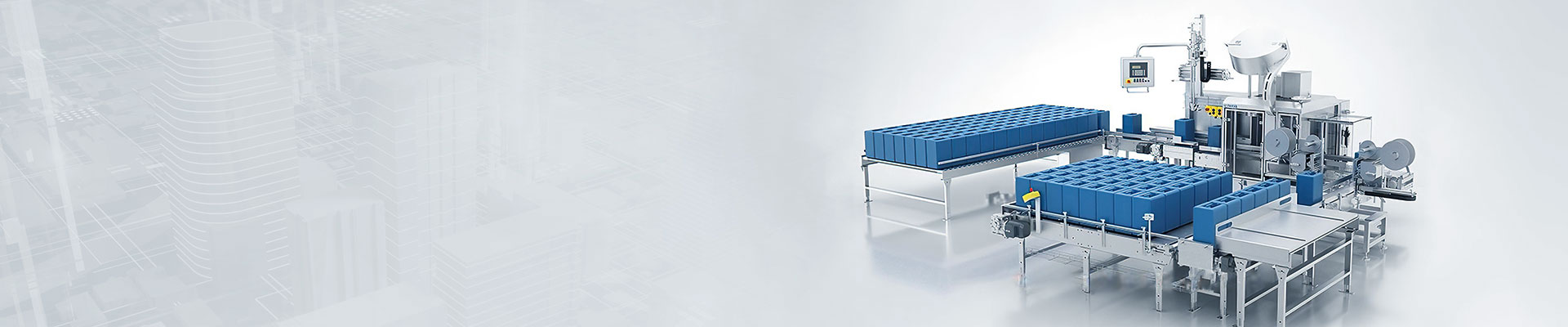
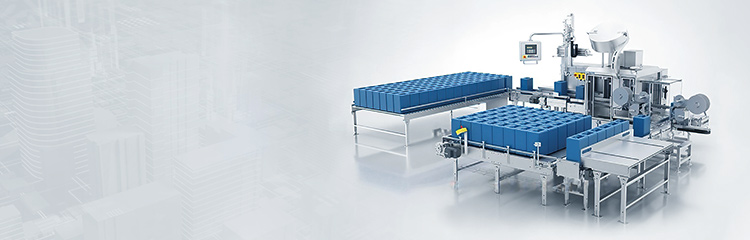
The mixing and feeding equipment adopts the regulating valve or changes the pressure of the issuing tank for dosage, and PID adjusts the weight value to the pressure of the dosage tank or the opening of the regulating valve. The standard proportional function and the proportional calculation of the weighing system are used to ensure the stability of the weighing performance. The given value is multiplied by a multiplier to calculate the target value of the dosage weight, which is given remotely as a control quantity, and the reciprocal is taken to calculate the weight of the discharged material by a multiplier, thus realizing interactive dosage.

Feeding system is a set of complex construction equipment, the production environment is extremely harsh, most of the kettle control Dosage system is mostly used in the upper monitoring + PLC, or upper monitoring + PLC + weighing instrument mode. In order to ensure the reliability of the whole control dosage system, Advantech industrial controller is chosen as the upper computer, with analog data acquisition boards to collect various production weighing sensing signals, and digital acquisition boards as the input signal detecting and controlling outputs through the kettle weighing module, so as to realize the whole process of controlling the dosage, unloading, mixing, discharging, and recording. The analog signal acquisition adopts Advantech PCI bus isolated high-speed analog input card, and the input and output of status signal adopts Advantech PCI bus isolated digital I/0 card. The dosage monitoring and management software automatically controls the dosage by high-speed acquisition of on-site signals from the computer, and automatically and precisely configures all kinds of materials according to the pre-set program with dynamic monitoring, real-time alarm and error correction functions to ensure the product quality is It has dynamic monitoring, real-time alarm and error correction functions to ensure the stability of product quality. Meanwhile, the Batching system also provides background data management functions, including user management, formula management, report management, weighing calibration and other functions.
The mixing and feeding system adopts the regulating valve or changes the pressure of the issuing tank for dosage, and PID adjusts the pressure of the dosage tank or the opening of the regulating valve by the weight value. The standard proportional function and the proportional calculation of the Weighing system are used to ensure the stability of the weighing performance. The given value is multiplied by a multiplier to calculate the target value of the dosage weight, which is given remotely as a control quantity, and the inverse is taken and then the weight of the discharged material is calculated by a multiplier, thus realizing interactive dosage. At the same time the feeding system has the following functions:
Control measures for accuracy and efficiency
In the software design, comprehensive consideration is given to all aspects such as reliability, weighing calibration, weighing accuracy, data processing, etc. in order to improve productivity and control accuracy.
digital filtration
In the weighing analog signal input due to mechanical vibration, electrical interference and other impacts, the signal distortion is more serious, the software first of all on the sampling data signal filtering, elimination of suppression of interference signals, the use of tracking type adjustment of the fall, in the process of production can be automatically corrected, which can ensure that the powder error within ± 2%, and other powder error within ± 1%. By pre-processing the data, the weighing terminal in continuous production can be weighed in advance to improve efficiency, weighing the first high-speed feeding, to reach the set value of about 90% after the beginning of the jitter replenishment, to achieve fine weighing.
Weighing Calibration
Weighing calibration coarse adjustment is completed by the hardware, weighing calibration fine-tuning is completed by the software to avoid weighing calibration fine-tuning zero migration and gain amplitude in the hardware circuit of the mutual implication of the problem, explosion-proof Electronic scales to improve the calibration efficiency and calibration accuracy.
auto-zeroing
Since the weighing substance may stick to the weighing hopper and affect the weighing accuracy, the software automatically adjusts the zero point to eliminate the effect of the weighing sticking substance on the repeat weighing accuracy.
correction for dropout voltage
The dosing process is a dynamic weighing process where the weighed material falls onto the weighing hopper in the form of a free fall. When the weighing value is reached, the randomness of the difference between the clans due to the discrete nature of the mechanical action delay affects the accuracy of the dynamic weighing.