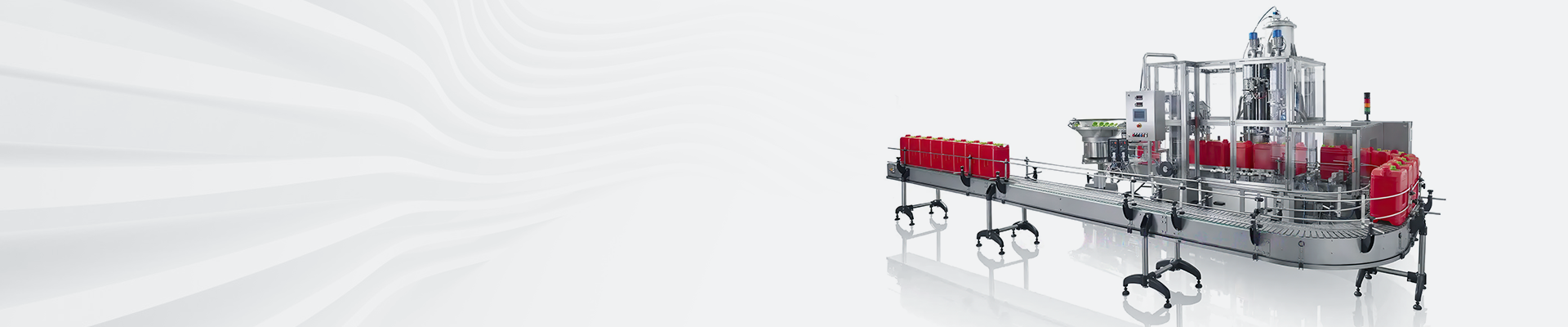
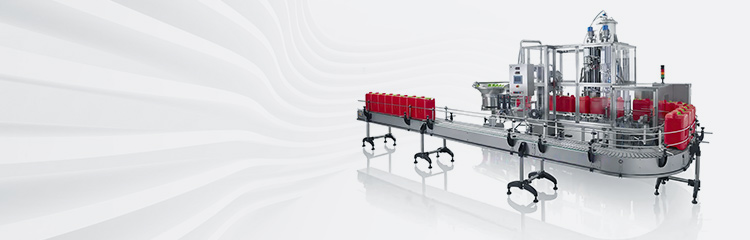

Summary:During the implementation of the plan, the batching system includes air flow, steam flow, oxidation temperature, evaporation temperature, fan speed, etc., using the advantages of DCS information sharing, historical data query and simple custom control algorithm compilation, according to the specific process on site. Control procedures have been prepared for the situation.
1. Introduction
Formaldehyde is a popular chemical product with wide application, simple production process and sufficient supply of raw materials, which is the backbone of downstream products of methanol, with an annual output of about 25 million tons in the world, and about 30% of methanol is used to produce formaldehyde. Formaldehyde production process is a complex chemical reaction process, for the operation of formaldehyde plant, people used to rely on the practice of testing and unit-combined instrumentation, due to the lack of accurate measurement of the production process parameters and real-time control, so that the formaldehyde product cost is high, the operating costs are large, and the product lacks competitiveness in the market. For this reason, there is a need to optimize the operation and control of formaldehyde.
The automatic feeding system has many advantages such as high reliability, open system, powerful function, simple maintenance, etc. It can provide efficient and high-quality monitoring of formaldehyde production, improve the stability and coordination of control, reduce the production of finished products and improve product quality, and enhance the competitiveness of the product market.
2, process introduction
Air oxidation method for the preparation of formaldehyde has two process routes: 1, electrolytic silver, pumice silver as a catalyst for the silver process, the use of this method, the concentration of methanol in the raw material mixture is higher than the upper limit of the explosive limit zone (36%), that is, in the case of excess methanol operation, due to insufficient oxidation of the reaction, the reaction temperature is high (generally 600-720 ℃), there is a dehydrogenation reaction occurs at the same time, so it is also known as oxidation -Dehydrogenation process. 2, Fe2O3-MoO as a catalyst for the iron process, this method is in the air-methanol mixture of methanol concentration below the lower limit of the explosion zone (less than 6.7%), that is, in the presence of excess air operation, due to excess air, methanol is oxidized almost entirely, so it is also known as pure oxidation of this method.
Raw methanol is weighed from the methanol reactor and transported to the methanol high level tank through the methanol pump to maintain a certain flow rate after filtration into the methanol evaporator, and at the same time the filtered air is sent to the bottom of the methanol evaporator by the Roots fan. Methanol after heating gasification and air entrainment, and air to form a binary mixture; and then and through a certain flow rate of steam phase mixing, the formation of ternary mixture, ternary mixture of superheater after superheating, into the fire-blocking filters, and then filtered the ternary mixture into the oxidizer, in the oxidation chamber of the high temperature of the heating element and the role of electrolysis of the silver catalyst, oxidation and dehydrogenation reaction occurs. The reaction gas quickly passes through the oxidizer emergency cooling section and under the cooling of the emergency cooling section, it enters the 1# absorption tower to circulate and absorb, and the circulating liquid is partially extracted as the finished formaldehyde solution (concentration of about 37%) and enters into the formaldehyde reaction kettle explosion-proof electronic scale and the formaldehyde finished product tank. After the 1 # absorption tower cycle absorption of the tail gas into the 2 # absorption tower, desalinated water as an absorbent, the 2 # absorption tower cycle absorption of the collected tail gas, through the tail gas liquid sealing tank, and finally into the tail gas treatment device as a fuel for combustion, combustion of the tail gas directly into the atmosphere, to achieve zero pollution emissions.
As long as the methanol as raw material, always inseparable from the methanol transportation, evaporation, raw gas (air, dosage, methanol gas) purification, filtration and flame retardant, conversion reaction, cooling and absorption, product storage and transportation and other links. Different means of each link and different combinations of different ways to form different process routes.
3、Batching control strategy
Weighing feeding system oxidizer temperature is an important indicator of production control, stable temperature control can improve the operation cycle of the catalyst, which can greatly reduce production costs. As can be seen from the above, the oxidizer temperature is the key to the whole formaldehyde production control, the variables affecting the oxidizer temperature are mainly:
(1) Temperature and pressure of the evaporator;
(2) Flow rate of dry air;
(3) The flow rate of dosing steam;
(4) Formaldehyde temperature at the outlet of the cooler. Of course, the concentration of methanol, the oxygen content of the air, the temperature of the air, the temperature and pressure of the steam all affect the temperature of the oxidizer.
In the production process, the greatest influence on the temperature of the oxidizer is the air flow, and if the amount of air change is greater than 5%, the oxygen temperature fluctuation can reach 10~20℃. Therefore, from the control point of view, air flow is a good variable used to regulate the temperature of the oxidizer.
Feeding system in the implementation of the program, dosing in advance allows the operator to set or confirm the best allowable state of a set of parameters (including air flow, steam flow, oxidation temperature, evaporation temperature, fan speed, etc.), the system will record these parameters in the database of the automatic dosing system platform of the operating system. The specific program is constant air speed, when the oxygen temperature change caused by external interference, first through the oxygen temperature-steam flow cascade adjustment circuit combined with the evaporator temperature adjustment circuit to quickly adjust the oxygen temperature: when the oxygen-water ratio deviation, according to the database of the best operating parameters, the production of the present, through the fuzzy mathematical modeling of the operation to amend the evaporation temperature, change the oxygen-alcohol ratio, and once again cause a small change of the oxygen temperature, and then Oxygen is adjusted by the oxygen temperature-steam flow cascade adjustment loop.
The temperature is restored to normal, thus restoring the oxygen-water ratio to normal, and subsequently the oxygen-alcohol ratio is also restored.
In addition, for the whole production process, especially the ignition stage, the weighing and batching system makes full use of the advantages of DCS information sharing, historical data query and simple customized control algorithms, and prepares the control program according to the site-specific process conditions. It not only improves the control level, stabilizes and enhances the product quality, but also greatly reduces the labor intensity of the operators. At the same time to ensure
production safety, and played a positive role in the actual production.
4、Control engineering
Oxidizer temperature is the focus of control, affecting the quality of finished formaldehyde products, ZJTU's control program, through the control of the fan speed and the main bypass regulator valve to achieve the control of oxidizer temperature.
5、Summary
Formaldehyde production in the use of automatic dosage system, can significantly improve the work intensity of workers, the level of production automation can be realized, the use of DCS powerful automatic control capabilities, the field instrumentation for coordinated operation. Formaldehyde production and quality has been significantly improved, DCS system unique interlocking control also improves the safety of formaldehyde production, the stability of the dosage also makes the production process stable and easy to control.