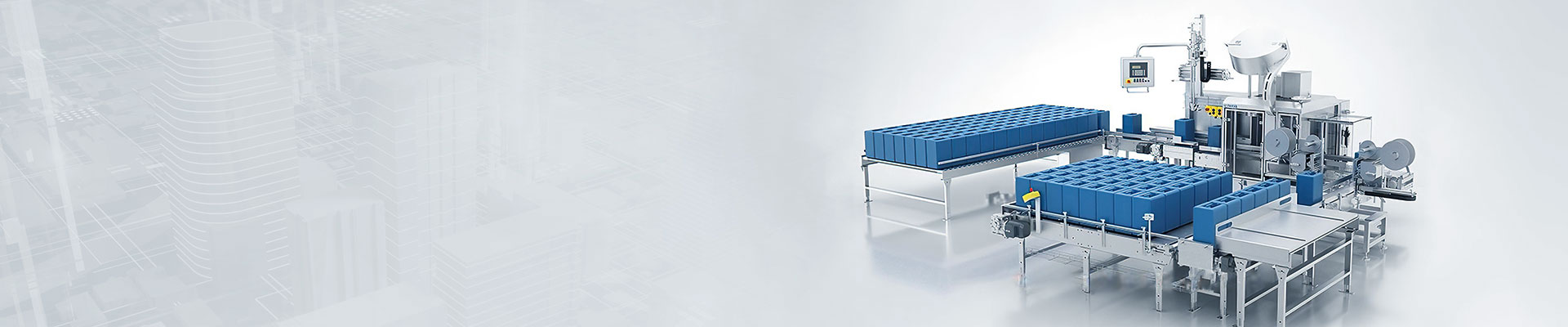
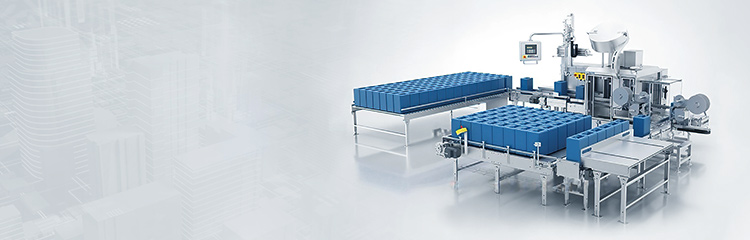
The operator of the mixer inputs the proportion of each raw material, the machine will calculate the weight of each raw material by combining the weight of each ingredient, and then control the opening and closing of the metering valve to distribute the raw materials to the weighing hopper, when each raw material is completed in accordance with the proportion of the raw material, the raw material in the weighing hopper will be discharged to the lower part of the agitator for stirring, and after the completion of the mixing, the whole process is complete.

The Batching system mixes different raw materials proportionally according to the pre-determined formula. In order to improve the precision and speed of batching, ensure the quality of the products and increase the output, it adopts the microcomputer control technology. Microcomputer-controlled matching production line. It mainly consists of pulverizer, elevator, blower, conveyor and distributor. The dosing part includes silo, Feeder, Electronic scale and mixer. The main function of the dosing part is that after the feeding equipment puts all kinds of different raw materials into their respective hoppers, the materials are discharged into the weighing hopper in accordance with the given proportion of the formula and weighed, and then sent into the mixing machine for a certain period of time for stirring and mixing uniformly into the finished products. Various fixed formulas are inputted into the computer beforehand, and the computer controls the discharging, weighing and mixing according to the proportion of the formulas, and detects the signals of the weighing module in real time, makes a judgment, and sends out the commands to each actuator of the dosage, so as to realize the automation of the dosage. The whole production system is equipped with manual control auxiliary mechanism, which can control the operation according to automatic or manual working mode.
The batching machine realizes automatic control and supervision of raw material feeding, weighing and measuring, vacuum feeding, dispersing and mixing, etc. The dispersing time and cylinder number can be selected and adjusted on the computer according to the production requirements, and the opening and closing of the motor equipment and the opening and closing of the feeding valve in the process are all controlled by the computer. Finished product filtering and packaging adopts fully automatic filling line, and the palletizing process is robot palletizing. It consists of industrial computer, PLC module, industrial configuration software, intermediate relay, AC contactor, thermal relay, air switch and so on. Under Windows environment, the actual flow chart drawn by using industrial configuration software can make the flow of each motor, control valve, pump and pipeline of the production line displayed, which can be very intuitive to understand the production situation and control the process of the whole system.
Product Features
1)Saving labor cost and raw material cost, the service life is more than 10 years.
2)Centralized management of raw materials to avoid waste and pollution.
3)Keep the factory environment clean and maintain the environmental system.
4) Favorable to maintain stable quality, increase production value and maintain quality system.
5)Favorable to improve the company's image, win the customer's praise and cooperation.
6) High degree of automation: the whole batching process is completed automatically, unmanned packaging, improve efficiency and save labor.
7)High dosage precision: static dosage, precision higher than 0.2%.
8)Fast speed: the whole batching process is completed automatically in 30 seconds.
9)Good dust removal effect: set up double dust removal channels with good sealing performance.
10)Provide accurate measurement data and control means for production control and management of various industrial sites.
11)Batching speed 3-10T/hour; Packing speed: 200-460 packages/hour; Packing quantity: 1-10kg; 10-50kg.