides convenient management.

Automatic mixer for rubber, plastics, food, feed, pharmaceutical and other industries, intelligent automatic high-precision materials (granular, powder, flake) metering Feeding machine; the feeding system using electromagnetic vibration, double (single) spiral feeding and other feeding methods and continuous stepless speed control intelligent control device, multiple Electronic scales set up individually, individually driven, shared with the automatic dosage and mixing system consists of a weighing and mixing machine with a A set of PLC, touch screen and a number of accessories; mixing machine has a factory more machine docking supporting. Mixer through the 485 communication with the computer connected to a network, for the company's unified management provides a convenient platform.
Weighing mixer production line dosing part: powder tank, auxiliary material tank, reaction tank, screw Feeder, screw mixer, weighing tank, and a number of pneumatic/manual valves, etc.; production line mixer automatic control part of a set of PLC and touch screen to control the site of the storage tank of the low level of material signals, screw feeder alarm signals, feed valve/discharge valve level signals mixer start signals or the site of the manual feed and discharge signals into the PLC input. The signal of weighing module is inputted into PLC through the 16-bit high precision A/D converter module of PLC, and PLC can automatically control the whole batching and weighing process, data processing and alarm output of Weighing system through the preparation of program. The data parameters and operation of dosage are directly controlled by touch screen interface. The feeding system is connected to the computer as a network through 485 communication module, and the computer monitors the weighing system and processes the data.
Key Features:
It adopts U-shape barrel structure, smooth running, even mixing, no dead angle, clean discharging, and wide range of applications.
Adopting internal and external double-layer screw belt staggered back and forth mixing, fast mixing speed, high uniformity
The bearings are at both ends of the mixer, so the material is not easy to enter and the maintenance rate is low.
Screw conveyor is easy to feed, the feed opening is flush with the ground, feeding labor-saving and convenient.
The internal structure and the overall design of the materials used have passed the ISO9001 international quality system certification.
Realize remote control and after-sales support to improve management level.
Adopting high resolution electronic scale and weighing instrument, high weighing precision.
Multi-station simultaneous metering and dosing, continuous dosing capacity of 400-600 bags/shift, high production efficiency.
All key components are imported and joint venture brands, stable and reliable.
Fieldbus working system (i.e. setting PLC sub-station), automatically detects the operation situation, gives the alarm position and prompts the solution when there is an abnormality, which is convenient for overhauling and maintenance.
Rectangular cyclic transportation assembly line arrangement, open Chinese and English human-machine interface, multi-area display, monitoring and operation functions of the system operation process, easy to use.
Automatically detects system operation, gives alarm location and suggests solutions when abnormalities occur.
Low energy consumption design with safety chain protection measures to ensure energy saving and safety.
Optimize the design of dust recovery system, configure single machine bag filter, no dust flying and leakage, good operating environment, no waste of raw materials.
Flexible arrangement (can be arranged in 1 or 2 layers, suitable for 6-24 kinds of materials), wide applicability, can be adapted to different user requirements.