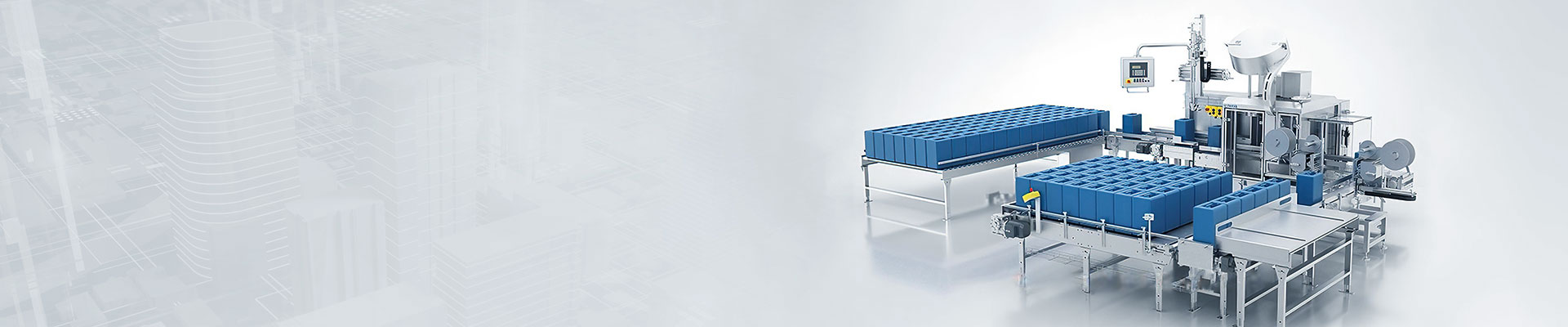
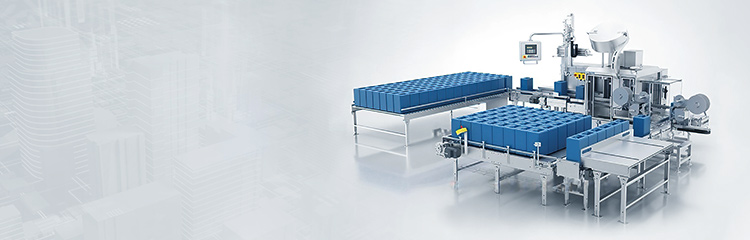
Spiral feeding scale adopts the new technology of negative pressure conveying + batching tank, automatic measurement, automatic batching, automatic conveying, automatic mixing and other functions into one, centralized control effectively solves a variety of materials how to ratio, conveying the problem of completely eliminate the material in the process of easy to produce dust on the environment as well as the environment on the double pollution of the material. Conveying occurs in the last process before mixing, which not only reduces the dosing error, but also effectively protects the product quality.

Screw feeding scale is a kind of measuring equipment that utilizes the rotary movement of screw for accurate weighing. It consists of feeding tube, screw, load cell, control system and so on. When working, the material enters into the Feeder through the feeding pipe, and is driven forward by the spiral, and at the same time is weighed by the load cell. When the weight of the material reaches a predetermined value, the control system will automatically stop the rotation of the screw to prevent the material from continuing to feed. The weighing process is realized by the rotation of the screw. When the material enters the feeder, the auger starts to rotate and the material moves forward. At the same time, the weight of the material is constantly monitored by the load cell.
When the weight of the material is the same as the preset value, the control system automatically stops the rotation of the auger. Since the rotational speed of the auger rotation is adjustable, different accuracy levels of weighing can be realized by changing its rotational speed, thus meeting different production requirements. It consists of a basic automation system and a secondary process computer system. The basic automation system includes automatic weighing and batching equipment and HMI monitoring system, which accomplishes the basic control functions such as on-site data acquisition, process loop control, parameter setting, equipment sequence control, equipment operation monitoring and alarm, etc. The secondary computer weighing and batching equipment accomplishes the process control functions such as design planning, design model calculation, batching model calculation, batching liquid composition logistics tracking, etc. The two levels of automatic weighing and batching equipment together accomplish the design planning, design model calculation, batching model calculation, batching liquid composition logistics tracking and other process control functions. The two levels of automatic weighing and dosage equipment together to complete the automatic dosage control of the reactor to achieve accurate dosage.
Weighing and batching equipment mainly realizes automatic production and whole process control, providing a complete set of automatic production line for the requirements of raw material storage, automatic weighing, batching, delivery, mixing, coarse crushing, fine crushing, constant temperature preservation, pressing and molding, grinding, testing, finished product storage and environmental protection. The system adopts three-dimensional or plane structure design. Among them, the intelligent automatic weighing and batching equipment plays an important role in upgrading the management level, improving product quality and maintaining product stability. After years of continuous technological innovation and improvement, the weighing and batching equipment is well received by customers.
Process control flow:
1, the site uses a special touch screen as a man-machine operation interface, the system operation is direct, reliable, simple and clear, the operator can be based on the requirements of the product process at any time on-line modification of the dosage parameters and dynamic monitoring of the entire work process, real-time data display, alarm display.
2、Weighing system can store several production formulas according to the requirements, for the operator to call and modify at any time.
3, weighing system adopts PLC as the main control element, directly through the PLC 16-bit high-precision A/D converter module to collect on-site load cell data, according to the preparation of the program to directly control the output, reducing other intermediate control links, system stability, reliability, low failure rate, to adapt to a variety of harsh working environment. With PLC direct control, the system is highly expandable, the program is easy to understand, and the factory technician can increase the function at any time according to the need.
4, the field PLC and computer through RS485 communication directly form a network, realize the system remote monitoring, for enterprises to realize automation management provides more advanced conditions.
5、Weighing control system faults can be directly displayed through the touch screen, maintenance personnel can quickly troubleshooting according to the fault display, easy maintenance.
6、High reliability and direct control make the dosage speed fast, dosage precision high, greatly improve production output and product quality.
7, high degree of automation, can complete a variety of configurations at the same time, reduce labor input and improve the operator's labor intensity. At the same time, it realizes the complete automatic control of the whole feeding and batching control.