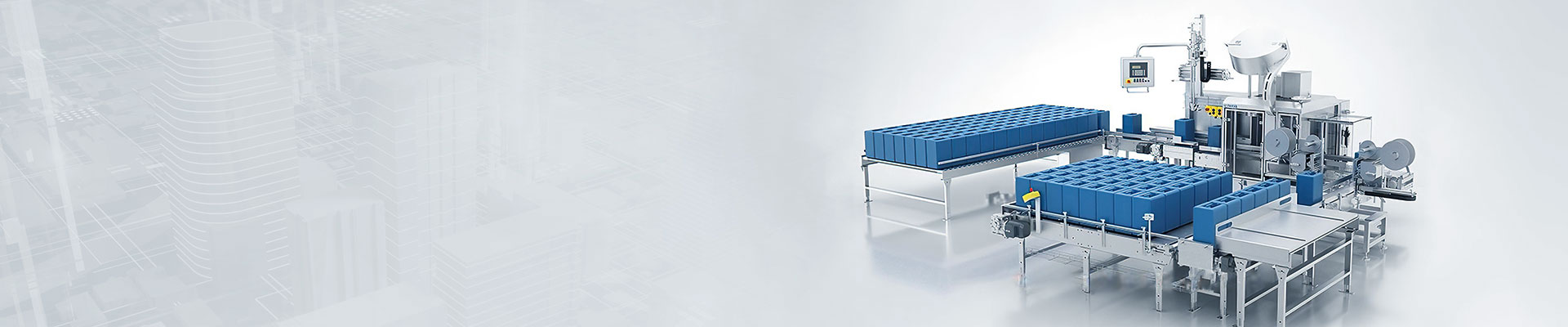
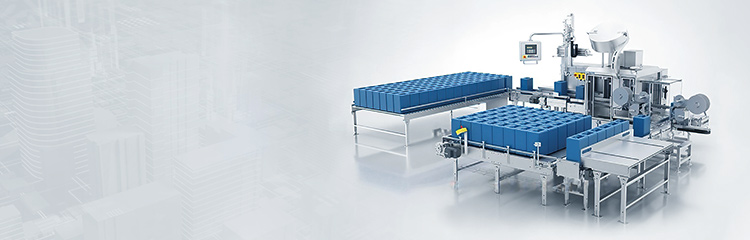
Metering feeding equipment collection storage body, conveying body, weighing dosing body, dust removal body, material mix and other equipment, dosing according to the characteristics of the industry, reasonable selection of "zero method" or "reduction method" weighing methods, according to the actual need to adjust the spiral speed, so as to achieve normal dosing. After measuring by electronic balance, it enters the feed tank of spiral pneumatic conveying, and pushes forward into the mixing tank through the spiral mechanism.

The feeding equipment is composed of PLC, weighing instrument, weighing module and signal distributor, PLC is used to configure the switching control such as starting and stopping and the opening and closing of the warehouse door, the state detection of the warehouse door and the running configuration, and the implementation of system interlocking of the Dosage system. the PLC and the weighing control instrument are connected with the I/O principle, and directly join the dosage control. PLC and weighing control instrument are connected by I/O, directly joining the batching control. It has the results of weighing signal collection, fast and slow adding control and self-tuning of overshooting, etc. It can modify the input and parameters of material side. Each scale is equipped with three Weighing modules, whose signals are sent to the distributor, connected to the bridge wall in parallel, and sent to the weighing control instrument by voltage division.
A centralized control console is set up at the production site, the weighing instrument is installed on the console, the data line of the weighing module installed at the lower part of the supporting leg of the batching machine is connected to the dynamic weighing instrument, the real-time data is uploaded to the industrial control machine of the control center by the weighing instrument through the communication line, and the formula and the control commands are downloaded to the electronic weighing instrument and the PLC controller by the industrial control machine of the control center through the communication line.
The materials will be fed into the mixing tank from the respective material level loader, and the small materials will be pre-mixed and fed into the small material bin. When the lower limit of the reaction tank bin alarm, the dosage system begins to start, the first screw conveyor, feeding system, feeding system start in sequence, while the weighing control instrument according to the formula to start dosage. Start batching and hopper door off in place interlock, that is, the material door off before allowing the start of batching. If the hopper door can not be closed in place within a certain period of time after the signal is given, the PLC will generate an alarm, prompting the maintenance personnel to maintain and repair the hopper door. The dosage is divided into fast and slow addition. Fast plus is the alleged mass is not close to the material side of the agile charging, if the flow rate does not reach the specified flow rate, the mixing tank began to vibrate until it reaches the specified flow rate; slow plus is the alleged mass of the alleged mass is close to the material side of the beginning of the slow charging, this time does not allow the silo vibration. When the three weighing bins weighing is completed, to PLC pleading discharge, in the material door closed in place under the environment, allowing the dosage weighing controller to control the discharge. Discharge is completed by the PLC control off the material door, the material door are closed in place after the PLC allowed to match the next kind of material. Mixing and stirring by PLC timing control, mixer always mixing, mixing quantitative addition of liquid, the bin must be in the temporary storage hopper door off (temporary storage hopper if there is a weighing scale) and the scale is empty when the release of material. The hopper will start to release material after the bin is closed in place. External storage tanks and in-plant silos start to feed the belt conveyor after a delay, and the amount of material to be fed is controlled by the opening of the material door. The starting and stopping of the external storage tanks and the in-plant silo are controlled according to the start and end of the discharge from the hopper. All controls are interlocked by the PLC, which controls the starting and stopping.