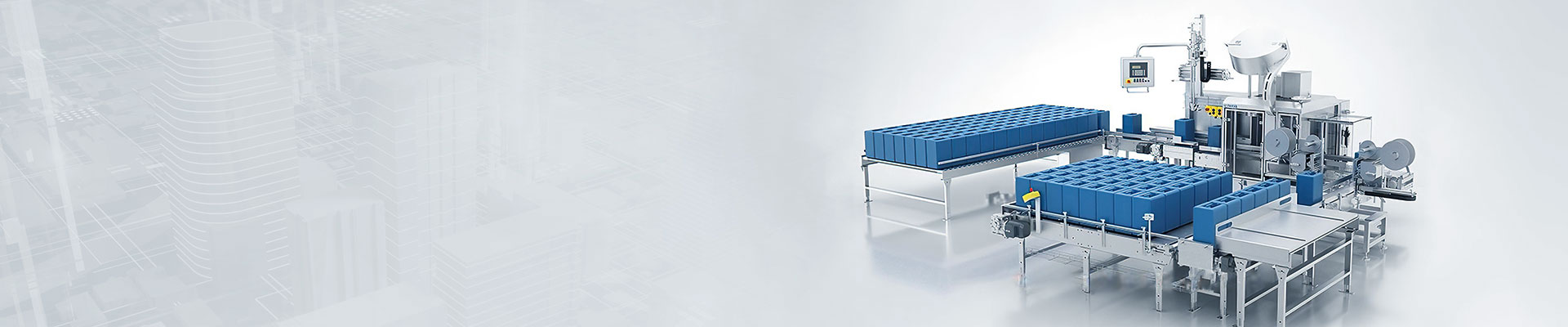
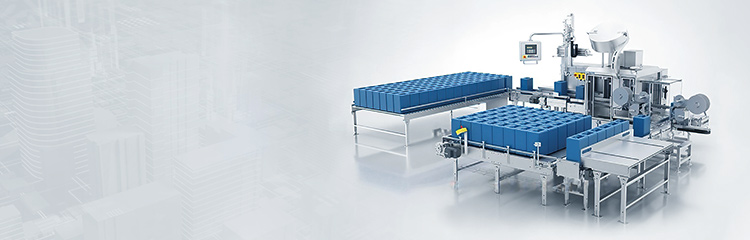
The automatic canning scale fills the material directly into the packaging bucket through the set quantity of the filling nozzle, and the bucket will be transferred to the next link through the power track. Through the professional manipulator, the filled packaging drum is accurately absorbed and placed into the set tray. When the number of paint drums in the tray reaches the specified number, the robot will automatically transport the tray placed in the bucket to the specified position.

Automatic canning scale adopts intermediate relay as conversion to realize the control of solenoid valve and pump. In the manual / automatic switching is realized through the two-position selection button, followed by the start, manual filling is realized through the button. I / 0 allocation of the Filling system, the need for switching individual input, analog input signal real-time collection of filling quality, switching output to control the action of the pump and solenoid valve, the PLC system has two ways of working, the use of the main program to call the structure of the subroutine, to reduce the scanning time, the conversion of the measured value, the external reason for stopping and emergency stops, and so on.
Automatic Filling machine using configuration software for monitoring interface design, the software can quickly components and generate the upper computer monitoring system, through the data acquisition and processing of the scene, to animation display, alarm processing, process control. Real-time curve, historical curve and report output and so on in many ways.
Filling system through the screen real-time display of the current filling quality, the number of filling barrels and other on-site work status, in the upper computer can carry out the corresponding operation, through the interface for the filling mode selection and start, stop and other buttons operation. It is possible to change the filling quality, the number of barrels and manually remove the tare (i.e., the quality of the filled bottles) when using different filling barrels. In order to realize the above monitoring requirements, the monitoring interface simulates the dynamic filling process with Haniwa effect and fast flow attribute settings.
The filling machine realizes manual/automatic selection, starting, stopping, emergency stop and manual opening of pumps and solenoid valves by adding standard buttons: realizes real-time display of filling quality setting, setting of number of filling barrels and displaying the current number of filling barrels by setting the display output attributes of labels, etc. Configuration monitoring screen monitors the operating status of the filling system, and realizes the purpose of monitoring PLC operation by operating on the touch screen, and establishes connection between the system and external hardware devices, enabling MCGS to read data from external devices and control the working status of external devices. The connection between the system and external hardware devices enables MCGS to read data from external devices and control the working status of external devices, realizing real-time monitoring of the filling process.
Basic parameters:
Maximum weighing capacity: 30kg
Minimum Sensitivity: 0.1kg
Filling error: ±0.1-0.2kg
Filling speed: 20L about 1500-1800 barrels/hour
Control mode: 2-speed control
Filling method: insertion type, liquid level up
Gun head line: Teflon gun head, valve + Teflon hose
Structure material: host SUS304 stainless steel, conveying palletizing carbon steel anticorrosion paint.
Weighing platform size: 400 × 800mm (304 stainless steel power raceway)
Empty barrel raceway: 400mm × 2500mm (304 stainless steel power raceway) with another 1200mm slope without power roller
Heavy drum raceway: 400mm×2500mm (304 stainless steel power raceway, 2 sets)
Separate barrel device: for 20L barrels, carbon steel anticorrosive paint structure, 304 stainless steel raceway.
Palletizing equipment: pan-transfer type, suitable for pallets 1200×1200×140mm, including supplying pallets, palletizing, and lower pallet conveying.
Pipe pressure: 0.2-0.6MPa (related to material properties).
Material interface: DN40 flange connector 4, according to the user to provide interface standards
Air Connection: User supplied 12mm air hose connector for quick coupling connection
Power supply: AC220/50Hz (user-supplied to one side of the machine)
Using air source: 0.4-0.8Mpa (provided by the user to the side of the machine)
Use temperature: -10℃-50℃
Base condition: Horizontal solid concrete floor, concrete thickness should be more than 10cm.
Optional models: standard, explosion-proof filling scale