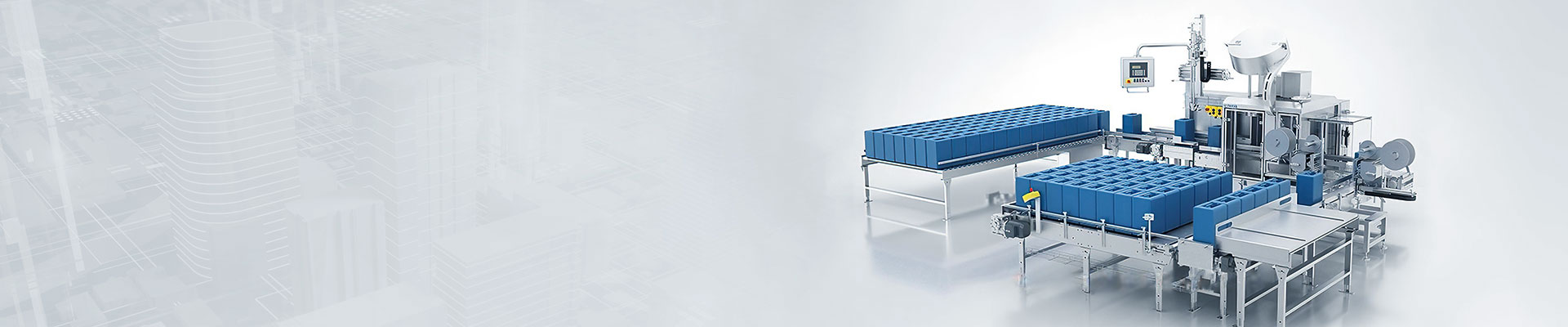
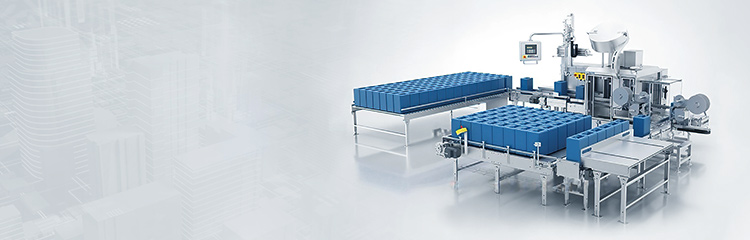
The mixer is automatically or semi-automatically completing the proportioning, weighing, feeding and distributing of raw materials at each time until the required weighing/feeding times of each batch are completed. At this point, PLC has completed a series of operations and controls. Such as the following target value calculation, raw material target value calculation, parameter automatic correction, etc. The main screen of each raw material and its parameter setting window have relevant parameters displayed, which can be used as control reference by the operator.

The process of weighing dosing machine is mainly the batching metering and feeding process. In batching metering process, firstly, the time of discharging from the material Feeder to the metering tank is controlled according to the weighing requirements, so as to control the amount of material entering the metering bin, and then the time of discharging from the feeder to the metering tank is controlled according to the material proportioning requirements, so as to control the weight entering the metering tank, thus completing the weighing process once until the specified weighing times for each batching are completed.
The weighing mixer mainly completes batching metering and feeding process control. According to the user login level preset by the operator, PLC manually sets and adjusts the set parameters such as weighing times, counterweight, ratio, impact difference, etc. At the same time, it displays the actual value of each batching and the actual value of under-value, as well as the next target value obtained by PLC operation, weighing times, times to be weighed, ratio, etc. The system also requires equipment control requirements such as batching interlocking, downward interlocking and upward interlocking.
Characteristics of weighing control system
1. Mitsubishi, Omron or Siemens PLC is adopted as the core, with small volume, high precision and good stability.
2. It can control multiple scales, different materials or control the output at the same time (depending on the process).
3. Intelligent control of batching time, no waiting between batching scales, shortening batching cycle and improving batching speed and output.
4. The latest WINXP system platform, which runs faster and more stably, produces pictures dynamically in real time, shows the production process, and has intuitive, clear and automatic recovery functions.
5. Powerful report function, which can record and store all kinds of data in large quantities, make tables and print, automatically compile and print the ingredient report after each production, and provide data such as date, time, report number and actual consumption of each material; The report is extracted manually by PC, and the report at the end of production is stored in the computer, which can be read infinitely to ensure the correctness and integrity of the production report.
6. The operation is simple. The system has three production modes: manual, semi-automatic and full-automatic.
Unique advantages of automatic Batching system
1.PLC has strong data processing ability, fast and stable sampling rate, and the batching process can completely meet the technological requirements.
2. The process can be set according to users.
3. Good reliability. The system has two control schemes (touch screen scheme and industrial computer scheme). When the other one has a fault, the other one will be switched on immediately without affecting the production, which can prevent the production from getting out of control when the production fails.
4. Real-time graphic display of production process and text display of production process are convenient for operators to operate.
5. Text files display production reports, formula reports, etc. (there are a number of printed contents to be selected by users themselves) with powerful alarm prompt function, which can minimize the rejection rate.
6. The frequency converter is used to control the discharging speed, so that all the materials can be discharged in the same time, which ensures the uniformity of ingredients.