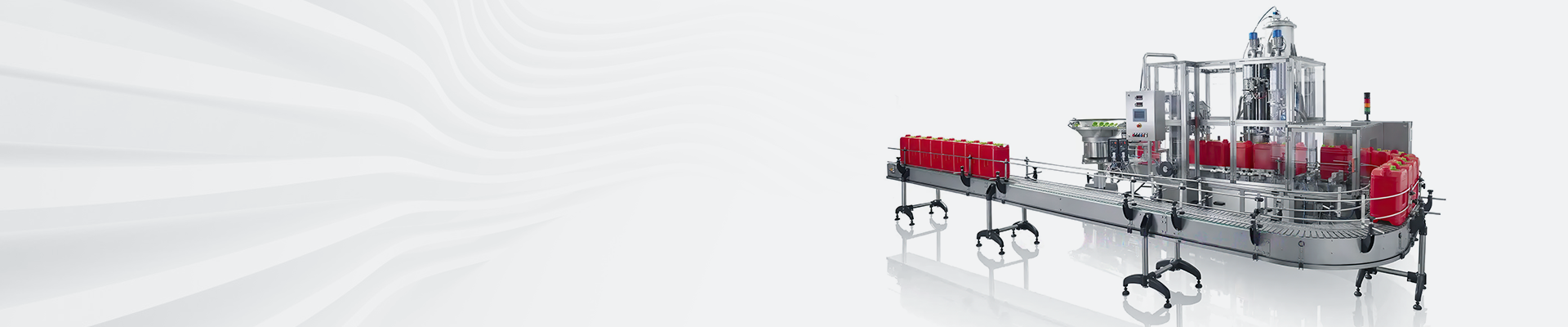
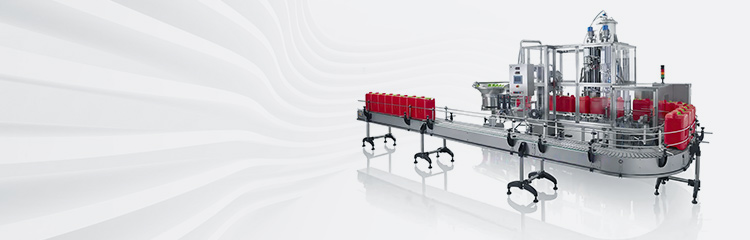

Summary:The batching machine refers to a predetermined mass ratio, which is transported to the hopper scale through a belt weighing device. The batching operation is completed automatically through PLC control. The movement of the mobile electrical equipment (travel control, electro-hydraulic push rod) is controlled by the ground part through the digital transmission equipment. Giving control instructions improves the advancement and simplicity of ingredients.
I. Introduction
Batching machine refers to the pre-given mass ratio, the weighing of several substances in the weighed material for the dosage measurement of the scale. Its use is very wide, can be used for a variety of materials dosage measurement, can also be used for a material measurement.
The following is a local feed production enterprises in the use of a batching machine as an example to discuss how to improve the batching machine weighing and measuring accuracy. Batching process is a key link in the production process of feed manufacturers, batching is a specific batching device, according to the requirements of the feed formula, a variety of different varieties of feed ingredients for accurate weighing process. The core equipment of the batching device is the batching machine. The performance of the dosage scale will directly affect the quality of the dosage. In the use of mixer, people usually use the dosing accuracy to evaluate the performance of dosing scale. Dosing accuracy is actually a description of the proximity of the weighing results to the true value, that is, a reflection of the dosage system error and random error. The use of computer control for weighing and batching, weighing errors can be automatically compensated to ensure the accuracy of the batching, but also through the computer for man-machine dialogue, to complete the parameter settings, process settings, monitoring the weighing process, fault alarms, and a series of control functions, through the management program to automatically complete the control of the weighing and batching system. Therefore, the use of computer-controlled weighing and batching system can reduce the consumption of raw materials, improve product quality and realize the scientific management of the production process.
Second, the automatic batching system process requirements
(A) process requirements
In order to ensure good dosage effect, in the design and use of the dosage device, the general requirements are: a. Good stability can realize fast, accurate weighing. b. In order to ensure the dosage accuracy, should be simple structure, reliable use, easy maintenance. c. The dosage system should be easy to use, reliable, easy maintenance. d. The dosage system should be easy to use, reliable, easy maintenance, easy maintenance, easy maintenance.
(ii) batching machine measurement performance analysis
Batching machine is a widely used industrial scale. In actual use, it should not only meet the basic performance requirements of the scale, but also meet the process requirements of the production process. Its measurement performance can be divided into static performance and dynamic performance.
(1)Static measurement performance
Static measurement performance is the batching machine in the non-automatic weighing state measurement performance, in fact, the batching machine itself measurement performance. The static measurement performance of the batching machine is in non-automatic weighing state, with all non-automatic scales, must have the correctness, sensitivity, stability, repeatability and other basic measurement performance. However, for automatic weighing with the help of weighing modules, the specific descriptions of the above properties often have many differences. Correctness of a scale is the property of the weighing system to be accurate and reliable during the transfer and conversion of forces. In the case of a batching plant, it refers to the accuracy and reliability of the force-electric conversion of the load cells and the processing of the results by the measuring and displaying instruments. The correctness of a scale is expressed in terms of correctness, i.e. the magnitude of the systematic error in the weighing result. The correctness of a doser is usually a combination of the systematic error of the weighing module and the measuring and displaying instrument.
(2) Dynamic measurement performance
Dynamic metrological performance is the metrological performance shown in the automatic weighing process, i.e. the metrological performance of the batching machine and its ancillary devices in the working state. For the working state of the batching machine is the most important automatic weighing process measurement performance. However, the basic performance of the batching machine itself often affects the measurement performance in different forms and to different degrees, so it is the basis of the measurement performance. The dynamic metrological performance of the batching plant is mainly concentrated on the dosage accuracy. Batching accuracy reflects the batching machine and its ancillary equipment in the batching weighing of accurate and sensitive, stable and reliable characteristics of batching accuracy with batching accuracy. It refers to the hopper scale is weighed in the actual mass of the material value and the dosage system for the material set the theoretical mass value of the difference between. The difference between these two values is also referred to as the dosage error in production practice. Dosage error reflects the dosage system work of the systematic error and random error sum. Batching machine dosage accuracy in the automatic weighing process is mainly reflected in the stability of the material supply, the accuracy of a single weighing, weighing the correctness of the cumulative weighing and weighing the reliability of the action of the stability of the material supply is the realization of the premise of the weighing of the accuracy of the process is the key to the dynamic measurement process. Batching machine feeding characteristics: a variety of materials through the corresponding feeder sequential feeding, each feeder feeding process operation and termination are subject to computer control, the weighing display on the meter is with the changes in the amount of feed and the continuous accumulation of the value. Feeding weighing process is a stage of continuous feeding, static display of the results, many times alternately accumulated complex dynamic process, the resulting "air column" is an important part of the dosage error, and fast, slow the implementation of the second feeding program is to reduce or eliminate the basic means of this random error.
The correctness of the weighing totalization reflects the comprehensive characteristics of the measuring and displaying instrument. This sum can be a material in different batches in the weighing results of the sum; can be the same batch of materials in different materials being weighed mass of the sum; can also be the weighing error, dosage error of the sum. The correctness of the weighing totalization not only reflects the accuracy, sensitivity and stability of the measuring and displaying instrument itself, but also reflects the coordination between it and the weighing module. This coordinated link reflects the quality of the signal can be weighed in the exclusion of a variety of external interference (such as mechanical vibration, power supply fluctuations, external electromagnetic fields, ambient temperature, etc.) in the case of the correct results to the display. The reliability of the weighing action reflects the rationality of the structure of the entire measurement and dosage system, manufacturing and installation of the correctness of the weighing action of the coordination of several aspects of the comprehensive effect. Weighing and dosing system is composed of a set of mechanical and electrical devices. The structure of the feeder form and working mode, the structure of the hopper scale and the capacity of the form, the bottom of the door control mechanism of the structure of the form, feeding, weighing and unloading links in the self-locking mechanism and interlocking mechanism must be considered in the design process. The manufacturing and assembly quality of the various mechanisms, hopper scales, weighing modules, the correct installation is the key to the operation of the feeding system. Feeder to realize fast and slow secondary feeding, feeding speed can be adjusted, weighing time can be guaranteed, batching and weighing process control in an orderly manner is to improve the accuracy of batching and weighing important means.
Third, improve the feeding system accuracy of the basic ideas and modeling
(A) Improve the basic idea of feeding system accuracy
In order to improve the production efficiency and weighing accuracy, the system should be equipped with fast weighing and slow weighing. The flow of material out of the fast weighing bin is large, and the flow of material out of the slow weighing bin is small. In order to compensate for the zero drift of the load cell and preamplifier, zero tracking of the electronic scale is required.
In batching weighing, the actual weighing value often deviates from the required target value. When the positive deviation exceeds a certain value, overweighing occurs. Therefore, it is necessary to reduce the amount of unloading when unloading, so that the actual proportioning error is limited to the permissible error range. When the negative deviation exceeds a certain value, underweighing is generated and the system has to continue weighing to make up the weighing value. At the same time, the linear error tracking method is used to automatically correct the advance of the next weighing to improve the weighing accuracy of the next scale.
Because of the mixing and discharging time are longer, in order to further improve the productivity, when the mixer into the mixing at the same time, it will start the next weighing. In silos and hopper scales where different varieties of materials are stored, the materials are prone to clumping, resulting in material retention. Therefore, the system requires flow monitoring of materials that are prone to clumping, and when the flow is insufficient, a broken arch jitter is issued and an alarm is given at the same time.
(B) the establishment of the weighing model
(1) Incremental weighing model
The weighing process of the system is the process of continuous feeding to the hopper scale, when the weighing value of various materials is equal to the closing value, the feeding will be stopped, and after a period of delay, after all the fallout into the hopper scale, the actual weighing value will be measured, and the weighing error will be calculated at the same time, which will be used for the automatic correction of the advance when the next weighing is done.
(2) Accumulation type weighing model
Since all kinds of materials share a hopper scale, so at the end of each material weighing, according to the weighing value of the next material as well as the closing value of the correction to continue to weigh the target value and the closing value, and at the same time to calculate the actual weighing value of each material and weighing error. Set a certain kind of feed by 8 kinds of materials mixed together, according to the process requirements first with the first kind of material to the amount given, the first kind of material dosage stop. Then with the second material, - .... -, until the last kind of material. To be all the material after the completion of the mixer, the computer to detect the mixer, after receiving the signal to be material. It will command the solenoid valve and conveyor feed to the feed mixer, then the analog screen corresponding indicator light, the end of a dosage cycle. The computer repeats the above process. If the dosage, due to accidental circumstances, a certain material more than the given range, the computer can automatically compensate for several other materials in proportion to ensure that the ratio does not change.
(3) Reduction type unloading weighing model
When the end of material weighing, first calculate a variety of materials to reduce the amount of unloading shutdown value, and then according to a certain time sequence, successively open the hopper scales for unloading, when left in the hopper scales of the weight of the material and its shutdown value is equal to the weight of the material to stop unloading, measure the actual unloading value and unloading weighing error, according to the error range and then dealt with separately. A material in the weighing of the existence of over-weighing. When unloading according to the reduction type unloading, so that the formation of part of the material to stay in the hopper scales, so that the actual amount of unloading is limited to the permitted range of error, which is overweight processing. The material left in the hopper scale is used as the pre-weighing value for the next weighing. Among the above three types of weighing modules, incremental weighing module and decremental unloading weighing module are suitable for one bin one scale dosage system, and cumulative weighing module is suitable for multi-bin one scale dosage system.
Other measures to improve weighing accuracy and reliability
(A) the use of variable speed weighing method
Reduce the material flow is to improve the weighing accuracy of one of the effective methods, but this will prolong the weighing time of the system, reduce efficiency, so take the variable speed weighing method, not only to improve productivity, but also to improve the weighing accuracy. Variable speed weighing method is the beginning of high-speed feeding, when the material in the hopper scale reaches a certain value, the equipment is transferred to low-speed feeding.
(ii) Dynamic advance tracking
After the end of each weighing, the actual measurement of the hopper scale in the material weight value will be compared with the required target value, calculated the error, the error will be compensated to the next measurement of the closing value for the next weighing, affecting the amount of advance of more factors, it is with the structure of the weighing device, the level of the level of high and low, the fluidity of the material, the pneumatic door closure device of the pressure changes as well as the fatigue of the electromechanical equipment are directly related to the degree of fatigue. But as long as the above factors change slowly, the use of advance tracking method is still the most effective.
(C) the sampling frequency is an integer multiple of the industrial frequency
Each time the sampling time and the frequency voltage to maintain a synchronized relationship, so that the size of the frequency interference is fixed, and this as the zero value of weighing, can effectively eliminate the frequency interference. If the use of precision regulated power supply for the preamplifier and the A/D converter board is powered separately, the effect of eliminating industrial frequency interference will be better. But consider the performance-price ratio.
(D) multi-power supply
Digital interface circuits can share a set of DC power supply, preamplifier and A/D converter boards are powered separately, so as to avoid mutual influence due to fluctuations in the power supply load. (E) A/D conversion function
Make full use of the voltage range of A/D conversion, and increase the voltage amplification of the preamplifier as much as possible so that the analog voltage to be converted is as large as possible, which can reduce the relative error of A/D conversion.
(F) many times to verify the weighing value
When the weighing value is greater than or equal to the closing value of the repeated verification of the value of the size, if three consecutive times and three times are the same result, it is judged that the weighing of the validity of this time, so as to prevent interference with the error generated.
(G) Power failure protection measures
The system should be equipped with an uninterruptible power supply, once the power grid power failure, the computer will save the main parameters to disk, to be after the incoming call, the program according to the parameters of the characteristics of the automatic execution.
V. Conclusion
Adopting microcomputer and establishing weighing and batching control model can automatically compensate the weighing error, ensure the accuracy of the batching, monitor the production process of weighing and batching, and find out the faults in time and alarm. Through the established model to automatically complete the weighing and batching system control system model design has automatic compensation, advance tracking, zero tracking, multiple vibration feeding by approximation and over and under weighing processing and other precision control methods, can achieve high control accuracy, enhance the adaptability of the system to the changing industrial site, improve the reliability of the system.