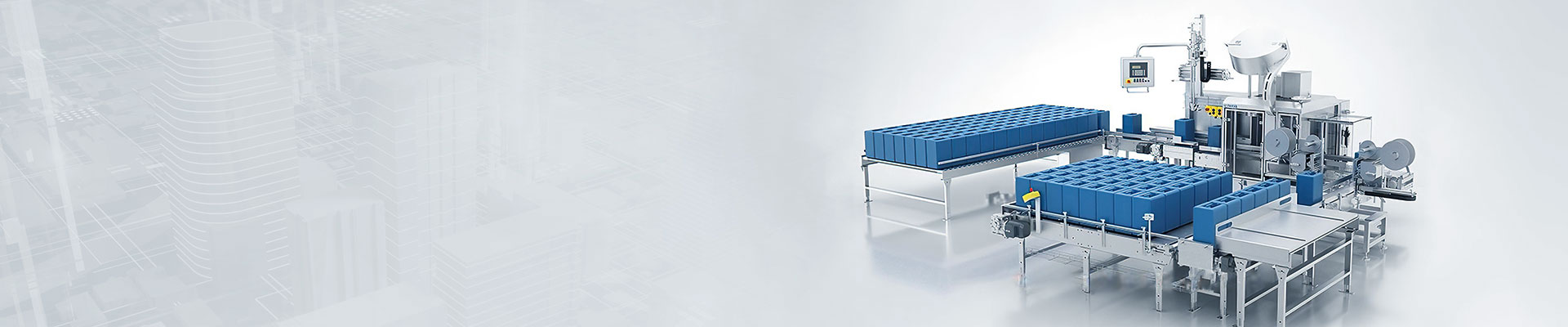
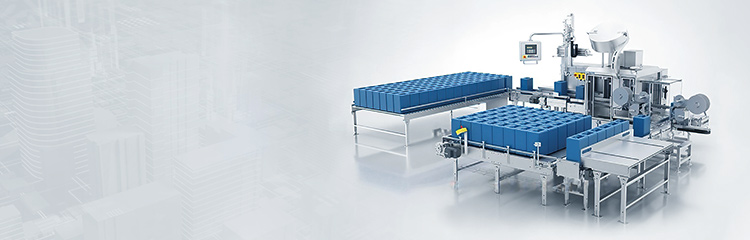
The automatic batching system ensures the real-time communication between the upper PC and PLC, directly collects the weight signal through the electronic weighing, and automatically controls the weighing. The operator input the feeding information (feeding type, weight, etc.) on the HMI of the upper computer through the keyboard or mouse, monitors the whole process of feeding control, and prints the feeding results and production reports. It is a practical and effective method to realize the integration of measurement, control and management in feeding process.

The overall composition of the Dosage system host and the slave (including virtual host) connected through the serial bus, the virtual host and the slave is also connected through the serial bus, constituting a dual-bus structure of the master-slave microcomputer dosage, the host through the serial president to achieve the dosage of the control, while the virtual host in the acquisition of the right to control the system, the dosage through the serial bus to achieve the control of the host to complete the process control, real-time display and alarm, provide data storage, reporting and printing, recipe optimization and management consulting functions. The host mainly accomplishes the functions of process control, real-time working condition display and alarm, data storage, report printing, formula optimization and management consulting.
The dosing system can quickly and accurately complete the quasi-dynamic measurement of liquid and powder materials, can simultaneously carry out real-time quality testing of a variety of liquids and powders, with real-time monitoring of all aspects of production, data collection, statistics, reports, printing and other functions, can be manually or automatically and accurately complete the scheduled charging, inverter mixing, material to the finished product tanks, finished product tanks, tank barrels, tank trucks and so on. It is widely used in mixing and other industries for precise measurement and automatic control of feeding, filling and pipeline transportation.
Weighing and batching equipment design features:
1、the use of continuous dynamic measurement of solid, liquid powder material quantitative measurement, can be fast and slow casting control, not only to improve accuracy, but also to ensure production efficiency.
2、Centralized control by operator console, configuration software development, can quickly respond to changes in customer demand, friendly man-machine interface, the operator can monitor the working status of the production line in the control room, improve efficiency and the speed of dealing with abnormal situations;
3、Centralized installation of weighing instrument makes communication with monitoring software and PLC more convenient, safe and reliable;
4、production management software is powerful, can complete a variety of production formula management, process control, abnormal alarm and production data collection, storage, report analysis, printing;
5、easy to upgrade and expand, the user needs to expand the existing system, only the system's newly installed sensor leads, valve control line into the control room, and in the software interface to increase the corresponding function module can be, simple and fast.
6、with tank pressure, liquid level detection, in the raw material tank can be installed level meter, load cell, centralized control center on the liquid level, pressure and other real-time monitoring, to avoid accidents.