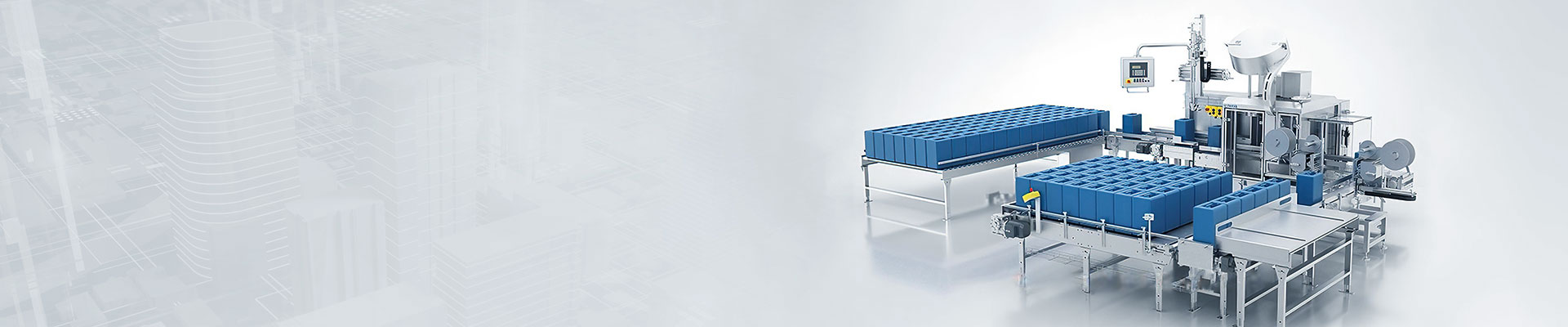
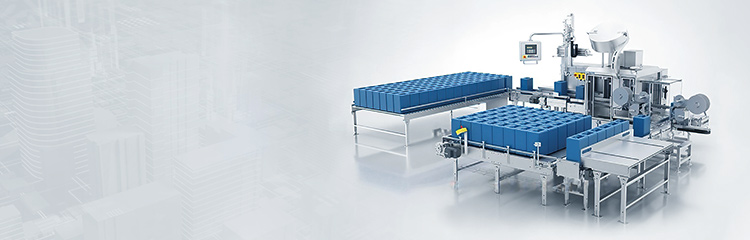
The design of the weighing and mixing machine is centered on the computer, and the operation process is also centered on the computer, and the process of feeding, temperature control, and discharging are all carried out by the sequential instructions issued by the computer. Each step of the operation process is carried out through the computer prompts and manual confirmation, the operation of the site with the computer system to carry out. Except for the operations that require manual cooperation, all other processes are automatically controlled by the computer system. The discharge rate of the weighing system affects the temperature of the mixing kettle and is controlled by detecting and regulating the flow rate. The control program automatically changes the feed flow rate according to the internal temperature rise rate to ensure that the internal temperature does not exceed the required range. At the same time, the jacket flow can be adjusted to stabilize the temperature in the dosing kettle.

Weighing mixer material into the pump body and compressed air mixing, the use of differential pressure of the warehouse, the material from the pump body discharged gas flow, and then sent through the conveying pipeline to the designated location and then from the material and the material to separate the gas gas, the material is divided into containers or shelves. With the required production formula, fully automatic weighing and distribution of powder (carbon black, etc.), granular materials (paraffin, etc.), oil and other materials, mainly applicable to the production of large and small material formulas, the intelligent storage of production formulas, call production formulas at any time, storage of production data, etc., to help product quality traceability. It can complete the following operations automatically and accurately for powder, granule, block and bulk materials in various industrial production environments: fully automatic weighing of trace materials, fully automatic quantitative dosage and fully automatic conveying control. Its stable and reliable performance, intelligent and accurate, will greatly improve the efficiency of the industrial production of trace substances Dosage system, at the same time completely eliminated the trace substances of manual weighing and dosage, feeding the error rate may occur. Additives trace component computer dosing and adding system can improve the dosing accuracy and dosing and weighing efficiency of trace components, completely overcome a variety of human errors, avoid multiple dosing and weighing and adding accidents, greatly reduce the economic losses caused by trace component dosing and weighing, and significantly improve the production efficiency and realize the safety, quality, cleanliness and high efficiency of trace component dosing, weighing and adding.
Dosing systems are also relatively reliable high density phase pressure air conveyors for high pressure (less than 700kPa) conveying of powdered materials. There are two ways to discharge a warehouse pump. Bottom discharge is a common method. The material is fluidized in a conical expansion tank, nozzle jet, or other means; the material can be discharged to the top of the vessel. The distribution of the conveying gas over the input surfaces in the storage tank depends on the nature of the material being conveyed. The self-searching dosing system allows flexible arrangement of the conveying pipes according to the topographical conditions, enabling centralized, decentralized, high and long-distance conveying. The transportation process is not affected by natural conditions, which can ensure that the materials are not affected by humidity and environment without pollution. The equipment adopts PLC control system, which can be controlled automatically or manually. After long-term production, it has stable performance, reliable quality and no dust pollution during transportation.
Product Features.
1) High energy efficiency
Due to the reasonable fluid structure, the material is in a good flow state, and the gas consumption is significantly lower than that of similar products. After years of production and development, we have improved the silo pump pneumatic conveying equipment process structure many times, significantly improving production efficiency and reducing energy consumption.
2) High material to gas ratio
Fluidization effect is good, gas consumption is small, raw material gas ratio is higher than natural gas. After indoor test, the equivalent distance is within 500 meters, and the feed sand gas ratio is more than 30Kg(ash)/kg(gas).
3) Low material flow rate
Due to the low air consumption, the ratio of material to gas is high, and the material is partly conveyed dynamically and statically through the pipeline. Therefore, the flow rate of the material is low during the conveying process, the wear and tear of the valves and pipes is low, and the life of the worn parts is long.
4) Powerful adjustment function
Various regulation methods, such as primary and secondary inlet regulation, allow the bin pump pneumatic conveying equipment to operate at a ratio of gas consumption to good fluidization.
5) Unique ways to eliminate blockages
We use a simple, easy to operate and rationally operated reverse pumping method, where only the material gas is directed through a plug valve and piping to the silo or flue inlet.
6) Support facilities are easy to fix
Silo pump pneumatic conveying equipment due to its low energy consumption and slow speed, silo material separation and filtration device can be smaller than the typical silo pump, reducing air pollution.
7) Small energy consumption factor
The energy consumption coefficient of the silo pump conveying system of the unit is less than 65 KW.h/t.m.
8) Advanced automation
A programmable (PLC) control system is used to fully automate the entire work process. The system can be set up for automatic or manual operation. The main control cabinet is located in the system control room.