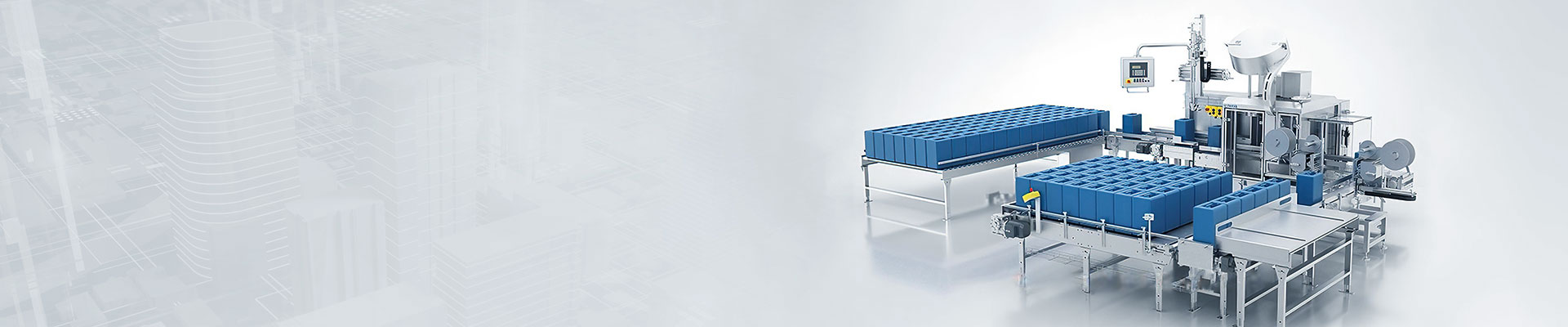
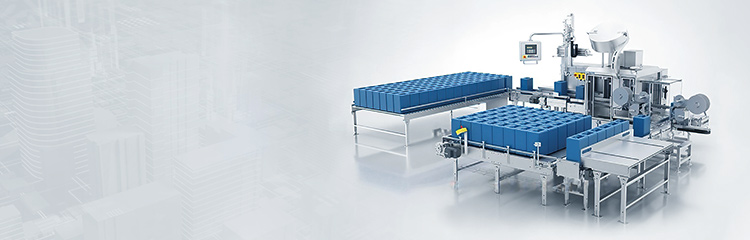
Pus Liquid Filling Machine is mainly used to collect the set value of filling quantity, process the pulse signal of weighing module, drive the relay to drive the frequency converter to control the motor and centrifugal pump to convey the material, calculate the pulse signal of pipeline tube flow through weighing module, get the weight of liquid actually discharged from the weighing system, and control the operation of the motor according to the difference between the actual filling quantity and the set value, so as to realize the precise control of filling quantity according to the actual need.

Liquid Filling machine by the programmable controller and Electronic scales to form a two-stage computer control network, through the field bus to connect the field weighing instruments, control computers, PLC, frequency converter and other high degree of intelligence, fast processing speed equipment. PLC is mainly responsible for automatic filling machine fault detection, display and alarm, and at the same time to the frequency converter output signals, frequency converter to complete the regulation of the role of the rotational speed of point electronic scales.
Electronic scale weighing is the instantaneous flow, the host computer is given to set the flow, the two in real-time measurement deviation. Adopt the most widely used in industrial control PID regulation for the actual control of the flow, according to the flow deviation, the use of proportional, integral, differential calculation of the control amount, through the frequency converter to regulate the speed of the electronic scale, adjust the amount of feed, so that it is equal to the set value, to complete the automatic filling process.
In order to realize accurate production, to avoid the production process of human error caused by production losses, and even accidents, automatic filling machine through the feeding process, the filling process of the instruction information checking confirmation, the important steps of the electronic signature, the material and container code identification of the constraints to ensure that the automatic filling machine to perform the correctness of the machine.
Adopting the CS structure, the control and management server manages the entire automatic filling machine as the filling center server. Through the industrial Ethernet as the network, it connects the operation station of each process. One operator station is placed in each process and connected to the equipment of each process. The functions of each station are realized through the operating station.
Basic parameters:
Maximum weighing capacity: 300kg.
Minimum sensing capacity: 0.1kg.
Filling error: ±0.1-0.2kg.
Filling speed: 200L about 150-180 barrels/hour.
Control: 2-speed control.
Filling method: Insertion type, liquid level up.
Gun head line: Teflon gun head, valve + Teflon hose.
Structure material: host SUS304 stainless steel, conveying palletizing carbon steel anticorrosion paint.
Weighing platform size: 800 x 800mm (304 stainless steel power raceway).
Empty drum raceway: 800mm×2500mm (304 stainless steel power raceway) with another 1200mm slope unpowered roller.
Heavy drum raceway: 800mm x 2500mm (304 stainless steel power raceway, 2 sets).
Separate barrel device: for 200L barrels, carbon steel anticorrosive paint structure, 304 stainless steel raceway.
Palletizing equipment: pan-transfer type, suitable for pallets 1200×1200×140mm, including supplying pallets, palletizing, and lower pallet conveying.
Pipe pressure: 0,2-0,6MPa (related to material properties).
Material interface: 4 DN40 flange connectors, interface standards can be provided according to the user.
Air Connection: User supplied 12mm air hose connector for quick coupling connection.
Power supply used: AC220/50Hz (user supplied to one side of the machine).
Using air source: 0.4-0,8Mpa (provided by the user to the side of the machine).
Use temperature: -10℃-50℃.
Base condition: Horizontal solid concrete floor, concrete thickness should be more than 10cm.
Optional models: standard and explosion-proof filling scales.