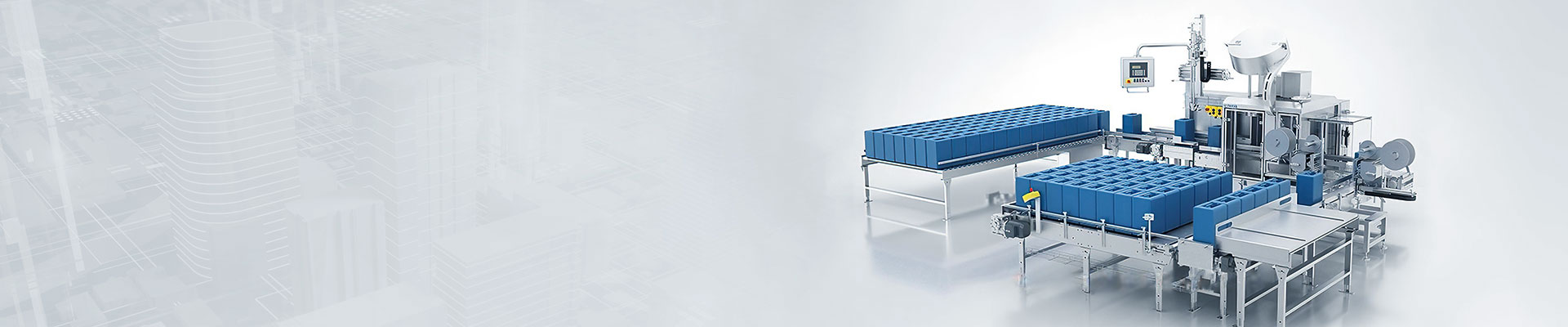
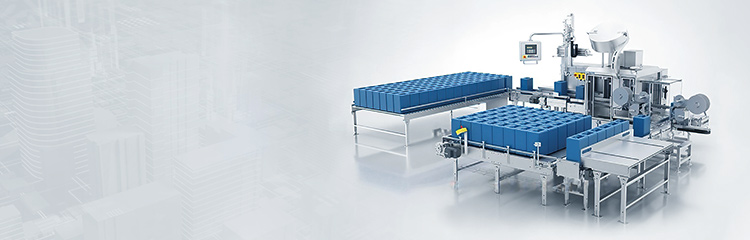
Pharmaceutical liquid filling machine PLC as the control core, drive relay driven frequency converter control motor and centrifugal pump conveying materials, through the weighing module to calculate the pipeline tube flow pulse signal, to obtain the actual weight of the liquid discharged by the weighing system, according to the difference between the actual filling volume and the set value to control the motor operation, so as to realize the precise control of the filling volume according to the actual needs.

Weighing and Filling machine adopts German Siemens S7-300PLC programmable controller, distributed I/O ET200M and industrial control machine (loaded with WinAC and PROFIBUS-DP adapter CP5611) to form a new type of filling equipment, and PROFIBUS-DP is used as the network platform of equipment control layer; WinCC, MPI network as the monitoring layer of man-machine interface and filling maintenance (network programming, man-machine interface back-up station) platform; Ethernet as data management, production and equipment management layer network platform. Among them, S7-300PLC programmable controller as the lower to realize all the signal acquisition, operation, regulation, respectively: temperature control, traction control, pressure control and auxiliary control of the local unit, the industrial computer is mainly installed WinAC adapter and unit status monitoring, process data access, unit automatic filling control, and workshop-level process control server and production planning server connected.
Automatic filling machine to batch for the production cycle for production, strict implementation in accordance with the provisions of the work order (recipe) for the implementation of automatic filling machine control procedures, in order to achieve accurate production, to avoid production losses caused by human error in the production process, through the feeding process, filling process of the instruction information checking and confirmation of the important steps of the electronic signature, the material and the container code identification of the constraints, to ensure that the weighing of the filling machine to implement the Correctness. Generate process production batch reports, material balance and other quality related reports, process data reports, material usage reports, work order reports, etc., through which the analysis of the filling process can be realized.
Basic parameters:
Maximum weighing capacity: 30kg
Minimum Sensitivity: 0.01kg
Filling error: ±0.1-0.2kg
Filling speed: 20L about 150-180 barrels/hour
Control mode: 2-speed control
Filling method: Insertion, liquid level up
Gun head line: Teflon gun head, valve + Teflon hose
Structure material: host SUS304 stainless steel, conveying palletizing carbon steel anticorrosion paint.
Weighing platform size: 400 × 800mm (304 stainless steel power raceway)
Empty barrel raceway: 400mm × 2500mm (304 stainless steel power raceway) with another 1200mm slope without power roller
Heavy drum raceway: 400mm×2500mm (304 stainless steel power raceway, 2 sets)
Separate barrel device: for 20L barrels, carbon steel anticorrosive paint structure, 304 stainless steel raceway.
Palletizing equipment: pan-transfer type, suitable for pallets 1200×1200×140mm, including supplying pallets, palletizing, and lower pallet conveying.
Pipe pressure: 0.2-0.6MPa (related to material properties).
Material interface: DN40 flange connector 4, according to the user to provide interface standards
Air Connection: User supplied 12mm air hose connector for quick coupling connection
Power supply: AC220/50Hz (user-supplied to one side of the machine)
Using air source: 0.4-0.8Mpa (provided by the user to the side of the machine)
Use temperature: -10℃-50℃
Base condition: Horizontal solid concrete floor, concrete thickness should be more than 10cm.
Optional models: standard, explosion-proof filling scale