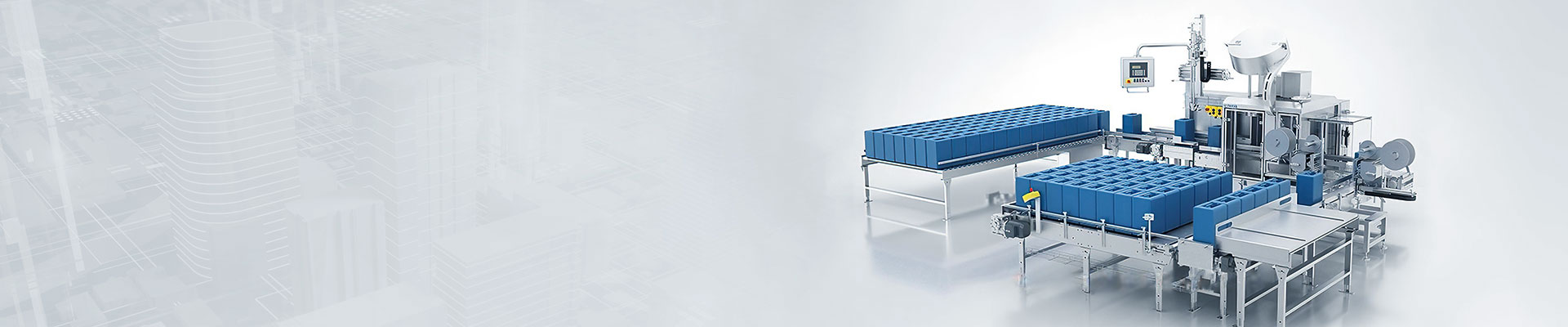
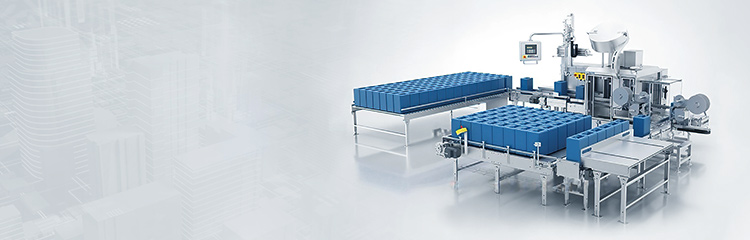
The mixing and weighing system adopts Siemens PLC, circuit breakers, relays, inverters and terminals, which can complete the equipment automation and process automation control. At the same time, the configuration control means to collect the data and adopt the high-end configuration software as the upper computer, through which commands are issued to manage the automation equipment and process. Standard industrial computer software and hardware platform as an integrated carrier to replace the traditional system, with strong adaptability, openness and good characteristics.

The weighing control system can be the weighing module and weighing instrument installed on the storage irrigation, etc. After receiving the signal from the weighing module, the weighing instrument completes the weight calculation and conversion within it, and at the same time, the required quantitative control value is set within the weighing instrument, and the quantitative weighing instrument outputs the switching signal when the value displayed by the quantitative dosing control instrument reaches the target value of the set quantitative dosing control. At this time, the switch signal is used to control the flow-breaking equipment on the installation pipeline through the mating relay or contactor, so as to achieve the effect of quantitative control.
The automatic Dosage system is a complete set of automation equipment to realize dynamic weighing and dosage control through electrical control management and visualization man-machine software configuration. The electrical control part of the system adopts Siemens PLC, which is programmed and controlled according to the production requirements; the software adopts man-machine group configuration, according to the process requirements, through the monitoring system and PLC program to control the weight and flow rate of the materials loaded into the weighing hopper, so as to realize accurate measurement and dosage. The system has strong stability and high cost performance, and can provide accurate measurement data and control means for production control and management of various industrial sites.
The dosing equipment adopts automatic control to realize automatic control and supervision of the process of raw material feeding, weighing and measuring, vacuum feeding, dispersing and mixing, etc. The dispersing time and cylinder number can be selected and adjusted on the computer according to the production requirements, and the opening and closing of the motor equipment and the opening and closing of the feeding valves in the process are all controlled by the computer. Finished product filter filling adopts fully automatic filling line, and the palletizing process is robot palletizing.
The automatic dosage system consists of industrial computer, PLC module, industrial configuration software, intermediate relay, AC contactor, thermal relay, air switch and so on. Under Windows environment, the actual flow chart drawn by using industrial configuration software can make the flow of each motor, control valve, pump and pipeline of the production line displayed, which can be very intuitive to understand the production situation and control the process of the whole system. The whole system is centralized in the central control room. The center control room is set up next to the platform in the workshop, which is used to place the main control cabinet and the center control console.
1)Feeding and metering
The incoming material of additives is transported to the feeding area of additives, and many additives are sucked into the reaction tank through vacuum, and the inlet adopts quick-connecting hose which can be accessed to different pipelines of additives reaction tanks (many kinds of pipelines can prevent mixing of materials). There are liquid level switches installed on the auxiliary reaction tanks, when the liquid level is lower than the lower limit, the central control room alarm, prompting the need to replenish the material; when the liquid level is higher than the upper limit, the central control alarm, the feed valve is automatically closed.
Measuring process: input the formula before production, the computer according to the formula amount of linkage to start the corresponding automatic valve to start feeding, when the weighing reaches the set value, the weighing module automatically closes the feed valve, and at the same time to start the measurement of another additive. When the metering is finished, the discharge valve of the metering tank will be opened automatically and the corresponding automatic valve on the E1 dispersing kettle (the number of the kettle will be set first) will be opened, and the additives will be sucked into the E1 dispersing kettle in a vacuum. After all the additives have been charged, input the weight of pure water to be charged in the same way, and then tap the pure water feeding valve to use a small amount of pure water to clean the metering tank and the downstream pipeline in order to ensure that there is no residue of the additives. A variety of additives for the measurement and delivery of automated control process, metering tank can take the first additives, after adding water.
(2) Emulsion feeding and metering
Emulsion feeding for tons of barrels or tanker trucks to feed, transported to the feeding area, discharge pump outlet quick connect hose connected to the emulsion tank pipeline, (because of the short distance, less residue, a variety of emulsion feeding pipe to take the co-pipe way), emulsion tank material PE, are translucent material, in the feeding, manual confirmation of the level of the estimated amount of unloading, to prevent overflow.
Measuring and conveying of many kinds of emulsions is an automatic control process, utilizing the emulsion measuring tank to measure. Computer control, according to the weight of the material, automatically open the corresponding valve, linkage start the corresponding transfer pump to start feeding, when the weighing reaches the set value, the chain feed valve and transfer pump shut down the valve to stop the pump. When the metering is finished, the discharge valve of metering tank will be opened automatically, and the corresponding automatic valve of E1 dispersing kettle will be opened, and the emulsion will be sucked into E1 dispersing kettle in vacuum. At the end of all the emulsion dosing, the same way to enter the weight of pure water dosing, tap the pure water feed valve, using a small amount of pure water to clean the metering tank and downstream piping to ensure that the emulsion is not residual.
(3) Pure water metering
Pure water metering is an automatic control process, the same operation process as the emulsion feeding.
4)Powder feeding and metering
Automatic loading system tons of powder from the pressure feed tanks into the powder bin for storage. A variety of powder measurement and delivery for automated control process, the use of powder metering tank measurement. Computer control, according to the weight of the charge, automatically open the corresponding valve, linkage start the corresponding screw conveyor to start charging, when the weighing reaches the set value, the chain feed valve and screw conveyor closed. Measurement is completed, the discharge valve of the metering tank is automatically opened, and open the GD1 transition tank feed valve powder into the transition tank storage, E1 dispersing kettle to add powder, take the bottom of the kettle feeding, vacuum the kettle, the transition tank discharge valve and the E1 tank feed valve is automatically opened, the powder from the bottom of the tank into the reaction kettle.