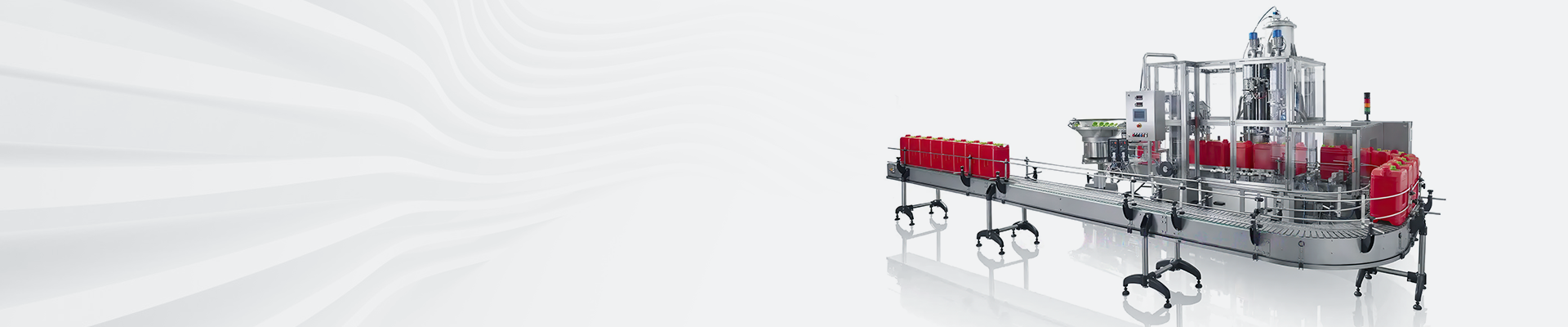
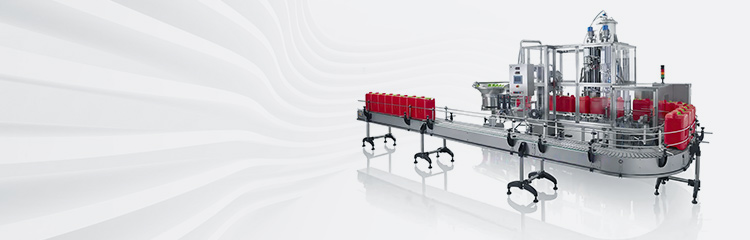

Summary:The batching system consists of a dehydration tower, an alkali washing tower, an alcohol recovery tower, a top tower, a finished product tower, four reactors and tank area batching.It is also a production process of chemical synthesis and physical fractionation.
Propionic acid butyl batching is a continuous metering dosing system for the production of chemical coatings as a product, the feeding system has a total of dewatering tower, alkali washing tower, alcohol recovery tower, pulling tower, finished product tower, four reactors and tanks dosing and other components. It is another production process of chemical synthesis and physical fractionation. The raw materials are propionic acid and butanol, and the product is butyl propionate, which is used as chemical raw material for coating products.
2、Batching scale
The automatic batching system has two operation stations, one of which is also an engineer station and one control station, and the central control room is equipped with UPS, printers and other accessories.I/O point configuration: AI (analog input): 89 points (e.g., temperature, pressure, liquid level, flow rate, regulation of the pump's frequency feedback, etc.), AO (analog output): 32 points (all 4-20mA current output), DI (digital output): 32 points (all 4-20mA current output). AO (analog output): 32 points (all 4-20mA current output), DI (digital input): 24, DO (analog output): 16 points, a total of 28 control circuits, including 13 single-loop control circuits, 15 serial control circuits, frequency control circuits of 8, the field actuators are mainly composed of pneumatic control valves and frequency control pumps.
3、Weighing and batching system program
I. Design principle
Propionic acid butyl process environment for the medium temperature, low pressure, flammable, explosive, control medium corrosive, temperature and pressure control, directly affect the quality of the product and the amount of product yield, the design of the control program takes into account the above characteristics, the temperature, level as the main loop, the corresponding flow as a secondary loop of the cascade control loop and the frequency converter (main/standby switching) control and the top of the tower pressure safety control and other factors as a priority, so that the temperature, level as the main loop, corresponding flow as a secondary loop of the serial control loop and frequency converter (main/standby switching) control and tower top pressure. Safety control and other factors as the focus, so that the overall program is more reliable, flexible and stable.
Second, batching control mode
The batching control system adopts PCC800 small-scale centralized control batching, which is based on intelligent, digital and networked design ideas for small and medium-sized industrial equipment or production process with modular flexible design; realize process control, logic control, sequence control integrated; that is, it can be modular decentralized joint control and low-cost stand-alone configuration; provide open data interfaces, field buses and Internet access, and absorb the latest electronic, network and control technologies. The latest electronic, network and control technology, a new generation of small and medium-sized centralized control of automatic batching system MicroDCS, with high reliability, open system, powerful, flexible and convenient, cost-effective features.
a) Reliability
Batching design, development and production process strictly comply with the international "ISO9001 quality management system", and has taken a variety of measures to ensure reliability;
Arbitrary redundancy design, which includes power supply, master control template, communication network and I/O template can be configured redundantly according to reliability;
Signal intelligent conditioning and isolation technology: based on SmartBUS dexterous digital bus technology, supporting the full range of signal modules automatic identification, arbitrary mixing, open protocol, feeding system access can be self-diagnostic, self-calibration, self-recovery, fault isolation, and automatic compensation for environmental impact. Field I/O signals fully realize the "point - point isolation", "point - machine isolation";
Multi-processor distributed processing, coordinated work: I/O modules, I/O templates, control templates, communication templates, etc. are equipped with corresponding microprocessors, division of labor, danger dispersion, high reliability, strong stability, support for template fault isolation, online insertion and removal, online repair;
Standard 9U/6U/84TE chassis, pin connector, effective dustproof and heat dissipation measures.
b) Ingredients openness
All-round open design: based on the Chinese WINDOWS-NT/2000 system environment, full support for ActiveX, OPC, ODBC; provide OLE automation server interface, DDE data exchange interface, driver program interface and other all-round open to the user;
Conform to IEC61131-3 standard configuration language, including function block diagram FBD, ladder diagram LD, structured text ST and so on;
Analog input, full support for the full range of industrial standard signals (hot spot resistance, hot spot coupling, current, voltage, type II/III standard signals, etc.) input, do not need to adjust the hardware configuration, only the software set the signal type, signal range, and confirm the wiring method;
Comprehensive support for TCP/IP protocol, support for client-server mode, the ingredients network has great flexibility and flexibility.
C)Powerful, flexible and convenient
Screen configuration using the Russian TRACEMODE application software, the software screen gallery rich, vivid animation display, online help is clear, easy to learn and understand;
Real-time operation software SunyRTM, expanding advanced control and process control algorithm set, providing 123 kinds of standard algorithm modules, in line with IEC61131-3 international standards, advanced and flexible graphic configuration, image intuitive, just formulate the function block, variable drag and drop connection, no programming can be completed without the control program;
I / O template intelligent, powerful, computing and processing power effectively decentralized, significantly reducing the control template computing burden and network communication load, so that the automatic dosage system operation detection and fault diagnosis capabilities can be improved, the module adopts intelligent conditioning and signal isolation technology, less types, easy to maintain, easy to select and change, spare parts, spare parts less;
Any one of the nodes on the network can actively send information to other nodes at any moment without distinguishing between master and slave, and the multi-machine backup and communication mode is convenient and flexible.
Third, process control program
1、Heat balance control of reactor and dehydration tower
The heat energy required by the reactor comes from the superheated steam, how to control the temperature of the reactor is crucial, the superheated steam is regulated by the temperature and pressure reduction, and then reaches an expected process requirements, and then pumped into the lower part of the reactor, because of the hysteresis of the temperature, so the feed-forward cascade control of the temperature of the raw material in the lower part of the reactor and the flow rate of the steam is adopted as the basis of the control and the thermal balance of the raw material feeding pump is controlled with variable frequency, and the PID parameters are adjusted to achieve an ideal process requirements, through the adjustment of the PID parameters, to achieve an ideal process requirements. Adjustment of PID parameters to achieve an ideal heat exchange balance control, which is conducive to energy saving and increase product yield.
2、Liquid level and boundary level control
The feeding system has 21 liquid levels, 8 with control, the field instrumentation are used EJA field level meter, to ensure that the level of automatic dosage system access accuracy, including the pulling tower and the kettle kettle level adjustment of the tower for the frequency control, the remaining 6 for the level and the corresponding flow rate of the cascade control, the level of the material control tends to be balanced.
3、Optimized control of pulling head tower
Adopting series control of temperature difference and reflux of sensitive plate in the drawer tower, series control of temperature and steam flow in the reboiler, and frequency conversion control of liquid level and discharge at the bottom of the tower to further optimize the material control of the drawer tower, to increase the product yield and to reduce the energy consumption.
4、Pressure safety control
In order to ensure the sensitivity and reliability of pressure, the on-site instrumentation of the process tower top pressure of the vacuum automatic dosage system adopts EJA absolute pressure transmitter, and the actuators are regulating valves and pneumatic safety valves, so that the automatic dosage system can respond positively to the slight change of pressure, which ensures the safety of the automatic dosage system.
5、Other functions
Historical trend curve record and query function;
The trend screen makes different historical trend screen for each kind of control parameter, and it is convenient to query the previous production records through the filter, and it is easy to rectify the PID parameter values by clicking the corresponding real-time parameter curve through the icon on the regulator panel on the main screen.
Report generation and printing function;
Shift and weekly reports are produced according to the user's needs, and the important trend screen can also be printed regularly and manually, which is more convenient for management.
Alarm value screen setting, display and sound and light alarm function;
A total of three pairs of alarm screens have been produced, and the set values can be modified online, with user-defined modification rights, making the alarm settings safe and reliable.
Operators, maintenance personnel are set up. The different levels of authority passwords and codes for process technicians and engineers, and the keyboard with shielding function, make the weighing and batching system control and configuration security can be improved.
The safety grounding of the field instruments and DCS system and the double power supply access of the backup UPS increase the anti-interference ability of the automatic dosage and the ability to cope with emergency situations.
4、Summary
PCC800 collector-dispersal feeding system used in propionic acid butyl process control automatic dosing, with low capital investment, received a very good result, effectively solved some of the complex process control program, so that the entire dosing operation is safe, smooth and reliable, not only increase the product yield but also greatly reduce the emission of three wastes, is a process automation in the control of fine chemical process control of a complete, good embodiment.