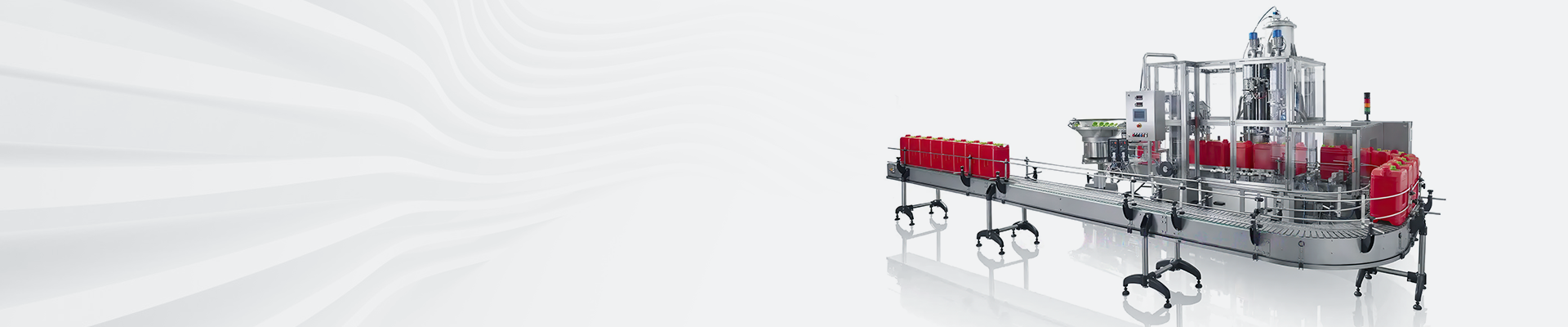
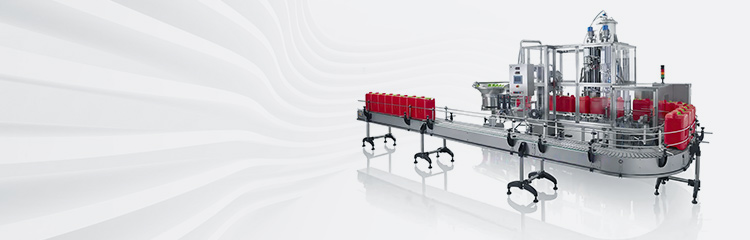

Summary:The polypropylene weighing and batching system ensures product quality, reduces consumption and labor intensity by improving pressure-temperature cascade batching and feeding measurement, and realizes automatic batching of polymerization kettles.
Propylene by the propylene pump after measurement into the polymerization reactor, and then add the catalyst, activator, hydrogen, etc., feeding is completed, to the polymerization reactor jacket into the hot water to warm up, when the reaction kettle temperature reaches 70 ° C, the reaction kettle pressure reaches 3.5 MPa, the reaction kettle polymerization reaction to release heat, so that the reaction kettle pressure continues to rise. In order to maintain the reaction kettle pressure constant, start to polymerization kettle jacket and even the reaction kettle water coil into the cold water, remove the reaction heat, stabilize the reaction kettle pressure, until the end of the reaction.
After the operator sends out the feeding control signal through the weighing and batching system button, the programmable controller confirms which polymerization kettle the propylene is to be fed to and sends out a signal to open the feeding valve of the kettle as well as the pneumatic three-way ball valve, and the propylene is put into the polymerization kettle through the pneumatic three-way ball valve to the accurate detection of the mass flowmeter, and the mass flowmeter sends out the flow pulse signal at the same time to the programmable weighing controller to carry out the calculation of the feeding quantity and reach the set amount of propylene, and then sends out a signal to the weighing controller for feeding. After the set amount of propylene is reached, a weighing and dosing signal is issued to make the pneumatic three-way ball valve act, cut off the feeding and wait for the next reactor to be fed.
In the process of polymerization reaction heating - constant temperature feeding system, the reactor pressure is chosen as the main weighing and dosage parameter, and the reactor temperature or jacket water temperature is usually used as the secondary adjustment parameter. The process of polymerization reaction heating and constant temperature is a chemical reaction of heat absorption and exothermic process, need hot water and cold water switching alternately, so that in the initial stage of the reaction into the hot water heating to make the polymerization reaction, when the temperature rises to about 70 ℃, the pressure reaches 3.5MPa, the polymerization reaction starts a lot of large-scale, release a lot of reaction heat, the dosage system automatically pass into the cold water to take away the heat of the reaction, to prevent the over-temperature and over-pressure. The following improvements have been made to the polymerization reactor temperature and constant temperature weighing and dosing:
A. Adopting automatic adjustment of reactor temperature - reactor pressure string jacket cold water valve, reactor coil cold water valve, automatic control of hot water valve, adjusting the reaction heat inside the reactor is not easy to take away the drawbacks.
B. 12 polymerization reactors share one hot water tank and one cold water tank. In order to make sure that the cold and hot water in the jacket are returned to each other and do not interfere with each other, a quick cut-off valve for cold and hot water out of the jacket is designed to interlock with the water-cooling and hot-water regulating valve for water in the jacket. When the jacket is fed with hot water, the hot water regulating valve operates and interlocks with the hot water quick shut-off valve, and the hot water is returned to the hot water tank; when the jacket is fed with cold water, the cold water regulating valve operates and interlocks with the cold water quick shut-off valve, and ensures that the cold water is returned to the cold water tank, and the quick shut-off valve valve position indicator is set up in the batching room to monitor the position of the outlet valve operation.
The dosage system will open the corresponding quick shut-off valve after setting the specified time to ensure that the hot and cold water stored in the pipe can still be returned to the original place to avoid heat loss.
The automatic weighing and dosing of polymerization reactor, feeding accuracy, reactor temperature, reactor pressure adjustment, adjustment index, meet the requirements of process production, greatly reduce the labor intensity of workers, reduce production consumption, truly automated to facilitate the production of convenient operation.