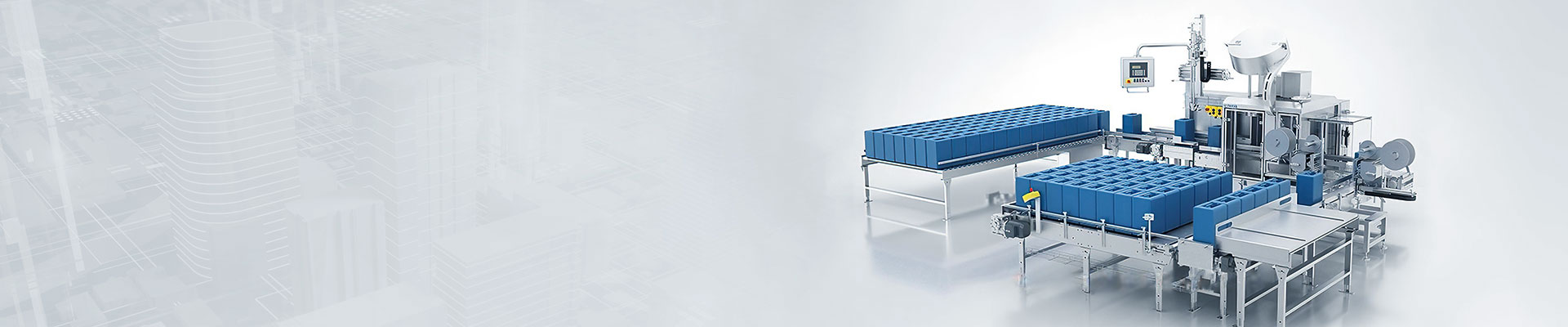
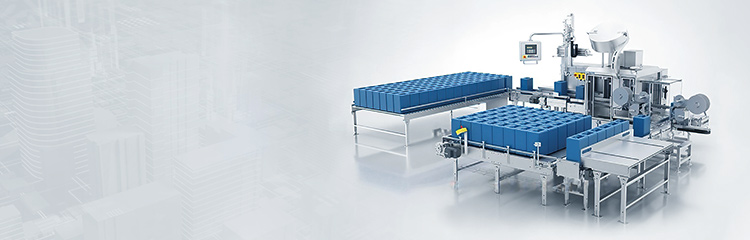
The detergent filling machine is combined with bottle preheating/rinsing device and capper/sealer in a two-stage filling method. When the filling head is not inserted into the bucket, it automatically lifts the grab and when it reaches the filling target value, the filling head automatically raises. The new filling valve allows for faster and cleaner filling. Gravity-assisted inflow into the bottle through vacuum. Vacuum enables 100% drip-free filling of low-viscosity products.

The interface of real-time parameter monitoring, alarm, test data summarization and historical data query of the automatic Filling machine can directly reflect the real-time operation data of the Filling system. The on-site filling interface automatically adjusts the weight and sends it to the host computer according to the set operating parameters. The upper computer reads the data sent by each on-site measurement and control unit. Adopting special filling control instrument with double window display, it can display target volume, filling volume, barrel number, time and date, etc. The controller can store 30 groups of filling value parameters, which can be called only when using, and the controller has self-diagnostic function and interface test function.
Liquid filling machine using programmable recipe controller automatically mixes two liquids, performs different action recipe control outputs for different states, so as to realize the cyclic recipe control of AB two liquids mixing, using photoelectric and proximity switches and other detection sensors as external input signals, servo motors, action cylinders and so on, as the output components. At the same time, it has the function of on-line real-time monitoring of products and the function of entering product information. The computer is connected to the PLC through serial communication, which can collect data in real time and carry out the data processing of production line and data entry and saving.
Liquid filling machine sequentially completes the steps of:pail loading, pail feeding, loading, feeding, filling, pail discharging, capping, sealing, palletizing and so on. During normal operation, when the filling equipment meets the interlocking switch closure, air pressure conditions, liquid level conditions and other external transmission number is normal, the equipment should be in automatic operation mode after pressing the start switch, each station on the filling line will be scanned and executed in accordance with the program programmed in the PLC of the filling system in a circular manner.
Basic parameters:
Maximum weighing capacity: 30kg
Minimum Sensitivity: 0.01kg
Filling error: ±0.01-0.02kg
Filling speed: 20L about 150-180 barrels/hour
Control mode: 2-speed control
Filling method: Insertion, liquid level up
Gun head line: Teflon gun head, valve + Teflon hose
Structure material: host SUS304 stainless steel, conveying palletizing carbon steel anticorrosion paint.
Weighing platform size: 400 × 800mm (304 stainless steel power raceway)
Empty barrel raceway: 400mm × 2500mm (304 stainless steel power raceway) with another 1200mm slope without power roller
Heavy drum raceway: 400mm×2500mm (304 stainless steel power raceway, 2 sets)
Separate barrel device: for 20L barrels, carbon steel anticorrosive paint structure, 304 stainless steel raceway.
Palletizing equipment: pan-transfer type, suitable for pallets 1200×1200×140mm, including supplying pallets, palletizing, and lower pallet conveying.
Pipe pressure: 0.2-0.6MPa (related to material properties).
Material interface: DN40 flange connector 4, according to the user to provide interface standards
Air Connection: User supplied 12mm air hose connector for quick coupling connection
Power supply: AC220/50Hz (user-supplied to one side of the machine)
Using air source: 0.4-0.8Mpa (provided by the user to the side of the machine)
Use temperature: -10℃-50℃
Base conditions: solid concrete floor of the assistant suspension agent flat, concrete thickness should be more than 10cm.
Optional models: standard, explosion-proof filling