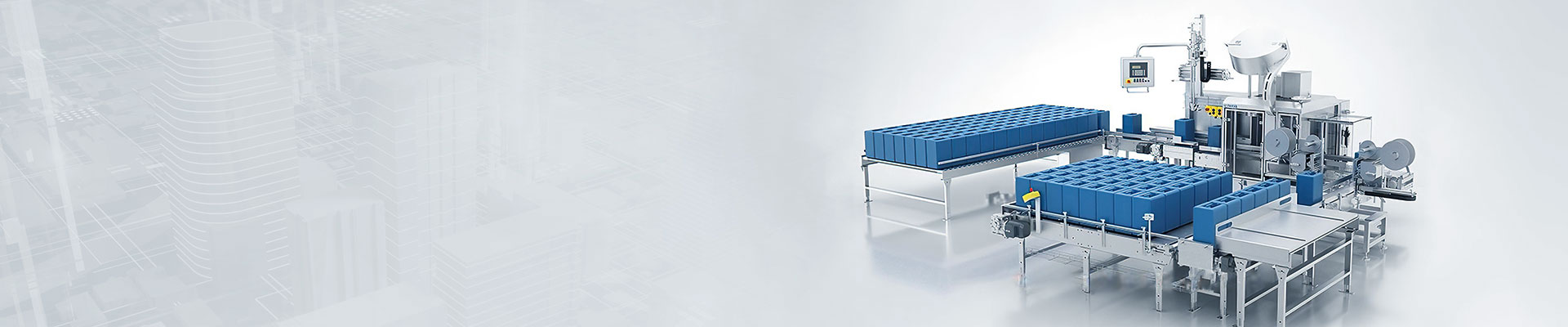
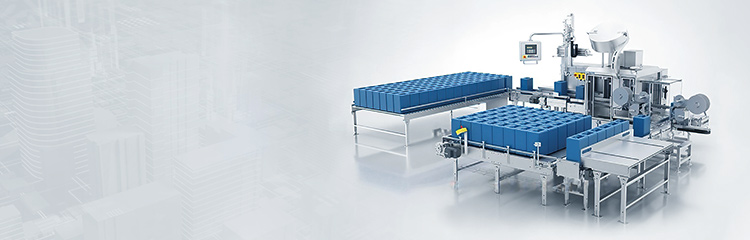
The weighing and feeding system adopts the screw metering method, and adjusts the material flow by controlling the screw speed through frequency conversion. When the system enters into working condition, the material from the spiral is conveyed and passed through the load cell for weight detection, and the speed sensor installed at the end for speed detection, the detected weight signal and speed signal are sent to the weighing instrument together, and the weight of the material in the spiral is detected and inputted into the totalizer with the help of the weighing module, and the frequency converter detects the speed of the motor, and inputs the speed information into the totalizer. The totalizer will process the received spiral speed signal and weight signal to get the cumulative amount of material and the time flow.

Weighing and feeding system can automatically complete the equipment for raw material dosing, which has many advantages, such as improving production efficiency, reducing labor cost, and ensuring the quality of products. Among them, the Weighing system is an important part of the feeding system and one of the core parts of the whole system, whose main function is to realize the accurate weighing of raw materials. It mainly consists of mixing system, feeding part, discharging part, control cabinet, inverter motor, inverter, weighing system and control operation panel. Using Siemens 1516F-2PNDPPLC to control the material proportioning, using the output of G120 frequency converter to control the motor speed, the operation control panel intuitively displays the motor speed, the process, the whole system can display and control the process of mixing and blending of a variety of materials in the production process.
During the production process, the materials added according to the formula are measured by the weighing control system, and the signal generated is inputted to Siemens 1516F-2PNDPPLC, which controls the weight of different materials and the order of feeding according to the formula, and after the feeding is completed, the mixing system is driven by the inverter motor to carry out the mixing. PLC and frequency converter are used to control the speed of mixing to realize the control of product quality. The frequency converter adopts G120 frequency converter with PROFINET industrial Ethernet port.
The automatic Batching system adopts bus type network topology. PROFINET field bus is used for communication interconnection. The signals of field equipment such as weighing module, travel switch, contactor, etc. are connected to the IO module of 1516F-2PNDPPLC with PROFINET communication interface by adopting the principle of proximity. The inverter motor is connected to the G120 inverter, and the PLC, HMI and inverter are connected to the same PROFINET bus network. The material flow rate is regulated by controlling the screw speed through the frequency conversion speed regulation. When the system enters the working state, the material from the spiral conveying and through the load cell for weight detection, at the same time installed in the end of the speed sensor for speed detection, the detected weight signal and speed signal together sent to the weighing instrument, with the help of the weighing module to detect the weight of the material in the spiral input into the totalizer, the frequency converter to detect the speed of the motor, the speed of the information will be input into the totalizer. The totalizer will process the received spiral speed signal and weight signal to get the cumulative amount of material and the time flow.