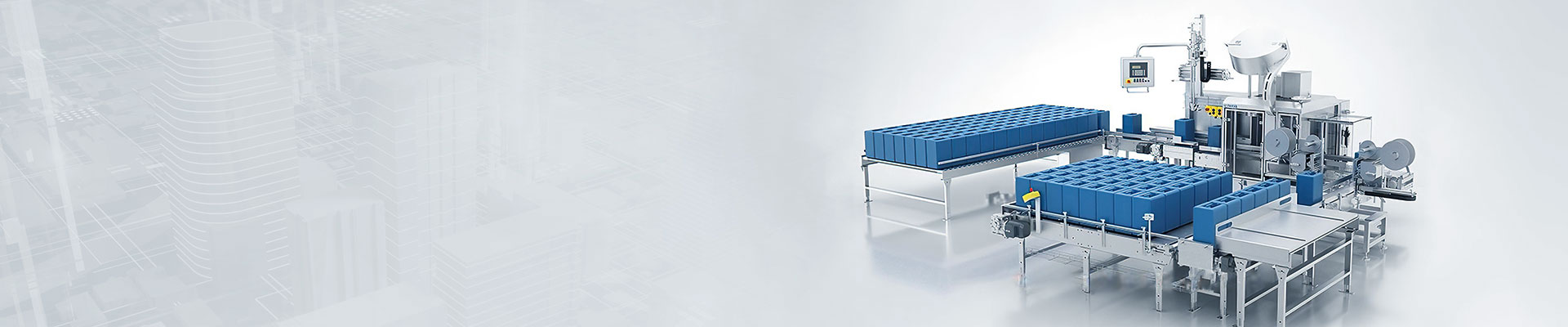
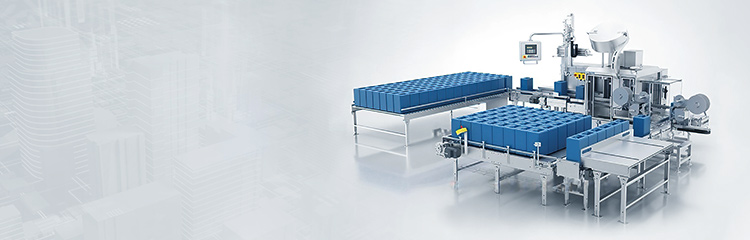
Detergent filling machine for the barrel identity of the weight collection, for the upper computer database for the barrel identity and regulation identification, each filling weight can be arbitrarily changed according to the need to use high-precision all-electronic weight detection weighing and measuring, in order to control the barrel of raw materials for the filling of filling operations, the degree of automation is high, you can try to avoid the overflow of materials, and maximize the prevention of pollution of the material itself on the environment.

Automatic Filling machine filling line work by their respective filling head, each filling head is equipped with their own measuring device to ensure the accuracy of the filling quality. In the whole filling line there are many groups of filling points, can be completed separately a variety of different products (materials) filling (production only 1 product filling). The filling machine on each filling point is equipped with multiple filling heads, which can independently complete the filling and metering of multiple barrels at the same time. When working, the empty barrels are put into the conveyor, transported to the filling position, positioned and locked by the relevant mechanism, and after the empty barrels are all in place detected by the detection device, the filling head automatically descends and is inserted into the mouth of the barrel. The filling control valve and filling valve will be opened at the same time, and the material will be filled through the filling gun, filling control valve (fully open) and filling valve, and the weighing module will start to measure at the same time. When the filling reaches the set value (a certain percentage of the filling volume), the filling control valve receives a signal, the opening becomes smaller, and the flow of material through the filling control valve decreases, until the completion of the exact filling volume. The signal is sent after the filling is completed, and the filling control valve and filling valve close quickly at the same time. Then the filling head lifts up and opens the locking and positioning device to complete the filling.
After filling, the product is transported to the capping station by the conveyor to complete the capping process. After the capping is finished, the barrels are sent to the designated position by the conveyor, and the pneumatic pusher pushes the barrels into the labeling station to finish the labeling process. Finally, the barrels are manually put into the pallet on the roller conveyor for palletizing, and after palletizing, the barrels are sent into the winding machine together with the pallet to complete the winding and packaging.
The weighing and filling machine is characterized by simple structure, high reliability and accurate measurement. Among them, the filling head is the key component, and the filling valve diameter corresponding to different barrel types varies. After the filling is completed, to prevent the material left on the surface of the filling head from causing pollution of the surface of the packaging container and the environment of the packaging place, it is required not to drip. The filling head has a special design in structure, the head surface is smooth cone surface, which is convenient for the residual liquid to be concentrated in the top of the cone after filling, and then the residual liquid will be sucked into the residual liquid collector through the small holes in the top of the cone, to ensure that there is no dripping after filling. The material to be filled is food grade, in order to prevent the material from being contaminated, all the movements of the filling head are pneumatically controlled, and its parts and seals are selected according to food grade.
The filling head must accurately complete the rising, descending, opening and closing actions during the filling work. Rising and falling are controlled by the main cylinder; opening and closing are controlled by the flow meter signal. Filling when the filling machine on the main cylinder down, filling valve inserted into the barrel mouth, filling valve on the small cylinder launched and open the valve mouth, the material through the flowmeter, filling valve will be injected into the barrel, at the same time, start real-time collection of signals from the flowmeter (counting). After the barrel is full of ferric sulfate weighing and filling machine closes the valve before and after the flowmeter, the small cylinder on the filling head retracts and closes the filling valve, the residual liquid recovery starts to work, and the residual liquid on the head of the filling valve is recovered by the vacuum to the residual liquid recycler, at the same time, the main cylinder on the filling machine lifts up, the positioning locking device opens, and the barrel is moved out by the conveyor, and the filling is finished.
Basic parameters:
Maximum weighing capacity: 30kg
Minimum Sensitivity: 0.01kg
Filling error: ±0.01-0.02kg
Filling speed: 20L about 150-180 barrels/hour
Control mode: 2-speed control
Filling method: Insertion, liquid level up
Gun head line: Teflon gun head, valve + Teflon hose
Structure material: host SUS304 stainless steel, conveying palletizing carbon steel anticorrosion paint.
Weighing platform size: 400 × 800mm (304 stainless steel power raceway)
Empty barrel raceway: 400mm × 2500mm (304 stainless steel power raceway) with another 1200mm slope without power roller
Heavy drum raceway: 400mm×2500mm (304 stainless steel power raceway, 2 sets)
Separate barrel device: for 20L barrels, carbon steel anticorrosive paint structure, 304 stainless steel raceway.
Palletizing equipment: pan-transfer type, suitable for pallets 1200×1200×140mm, including supplying pallets, palletizing, and lower pallet conveying.
Pipe pressure: 0.2-0.6MPa (related to material properties).
Material interface: DN40 flange connector 4, according to the user to provide interface standards
Air Connection: User supplied 12mm air hose connector for quick coupling connection
Power supply: AC220/50Hz (user-supplied to one side of the machine)
Using air source: 0.4-0.8Mpa (provided by the user to the side of the machine)
Use temperature: -10℃-50℃
Base conditions: solid concrete floor of the assistant suspension agent flat, concrete thickness should be more than 10cm.
Optional models: standard, explosion-proof filling