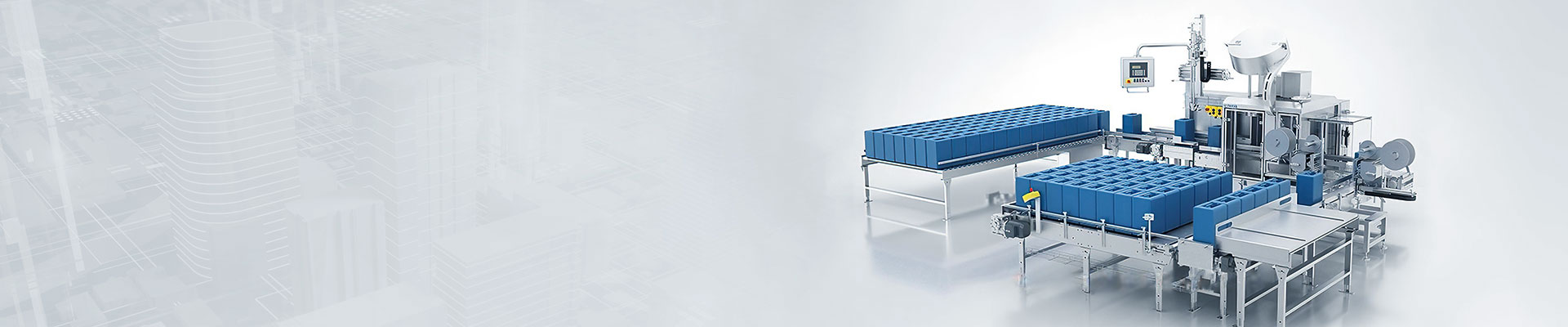
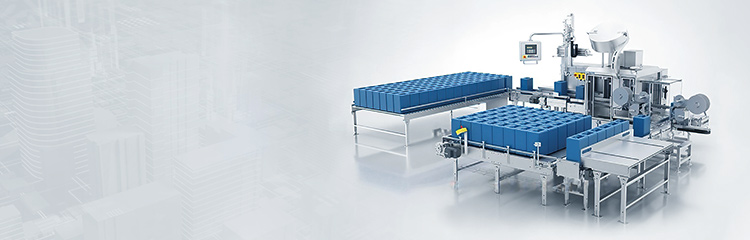
The oil filling machine has the nitrogen filling amount can be adjusted by controlling the time, the nitrogen filling valve is closed after a certain amount of nitrogen is filled, and the tare weight is automatically removed from the empty bucket of the scale, and then the fast and slow charging ball valve is opened at the same time. It can display information such as target quantity, filling quantity, number of barrels, time and date, provide human-computer interaction interface, complete the functions of controlling information input, data management, data display, storage, statistics and reports.

Liquid filling scale uses the most widely used in industrial control to adjust the weight for actual control, according to the weight deviation, through the frequency converter to adjust the speed of the Electronic scale, adjust the quantity, so that it is equal to the set value, complete the automatic filling process. PLC is mainly responsible for the selection of manual/automatic processing process, the judgment of entering liquid level processing, the display processing of alarm lamp and the control cycle under various fault states. Liquid level processing is mainly responsible for judging the height of the liquid level in the material reaction tank by comparing the collected numerical information of the liquid level with the set value, and the high and low signal of the liquid level will determine the opening and closing state of the material pump. When the input value collected by the Filling machine exceeds the maximum allowable value of the set liquid level, it will automatically limit it to a reasonable range to avoid abnormal situations.
The main control system of the weighing and filling machine uses the main control element made by PLC, the detection sensor such as photoelectric and proximity switch as the external input signal, and the servo motor and the action cylinder as the output component. The filling production line has the function of online real-time monitoring of products, and has the function of input of product information. The computer is connected with PLC through serial communication, which can collect data in real time and carry out data processing and data entry and storage of the production line. The control function is implemented by hardware relay. The relay is connected in the control circuit according to the change of voltage, current, speed, time and temperature in the main circuit, which realizes the automatic control and protection of the electric drive device.