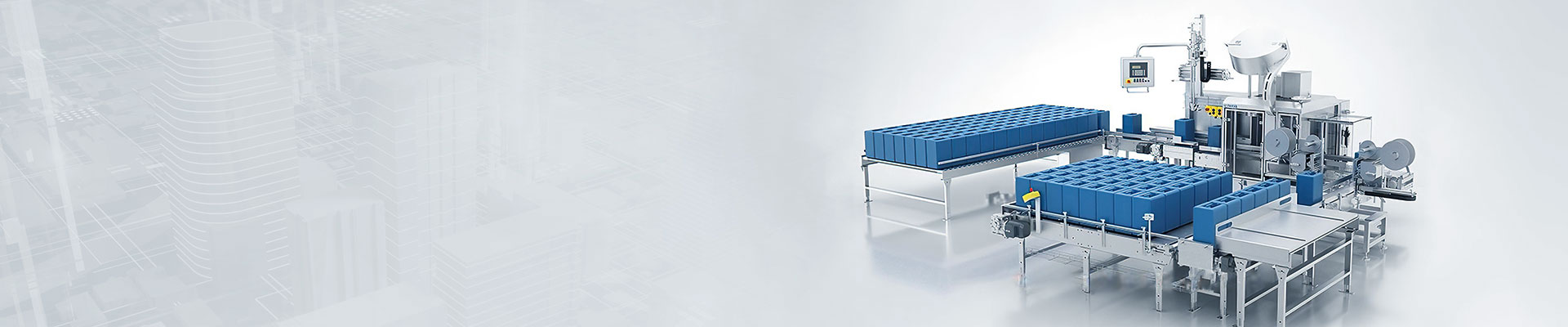
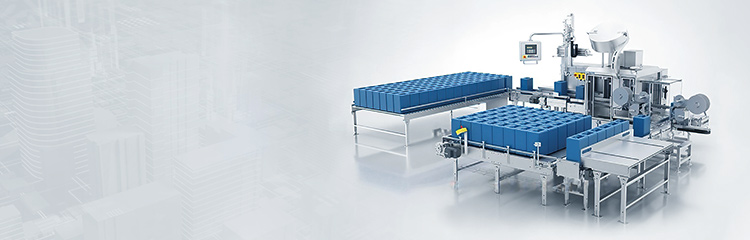
According to its specific production process and process equipment, the reactor weighing can achieve stable product quality through automatic monitoring and control of production parameters such as temperature, pressure, flow rate and batching accuracy. After particle size, moisture, viscosity and other quality testing, in a specific temperature, sealed and other environment storage and transportation. The use of computer for online monitoring and management has higher requirements for weighing speed, weighing accuracy, system compatibility and scalability.

Reactor weighing according to its specific production technology and process equipment, through the temperature, pressure, flow, dosage accuracy and other production parameters of automatic monitoring and control, to achieve stable product quality. After the quality testing of particle size, moisture, viscosity, etc., the products are stored and transported under specific temperature and sealed environment. Computer is used for online monitoring and management, which has high requirements for weighing speed, weighing accuracy, system compatibility and expandability. The upper computer of Weighing system is designed with PLC program, based on the upper computer with real-time process monitoring, overweight/overtime alarm, alarm processing, automatic data saving, querying historical data, printing formula and historical data. The control channel with PID regulation also allows it to be set up to calculate the conveyor load by the "absorption value method", and the channel can be equipped with weighing and metering, where the multifunctional characteristics are most fully reflected to meet the user's special needs.
Weighing and Batching system according to the actual use of the needs of the main structure and accessories configuration design, strict control of the reaction temperature, pressure, mixing and material concentration and other important parameters, so that the entire reaction process is more reasonable and adequate. It can be used to meet the weighing and batching, heating and evaporation, cooling and low speed mixing and weighing equipment in the reaction process. It is used to complete the process of sulfonation, nitration, hydrogenation, hydrocarbonization, polymerization, condensation and many other processes of organic dyes and intermediates as well as the reaction equipment.
The dosage control system has complete data recording and statistical report function to meet the needs of enterprise production management. Various types of reports include: Shift operation report: including the time of the beginning and end of each shift, set the target value of control according to the formula, the operation data of each scale, the output of dosage and the average hourly output of the reactor, etc. The statistics can also be divided into shifts. Statistics can also be divided into shifts. Cumulative statistics report, specify the starting and ending date and time of single scale and cumulative output, classification statistics and proportioning by material. Alarm record report, including alarm classification statistics, the number of alarms and alarm waiting time, i.e., the cumulative time between the microcomputer issuing an alarm and the operator making a keyboard response.