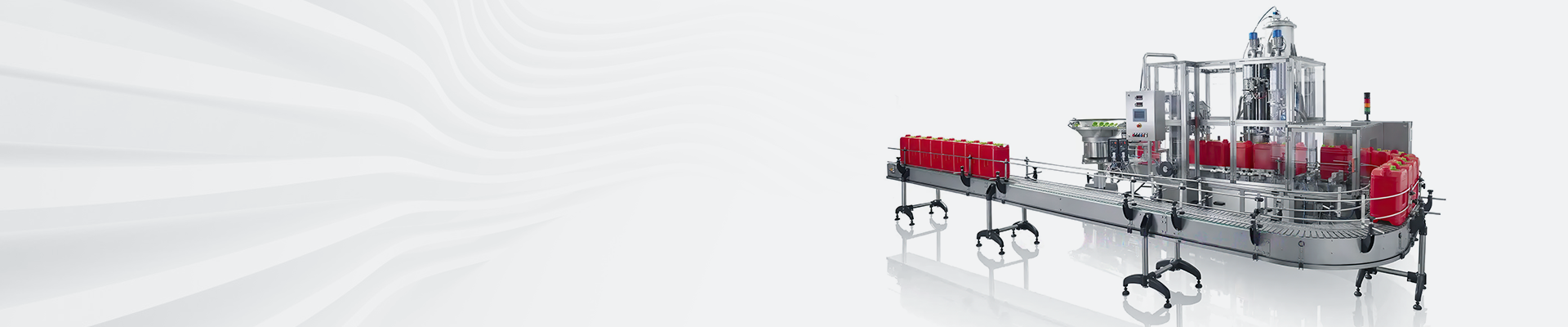
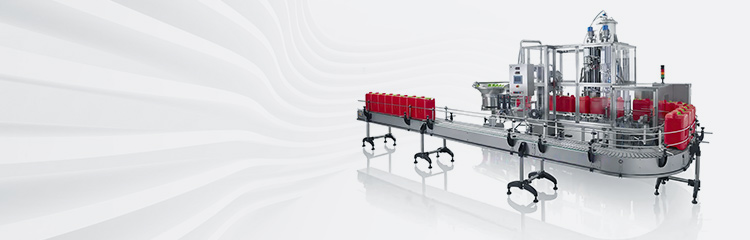

Summary:In order to improve the utilization efficiency of the equipment, the linear volumetric filling machine, screw propeller, capping machine, capping machine, baler, palletizer and other equipment were comprehensively modified to realize the filling of barrels of different specifications and reduce the cost. cost and improve the efficiency of the filling machine.
0Introduction
For lubricants and special industries in the production of liquid dispensing, often use various types of online capacity filling line. China Petroleum Lubricating Oil Company's production plants packaging device used in the lubricant dispensing production line, for example, mostly vertical, multi-head, online, small capacity fully automatic filling line. The introduction of equipment for each plant's own brand, different barrel types, different sizes, and later in the company's brand integration, car oil, commercial vehicle oil, industrial. Later, in the company's brand integration, car oil, commercial vehicle oil, industrial machinery oil, motorcycle oil, gas station exclusive sales and export products and Kunlun Star car auxiliary products, there are different types of packaging products, and various types of products are divided into several series, each series of products of different barrel types, each plant due to the characteristics of the base oil and the need for the product factory, often responsible for several series of small packages of several specifications of the product sub-production tasks, the process will need to original production line to carry out the transformation. The original production line needs to be remodeled in this process.
1 lubricating oil plant 1 4L filling production line status lubricating oil plant 1 existing packaging production line 5, of which 2 4L packaging line, a production line since 1997, originally designed to meet only a barrel-type oil filling, but at present the lubricating oil plant is responsible for the "Kunlun - Tiange" "Kunlun - Tianli Tianli" "Kunlun - Tianhong" series of oil production of small packages, and for OEM customers products, in order to reduce production costs, better serve the market, improve the utilization rate of existing equipment, after innovation and transformation, so that the original single specification vertical, multi-head, online, small capacity, fully automatic 4L filling The production line can be adapted to the production needs of multiple barrel types and specifications. Through several years of production and operation, from the original only a single 4L specifications in a barrel type of filling, after the transformation of the new barrel type of 4, the specifications of the barrel type of 1L, 2.5L, 3L, 3.5L, 4L, 5 different specifications, has greatly improved the utilization of the original equipment. It should be noted that, in the introduction of the new production line, even taking into account the barrel type switching, can reduce the cost of future transformation, improve the efficiency of production switching, but it does not mean that there is no need for renovation, especially now with the sale of production and commissioned processing production, the barrel type and the amount of specifications in the continuous updating and changes in the future renovation is unavoidable. Here, the lubricating oil plant on the introduction of equipment for the localization of the transformation experience is introduced.
2 Filling production line remodeling experience
2.1 Increase the bottle feeding machine, the empty bottle transmission method to be improved
Lubricating oil plant originally in the front of the filling machine for direct bottle feeding, operation found that it is not easy to site management, due to the production plant and empty bottle storage warehouse is not on the same floor, manpower transport distance is too far, the elevator is used too often. The bottle feeding machine and vertical bottle clamping conveyor are put into use, so that the empty bottles are transported from the storage area to the feeding area in the upper floor, and the operation control device is controlled by the filling operator in the lower floor. Empty bottles are transferred from the chain plate of the bottle feeder to the vertical bottle clamping conveyor, and then connected to the empty bottle conveyor downstairs, which reduces the pressure of material transportation management on the production line site and improves the working environment of the bottle feeder. The original bottle casting device near the air compressor, the noise is larger, in the upstairs drum transfer, on the one hand, reduces the noise, on the other hand, also makes the bottle casting operating environment better, the room temperature in winter is more than 15 ℃, the room temperature in summer basically stays below 30 ℃, the light, lighting, ventilation have been improved over the previous.
2.2 Modification of metering filling machine
In 1997 the filling machine was only adapted to the filling of one barrel type and the adjustment of internal loading specifications when the equipment was introduced. After the integration of lubricating oil company, according to the market and OEM users' demand, the barrel shape changes a lot, the size of the length, width and height are big differences. Lubricating oil plant again for different barrel type increase filling line does not have the conditions, both the waste of resources, but also increase the cost of enterprises. After discussion and argumentation, hands-on remodeling of filling machines, screw propellers, capping machines, capping machines, packing machines, etc. will be the best choice. Immediately the lubricant plant set up a transformation team, first of all, the quantitative filling machine into the barrel positioning cardboard reform, according to the barrel body width and diameter of the barrel spout dimensions to produce positioning fixtures.
Make clamps fixed in the positioning frame, barrels into the explosion-proof filling machine, the detector detects the barrel information to give a signal to the plc, so that the positioning frame is closed to position the barrels in the canning head under the right, to achieve the canning production. According to the barrel type, the width and thickness of the barrel to produce the screw propeller, feed vortex rod, the material used MC nylon 6 to produce, wear-resistant and very small deformation. As shown in Figure 4, the dimensions in the figure are calculated in mm.
Capping machine transformation is one of the key aspects of the equipment transformation to ensure that the production rate, but also the transformation of the workload is relatively large piece. First of all, according to the different specifications of the barrel type of the feeding vortex, star feed wheel, center star wheel, side guide plate, center guide plate, send out star wheel processing and transformation. When remodeling, we should pay attention to the measurement and calculation of the size, and pay attention to the choice of material, must be wear-resistant, corrosion-resistant, and second is to pay attention to the specifications of the barrel type for switching the adjustment of the position of each component. In addition to the above mentioned parts, attention must be paid to adjusting the position of the guide bar for squeezing.
Principle and production of capping machine: double-disk gap capping mechanism is mainly composed of top disk, chassis and driving device, etc. When facing the top disk, it enters into the downward slide through screening, and when the mouth of the cap is backward to the top disk, it returns to the hopper under the rotation of chassis and auxiliary blowing, and enters into screening again.
Capping machine part of the transformation: first of all, according to the length, width and height of the barrel to determine the height of the rotary fixture and the size of the recessed part, and then there is the transformation and adjustment of the cover and rotary chute. On the basis of the original rotary chute, it is widened and heightened, so as to adapt to the smooth rotation of different shapes and specifications of pail lids. At the same time, the height of the bogie should be adjusted according to the height of the barrel during the switching process of each specification barrel cover.
2.3 Transformation of oil storage tanks
Oil in the sub-filling production, oil tank oil by the pump transported to the liquid filling machine before the storage tank, the actual production, some varieties of oil is often due to the delivery process contains gas, affecting the volumetric filling products filled with oil net content accuracy and production efficiency, for this reason, in the original storage tank above the installation of a 2.5m 's buffer static tank, the basic improvement of the oil sub-filling process The oil contains gas in the oil due to a variety of circumstances.
2.4 Replacement of the entire packaging machine
Before the transformation of the wrapping packaging machine, due to the northern climate characteristics, the temperature difference between the four seasons, air humidity is small, affecting the quality of the box molding, and even many times in the production of the box molding is normal, stored in the warehouse because of the air humidity is small, the room temperature is low and other reasons to open the box, affecting the quality of the appearance of the product. Therefore, in the transformation of the selection of suitable for the northern production of the drop box type automatic folding packaging machine for the replacement of the entire machine. The type of packaging machine by the divider, unpacking machine, drop box machine, belt conveyor and other parts of the composition, to change the melt glue type for the tape paste type sealing. That is, after the carton body is nailed, the upper and lower box cover is only pressed out of the crease, so as to facilitate the logistics and transportation of packages, in the production process, after the carton enters the unboxing machine, the vacuum sucker controlled by the walking motor pulls open the carton, folding the bottom, pushing the box in the process of folding the bottom, under the driving force of sealing the bottom of the box motor, the bottom of the box will be glued with adhesive tape to send out the bottom of the box, through the chain transfer to the box falling machine, wait for the falling barrels to pack the boxes, in the process of the belt conveyor by the sealing of the top box, the top of the box will be sealed with tape. At the top, the top cover of the box is folded and glued, and then enter into the next link after spraying code.
2.5 Additional electronic scales for double-checking
Volumetric dispenser with the change of oil temperature, the net content of the loaded oil will be different, in addition, in order to prevent the packaging process at the drop box lack of barrels, add a double-check electronic scale. The checking weight is set according to different specifications before production. Review of electronic scales online detection, the set range of deviations allowed to release, when the deviation exceeds the permissible range, the box will be launched, high detection accuracy, and the entire line of electrical interlocking, the occasional lack of a single box will be automatically pushed into the unqualified platform accompanied by an audible alarm to wait for the processing, such as in the case of more than 2 boxes of lack of quantities of the export product pile up alarms and the entire filling production line will automatically shut down until manually disarmed.
2.6 Add alarm interlocking device
Electrical interlocking is carried out for faults such as insufficient amount of contents, lack of film, lack of cap, malfunction of coding machine or no coding. The original production line due to product quality standards and requirements continue to improve, add the barrel coding and box coding, online rechecking electronic scales and other equipment, additional equipment must be added with the original equipment for electrical interlocking, interlocking. On the one hand, the operator is the reduction of labor intensity, but mainly to improve the quality control of all aspects of the product, to avoid and control substandard products factory, reduce the number of substandard products rework processing, so that the loss of packaging and oil in the process of subcontracting production down to ensure that the product subcontracting production of the stability of the pass rate.
3 equipment transformation follow the principles
3.1 The feasibility of equipment transformation
Problems with the equipment, the basis for transformation, the choice of program to have feasibility. Here the "feasibility" includes three points: First, the selected technology or equipment should be the industry's current relatively advanced, stable performance, easy to maintain. Second, after the transformation of kinetic energy consumption should be within the affordable range, from the energy-saving aspects to consider. Third, it means that the transformation difficulty should be low, the construction period should be short, the cost should be less, the risk should be small, and the effect should be obvious.
3.2 Equipment transformation must follow the HSE management principles
Preparation before transformation, transformation construction and transformation after acceptance should comply with the HSE management system of quality, health, safety, environmental objectives and principles, energy saving and consumption reduction, protection of the environment, to ensure safe production, improve labor conditions, improve labor productivity.
4 equipment after the transformation of the advantages and disadvantages of analysis
After the completion of the transformation, there are still many unsatisfactory but must face. Is to open the box machine line slot position setting, according to the design specifications, the production site pipe, line layout must comply with the provisions of China's industrial design standards, does not hinder the safety of personnel in the vicinity of the machine out of the people to avoid tripping, there is enough space to ensure that the operation and maintenance of personnel operating in the safety, although in line with the standard, but the location of the setting is by no means optimal, and the actual operation of the feeling that if embedded in a hidden type or overhead type In actual operation, I feel that if I use the embedded hidden type or overhead type, it will make the remodeling better. This is still a problem that needs to be paid attention to in the future remodeling and introduction of equipment.
5 Conclusion
From the current operation of the equipment to prove that the lubricating oil plant on the 4L weighing and filling machine production line transformation is more successful. The new oil buffer static tank to solve the production of oil with wind problem, through the supporting processing of the clamps, can adapt to a variety of shapes and sizes and materials of the barrels of the sub-filling production; replacement of the packaging machine compared with the replacement of the former, the same efficiency, sealing effect is better to meet the production needs; new electrical interlocking can improve the efficiency of product production, reduce the labor intensity of the operator. Not only has it accumulated rich experience for the further transformation of 4L filling production line in the future, but also has accumulated sufficient information and experience for the transformation of similar equipment.