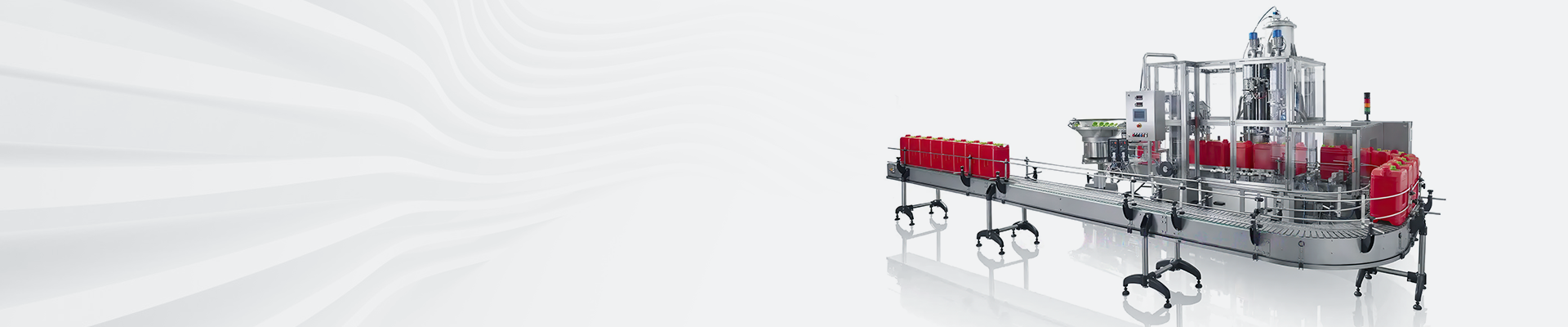
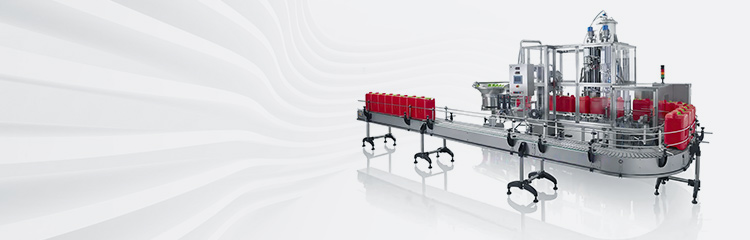

Summary:The practice of mixing production has proved that the deviation of the mixing ingredients is an important factor affecting the normal operation of the mixing process and the quality of the mixing powder.Therefore, precise dosing is very important.In view of actual needs, the intelligent weighing system and the PID control algorithm are applied to the control of the mixing and batching system, and the control process of the mixing and batching system using the intelligent weighing system and the PID control algorithm to achieve accurate batching is introduced in detail.Practice has proved that the application of this technology has achieved good control effects and is suitable for practical application on site.
According to the requirements of mixing production process and mixing powder quality requirements, accurate dosing is very important. Mixing production practice has proved that the deviation of batching is an important factor that affects the normal mixing process and the quality of mixing powder. Such as: solid fuel dosing fluctuation of 0.2%, will make the strength and reducibility of the mixing powder affected, mixing powder iron content and alkalinity fluctuations will affect the blast furnace temperature and slagging system, in serious cases, will trigger the blast furnace hanging material, crashing material phenomenon. This paper focuses on the mixing and dosing system using intelligent weighing system with PID control algorithm to achieve accurate dosing control process.
1 system control overview
Stirring batching control is based on the material flow detection of intelligent weighing control system. The detected material flow is transmitted to PLC, and after PID regulation operation in PLC, the motor control frequency of each broadband and screw feeder is given according to the proportioning value and output to frequency converter, which controls the motor speed of broadband and screw feeder to control the change of material flow.
Because of the unevenness of material conveying and the change of belt speed with time, the cumulative amount of material conveyed in the time interval; the time that the material passes through the weighing; the weight of the material on the unit length of the belt; the running speed of the material on the belt. As can be seen from the formula, as long as the product is guaranteed to remain constant, you can ensure that the material flow is constant, that is, with the change in the weight of the material on the belt to control the belt speed to make the appropriate adjustments, you can ensure that the material flow is constant. In this system, the speed of the belt scale is constant and unadjustable, so to control the flow of constant only to adjust the weight of the material on the belt, and the weight of the change can only be changed by changing the frequency converter, in order to change the speed of the wide belt and spiral material.
2 Intelligent weighing and batching system
2.1 Intelligent weighing and batching system topology structure
The weighing and batching system described in this paper is composed of 13 broadbands and 2 screw feeders. To ensure the stability of the mixing and batching ingredients, the flow control of the 13 broadbands and 2 spirals is the key. For flow collection the batcher uses a Ramsey Model XR-2105P flow controller. When the conveyor conveys the material, measure the value of the load per unit length on the belt scale and multiply it with the running speed of the belt at the same moment, and the result is the instantaneous flow of the material.
2.2 Frequency converter MB + network control
Each time before the inverter is powered up or after a fault, the initialization is carried out first, and the control program of this part is completed by PLC.
13 broadband and 2 spiral adjustment feeding with inverter by the communication card access MB + network, in each inverter expansion card to set the hardware node address, set the communication machine protocol, mode and accept and send the number of bytes; at the same time, define the PLC within the communication library protocol, mode and accept and send the number of bytes. PLC within the use of PEERCOP to the inverter " WRITE" command, including start-stop operation, motor forward and reverse control, process regulation control, fault control, etc.; GLOBAL to the frequency converter "READ" state, including current, voltage, speed and other information, to understand the operating status of the frequency converter and the motor.
3 feeding PID regulation control feeding
PID regulation mainly through the frequency converter to adjust the speed of the broadband or spiral motor to change the amount of material. The traditional PID control method is unable to achieve the stability and accuracy requirements. Therefore, the PID control of the band is adopted to avoid too frequent control action and eliminate the overshooting of the oscillating system caused by frequent action and on-site vibration, resulting in an unstable amount of material to be discharged. The principle of control is that the instantaneous flow of material feedback value and the computer to compare the given value, and then through the PLC with the PI regulation, the frequency converter to control the speed of the broadband or spiral to stabilize the material requirements.
3.1 Principle of band PID control algorithm
Position tracking deviation, instantaneous flow feedback value is an adjustable parameter, its specific data can be based on the actual control object process requirements or practical experience to determine. If the value is too small, it will make the control action is too frequent, can not achieve the purpose of stabilizing the controlled object; if it is too large, the system will produce a large hysteresis, the system's rapidity decreases and can not meet the process requirements. The control system of the belt is actually a nonlinear system, when l digital regulator output is zero; digital output regulator has PID output.
Note: In practice, the PID controller with is realized by the PLC built-in soft module.
3.2 Control characteristics
In this feeding system control, under the action of the same interference signal, the traditional PID controller and the PID controller with debugging.
From the debugging results, with PID regulation than the traditional PID regulation has a good response speed, can be caused by fluctuations in the field to implement rapid adjustment, but its shortcomings still exist in the static difference, but this static difference is completely in the process within the scope of the requirements; and the traditional PID regulation is not only 20% or so overshooting, and the system responds relatively slowly so that the fluctuations encountered in this way will result in the dosage is not uniform and even cause the quality of the mixing powder. Uniformity and even cause the quality of powder mixing.