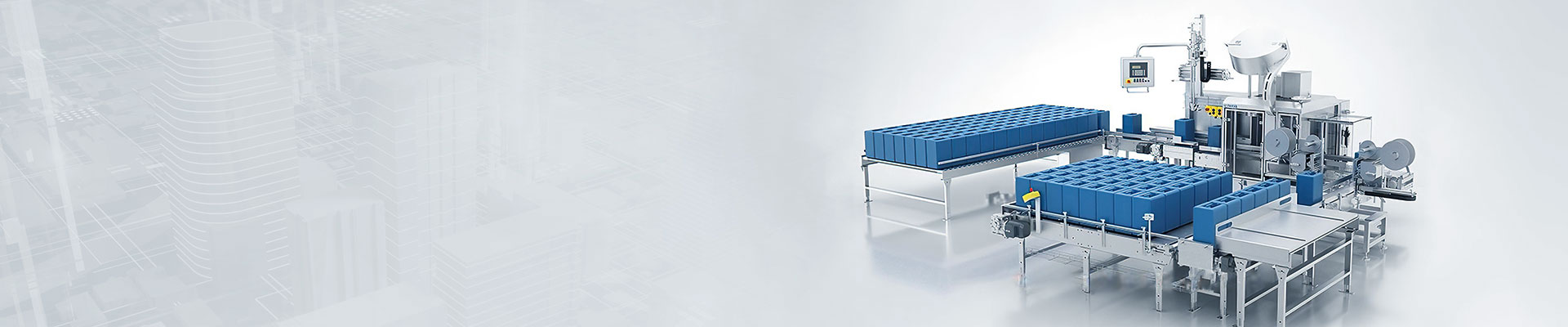
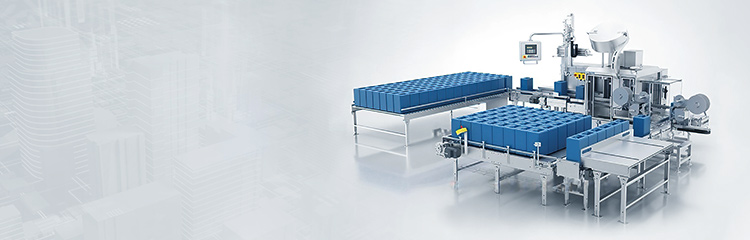
Weighing the reaction pot by several raw material conveyor screw to the raw material in the order of the set to the metering scale, each raw material according to the automatic control system set the weight of the conveyor in turn, after the weight of the raw material is measured, and then by the metering scale of the discharge spiral to all the raw materials to the downstream equipment (cache bin, or direct pipeline connection), while starting the vacuum conveyor or valve. The raw material is sent to the waiting bin located above the main engine, where the weight of the raw material is completed.

Reactor weighing is controlled by touch screen, and the metering equipment is fed by several hopper scales for continuous conveying, which consists of hopper metering scales, screw conveyor, discharging screw, computerized control system, and small material (micro) placing device. Weighing and metering is done by several raw material conveying screws to convey the raw materials to the weighing scale in a set order, each raw material is conveyed in sequence according to the weight set in the automatic control system, and after the raw material weighting and metering is done, the discharge screw of the weighing scale conveys all the raw materials to the downstream equipment (cache hopper scales, or direct pipeline connection), and at the same time, it starts the vacuum conveyor or valves, and sends the raw materials to the mixing bin which is located on the top of the main machine. At this point, the weighing of the raw materials is completed.
Weighing and batching machine combines the advantages of dynamic weighing and static weighing, the hopper scale and feeding mechanism as the whole scale body, through the instrument or the host computer constantly sampling the weight signal of the scale body, calculate the ratio of weight change per unit of time as the instantaneous flow rate, and then through the processing of a variety of software and hardware filtering technology, to arrive at the "actual flow rate" can be used as the object of control. The "actual flow" can be used as the control object. The equipment part mainly consists of hopper scale, feeding Feeder, discharging feeder and suspension device. The control part mainly consists of Weighing modules, signal amplifiers, input and output interfaces, host computer (host computer) and so on.
The process of dosage control system is divided into two stages: feeding and unloading. After the dosage starts, the feeding feeder is started firstly, and the controller detects and samples the weight of materials in the hopper weigher, and stops feeding when the weight of materials in the hopper weigher reaches the upper limit value set by the dosage. At the same time, the controller detects and samples the material weight of the hopper scale, and stops feeding when the material weight of the hopper scale (feeding quantity) reaches the upper limit value set by the dosage. In the unloading stage, the controller starts the unloading feeder to unload the materials in the hopper scale to the next level of material transfer equipment to send away. When unloading, the controller detects and samples the weight of the material in the hopper scale, and when the weight of the material in the hopper scale reaches the lower limit value set by the dosage, it re-feeds the material to the hopper scale. However, after the second feeding phase begins, the discharge feeder continues to unload without stopping.
The automatic feeding system continuously weighs the whole feeding system, including the hopper scale and the feeding mechanism, which is equivalent to a static scale; at the same time, the unloading flow of the feeding mechanism is controlled by frequency conversion.
The reduction of material weight per unit of time in the hopper scale corresponds to the feeding flow of the dosage. The dosage controller compares the dosage flow with the preset flow and automatically corrects it by adjusting the speed of the feeder, thus maintaining an accurate dosage flow.
When the weight of the material in the hopper scale falls below the preset value, the control module will lock the feeder speed and keep the downcomer mechanism feeding the material volumetrically while opening the fill valve for fast dosing. When the weight of material in the hopper scale reaches the high preset value, the charging valve will be closed automatically. At the same time, the Dosage system controller automatically switches the feeding mechanism to weighing mode.
The hopper scale will start from the feeding pump of raw materials until the qualified materials are sent to the reactor. It will include all the control and interlocking of the feeding and discharging valves, starting and stopping of the feeding pumps, fast and slow feeding control, status detection, and all the data processing functions. The system consists of weighing unit, data processing unit and logic control unit. They work independently of each other and are closely connected in a question-and-answer way. Flexibility and maneuverability, while improving the degree of automation of the system, but also improve the reliability of the system. To guarantee the user can run without trouble for a long time. The main low-voltage electrical components are TE and OMRON products.