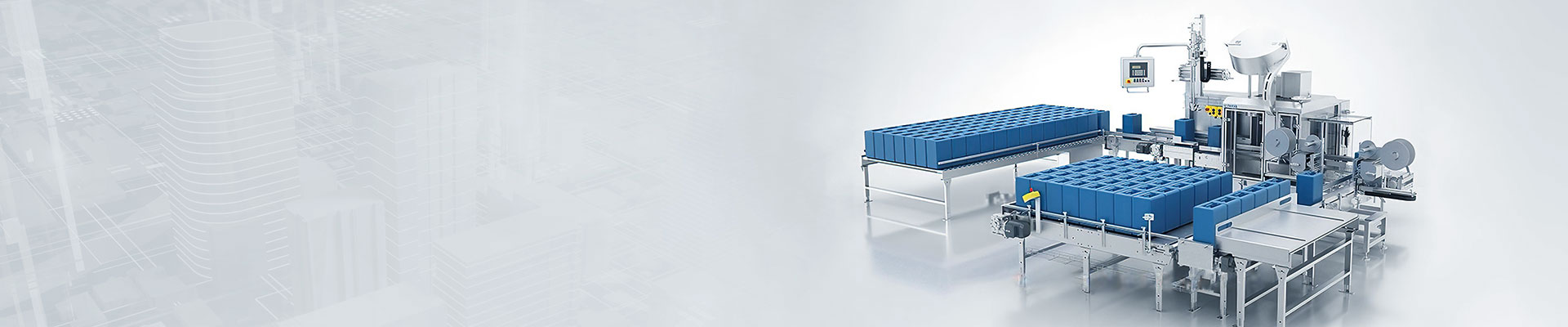
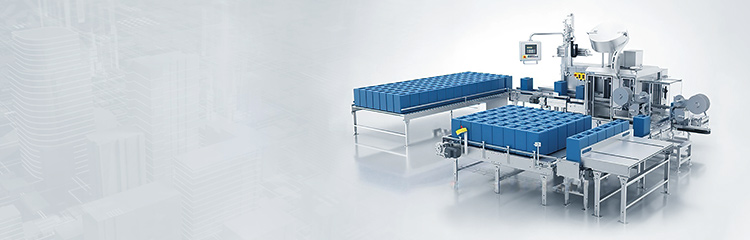
After the batching system enters the feeder from the bin, the weighing signal is processed by the controller to control the vibration feeder to drop the material at a certain rate. When the set value is reached, the feeding stops. Confirm that when the charging position is specified, and confirm that there is no material in the silo, the charging is opened according to the operator's instruction, and the material enters the charging silo; When all the measured materials enter the feeding bin, and confirm that the door of the measuring feed bin is closed, add the next batch of materials according to the operator's instruction, and start the walking motor of the feeding bin according to the operator's instruction or automatic program when starting, to complete the batching process.

Feeding system is two or more materials according to a certain weight ratio automatically added to the mixing dosage tank, after mixing to meet the predetermined requirements of the process of automatic discharge. Batching reactor control weighing module signal input, each reactor weighing are 3 or 4 Weighing modules, each group of weighing modules in parallel or in series by 4 or 6 with the signal line into the signal line junction box, and then access to the TR200H indicator signal is 2MV/V, sensitivity signal transmission, shall be converted to analog signals through the identification of the weighing terminal and sent to the analog signal acquisition module of the PLC; The whole Batching system does not need weighing instrument and main console, only weighing module junction box, wiring cabinet, PLC, analog input module, communication module, touch screen, the main hardware consists of two computers, high-performance microcomputer controllers, human-computer interface, high-speed and high-precision weighing unit and international famous low-voltage electric appliances, combined with self-developed professional software to realize the automation of the production of chemical liquid control.
The whole batching machine by the mixing tank, storage tank, weighing module, liquid level meter, Mitsubishi FX2N128 points PLC, Mitsubishi special module FX4AD analog input acquisition module and FX232IFCOM communication module, F900 series touch screen and a number of control valves and other control devices such as pneumatic valves and so on, divided into two major parts of the mechanical and control.
By into the reaction tank, measuring tank, mixer three parts, into the reaction tank under the drive of the motor to the measuring tank to send out the material, liquid tank support in the weighing weighing module, from the weighing module and weighing instrumentation generated on behalf of the weight of the electrical signal by the signal amplification module and then by the PLC and computer acquisition, when the weight reaches a predetermined level, the PLC drive motor to open the measuring tank pneumatic valve door, the material into the mixer, and at the same time! At the same time, the material enters into the mixer and at the same time, the mixing motor is started, and after mixing for a specified time, the discharge port is opened to release the material, and the batching process is completed once.
The signal 0-30mV of the weighing module of the kettle is connected to the amplifier module of the weighing module, and then it will be converted to the standard signal of 0-30mV (can be used in 1-3mV/V resistive strain weighing module), and then converted to the DC voltage output of 0-5V, 1-5V, 0-10V or current output of 0-10mA, 0-20mA, 4-20mA, and then transferred to the serial communication method for data processing. After serial communication to the PLC AD acquisition module, PLC will receive the data into the touch screen or the host computer program interface display for operator monitoring; when the need for mixing and dosage, PLC to start the charging valve pneumatic valve, the required materials according to a certain ratio of sequential addition to the mixing tank, while the PLC monitor the level meter to send pulse signals to determine the material position in the kettle to control At the same time, PLC monitors the pulse signal from the liquid level meter to determine the position of the material in the dosing kettle, so as to control the opening and closing of the pneumatic valve of the dosing valve; after the dosing is completed, according to the preset mixing delay time, PLC starts the mixing motor to ensure that the material is fully stirred in the mixing kettle to complete the mixing operation; then it enters into the stage of discharging and pressing the material, and the PLC controls the action of pneumatic valve of the discharging valve, which outputs the material from the mixing kettle to be pressed into the storage kettle, and completes the automatic dosage control process for one cycle.