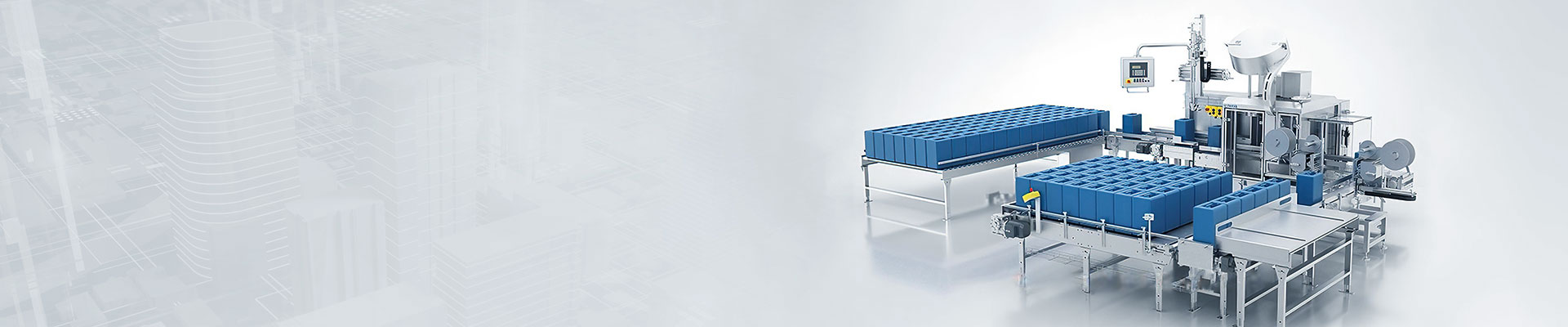
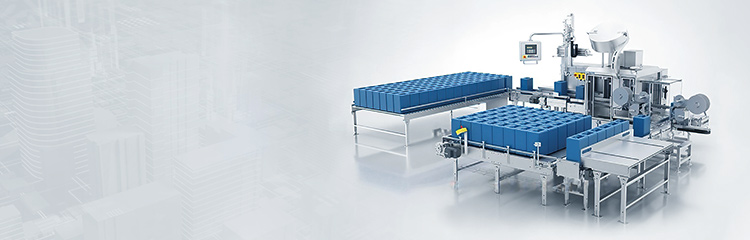
Mixing equipment consists of touch screen and bus module. Among them, the touch screen mainly completes the setting of process parameters, the system's motor rate, etc.; displays the gravity of each tank and the historical parameters, and displays the system's operating status. Including inverter current, fault code, etc. RS232 port to establish point to point communication. The main function is to complete the scanning of the module to get the gravity signal on site. And according to the requirements of the process parameters for a variety of PID operation after the output control signal to the bus output function.

Weighing and Batching system in line with the production process, you need to according to different varieties, according to the pre-determined formula, a variety of different raw materials in proportion to the mixing. The batching machine is divided into feeding part and batching part. The feeding part is mainly composed of screw machine, elevator, mixer, conveyor and distributor. The batching part includes silo, Feeder, Electronic scale and mixer. The main function of the dosing part is that after the feeding equipment puts all kinds of different raw materials into their respective hoppers, the materials are discharged into the weighing hopper in accordance with the given proportion of the formula and weighed, and then sent into the mixer for a certain period of time for stirring and mixing uniformly into the finished products. Various fixed formulas are inputted into the touch screen beforehand, and the touch screen controls the discharging, weighing and mixing according to the proportion of the formulas, and detects the signals of the weighing module in real time, makes a judgment, and sends out commands to the various actuators of the batching, so as to realize the automation of the batching. The whole production system is equipped with manual control auxiliary mechanism, which can control the operation according to automatic or manual working mode.
The dosage control system mainly includes the system hardware and software of the industrial control machine, as well as the electrical equipment corresponding to the sampling, detecting, alarming and other actuators. The system has the following main functions:
Human-computer interaction and management: the functions embodied in human-computer interaction and management are an important aspect of the performance of real-time control system. This system has the ability to process Chinese information and adopts Chinese prompts in the menu mode. The operator can select and perform various operations by function Casgood or cursor movement. The system provides a fixed recipe library. There are as many as 100 kinds of formulas. The operator can query, modify or assign a working formula to the stored formula, and can also input and erase a formula temporarily. The system has dynamic display and printing functions. In the process of dosage touch screen can display the dosage control flow chart on the CRT screen, and use the cursor for dynamic indication, and can display the title and dosage weight etc. at the same time, so that the operator can understand the dosage situation at a glance. The printer can print in Chinese. Explosion-proof electronic weighbridge system can provide various production information reports to the production management department.
Real-time detection and control: the system can collect the weighing signal of each dosage weigher in real time, automatically tare, automatically calibrate zero and automatically correct the error, and select and control the material according to the specified formula ratio and relevant algorithms, and judge at any time, send out switching signals to the corresponding feeder, electronic weighing door and mixing machine door.
State test and alarm: in the process of batching the controlled equipment running state detection, timely detection of problems is an important guarantee of safe production. Batching dynamically detects the status of drive motor, travel switch and other equipments of each feeder and weighing door, and alarms immediately once errors and failures are found.
On-site data protection: The system has a data protection zone in the touch screen. The touch screen puts the current recipe data and other important data in the dosage in the protection zone, if there is a sudden power failure or system failure and needs to be shut down, the data in the protection zone will not be lost. The dosage can be resumed when the site is restored.