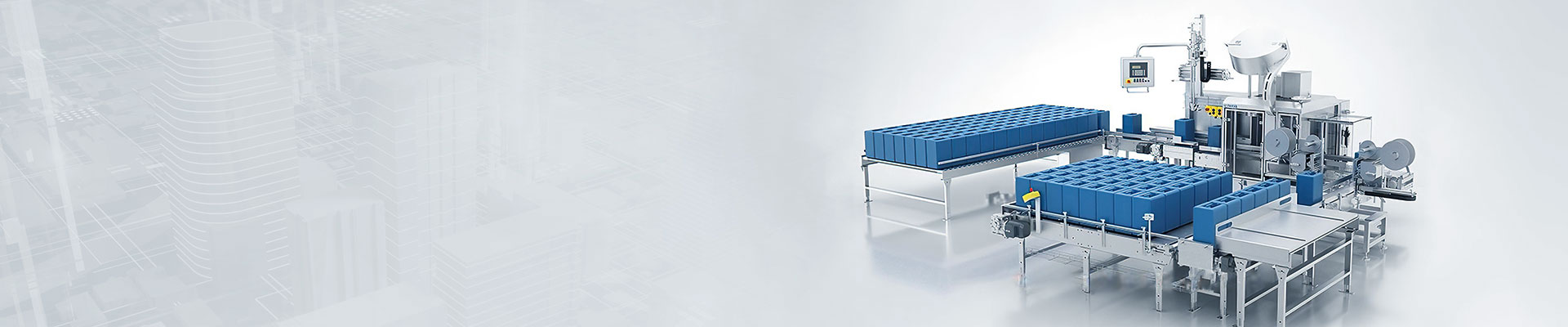
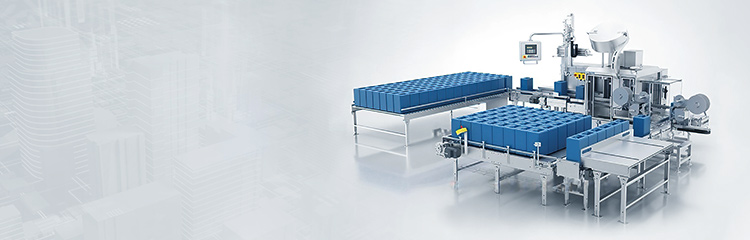
Weighing system with PLC as the control core, including the actuator, voice alarm, weighing instrument system and other parts, mainly control the elevator, classifier, crusher, feeder, screw, valve and other components. The operator station and engineer station are set up in the central control room and connected to the general control room for system monitoring and management of the whole plant. The weighing system is divided into operator stations and engineer stations, and is connected via Ethernet. The operator station is the same as the engineer station, with some limited functions.

Reactor weighing unit is mainly 0-inch touch screen, PLC as auxiliary control system, man-machine interface displays the proportioning parameters (formula) and monitoring and recording of real-time data. Under the automatic control mode, click the automatic dosage "start" button in the screen or the control cabinet "start" button, the touch control instrument will open the weighing valve of the dosage machine according to the set formula. If the system detects that a dosage valve is not closed, an alarm occurs and the system enters a pause state. Each batching machine is equipped with an advance quantity according to the weighing speed, when the control instrument detects that the weighing weight reaches the set value, it will subtract the advance quantity, and the control instrument will close the feeding valve. The advance amount can be corrected manually or automatically, so that the control instrument can control the dosage scale to reach the set target value every time the dosage accuracy.
The weighing control system takes PLC as the control core, including actuators, acoustic alarms, weighing instrumentation system and other parts, mainly controlling the elevator, classifier, crusher, discharger, screw, valves and other components. Operator station and engineer station are set up in the central control room and networked to the general control room for system monitoring and management of the whole plant. The Weighing system is divided into an operator station and an engineer station, which are connected via Ethernet. The operator station has the same settings as the engineer station, only some functions are limited. The upper computer screen simulates the three-dimensional dynamic process flow in the field, and it can set the valves, materials, water, etc., and display the information of temperature, flow rate, current, status of control elements, etc., according to the needs.
The reaction kettle dosage control system has the functions of human-computer interaction, communication, display and storage, printing, etc. It has data and graphic display, status monitoring, data input, information storage and other functional screens related to operation. The system can realize real-time process data monitoring, simulation display of process flow, real-time data record access, system operator authority setting, process parameter setting, setting alarm for running process events and switching between manual and automatic control. In the monitoring system, the on-site control instrument displays real-time flow rate, load, totalized value, temperature and so on. Temperature indication through the field temperature display instrument, pressure indication through the field pressure display instrument and motor current through the field display instrument is transmitted to the centralized display in the control room. Frequency converter regulation is equipped with automatic switching switch and communicates with the main control computer.