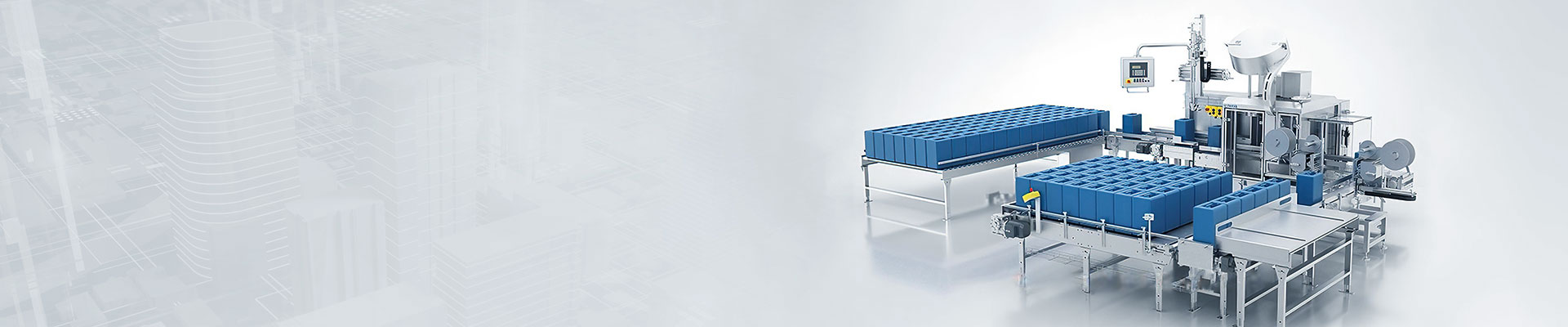
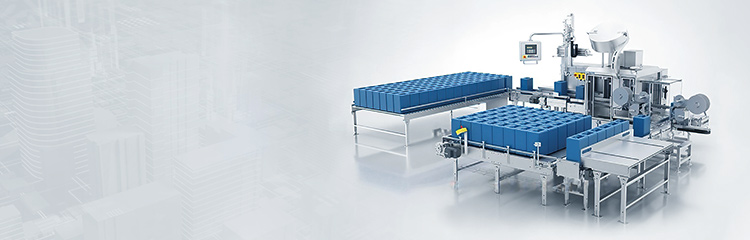
Mixing system is a kind of intelligent weighing system integrating control and management, with superior performance, stability and reliability. The product takes imported high-grade industrial computer as the mixing host, and combines with operation desk, analog screen and scale body to form a complete control system, and flexibly composes a machine and a scale and a machine and a scale according to the user's technological needs, and the selection of this system can greatly improve the enterprise's production efficiency and management ability.

The mixing system generally includes raw material receiving and cleaning, crushing, batching, mixing, granulation, finished product packing and storage, and dust removal and fire fighting systems, etc. Each production link is an independent production section. Weighing and mixing machine in each system is relatively independent, the production of automation, including the automatic control of the entire system and the automatic control of each process as well as the automatic control of individual equipment. PLC is responsible for controlling the operation of the field equipment and access to its operating status and fault information, sensing system to collect field information data computer using network communication to obtain data for storage and management, dynamic display of the process, equipment operating status, production data, alarm information, and to generate various types of production reports. Its core control component PLC, the use of modular programming ideas, separation of subsystems and relatively independent of the internal functions, and the functional blocks in accordance with the production system process flow through together to form the entire system of centralized control, and through the network to achieve and production management of remote monitoring command system.
The automatic Batching system consists of PC, PLC, Feeder, hopper, weighing module and actuator, etc. The upper computer transmits the raw material formula data to the lower PLC, and then it is controlled by PLC. Various kinds of raw materials are distributed into the corresponding batching silo for storage through the roof conveying equipment and distributor. The raw materials are sent to the hopper scale by the feeder respectively in sequence during dosing. Raw materials with large proportion (>20%) are sent to the large hopper scale; raw materials with small proportion (5%~20%) are sent to the small hopper scale for weighing. The weighing module detects the quantity of each material and transmits the signal to the weighing controller to control the feeding of the feeder, thus controlling the dosing of each material. When all the materials in the silo are weighed and dosed according to the set recipe requirements and reach the specified cumulative quality (quantity of each batch), the PLC opens the material door according to the control program and puts the materials in the hopper scale into the mixing chamber of the feeder for stirring and mixing. Mixing machine to achieve a predetermined mixing time, that is, the mixing uniformity to meet the requirements, under the control of the PLC, the material door opens out of the material, send the material to the buffer bin, fall into the finished product scraper-type conveyor, sent to the entrance of the bucket elevator lift to the mixing silo storage, to the next process.
Batching process is the key link in the production process, and its batching accuracy directly affects the quality of the product. Mixing feeding system to realize the two or more materials in accordance with a certain ratio of automatic quantitative addition to the mixer, after mixing to meet the predetermined requirements of the automatic discharge process. Through the comparison of the advantages and disadvantages of common dosage mixing technology program, choose the multi-material weighing mixing technology show. That is, all the measured material according to its physical properties or weighing range for grouping, each group with the corresponding measuring device to achieve the measurement operation, so as to economically and accurately complete the entire dosage process. Multi-material hopper weighing mixing process can significantly shorten the mixing time, significantly increase the output, combined with the production situation, the mixing process is selected as a multi-material double-weighing simultaneous dosage process.
The upper computer selects the brand machine with standard RS232C communication white and printer interface, this system requires high control accuracy, according to the number of input and output signals, the lower computer selects a Mitsubishi FX~-80MR PLC and two FXN-16EX expansion units, and selects the SC-09 programming cable as the connecting line for the communication between the computer and the PLC. In the whole feeding system, the load cell is a very critical component, how accurate it is, directly affects the accuracy of the system's dosage. This system selects resistance strain type weight sensor, its accuracy meets the requirement of dosage, it should be one level higher than the dosage accuracy.XSB-A weighing display controller is a kind of multi-purpose instrument, with fast speed and high accuracy, it owns many special properties which are very suitable for the application of weighing display and control.
The computer transmits the corresponding formula and production process parameters to PLC according to the production process, PLC controls the frequency converter to start the batching winch working according to the formula parameters and the feeding order, and the weighing signal is detected by PLC. Feeding system working sequence: after weighing is completed, when there is material in the feeder, the hopper scale door is closed; when the feeder is discharged and closed in place, the hopper scale door is opened. After the hopper scale door opening time arrives, the residual material on the hopper scale will be detected, when the residual material exceeds the limit value, the system will alarm and the hopper scale door will not be closed when it is lower than the limit value, the hopper scale door will be closed. When the hopper door closes in place, if the scheduled batch is not completed, the dosage continues and a signal is sent to add premix and grease. After the premix is added and the answer reset is completed, the mixer starts mixing and after the mixing time is reached, the mixer opens the door to discharge the material according to the material level in the buffer hopper.