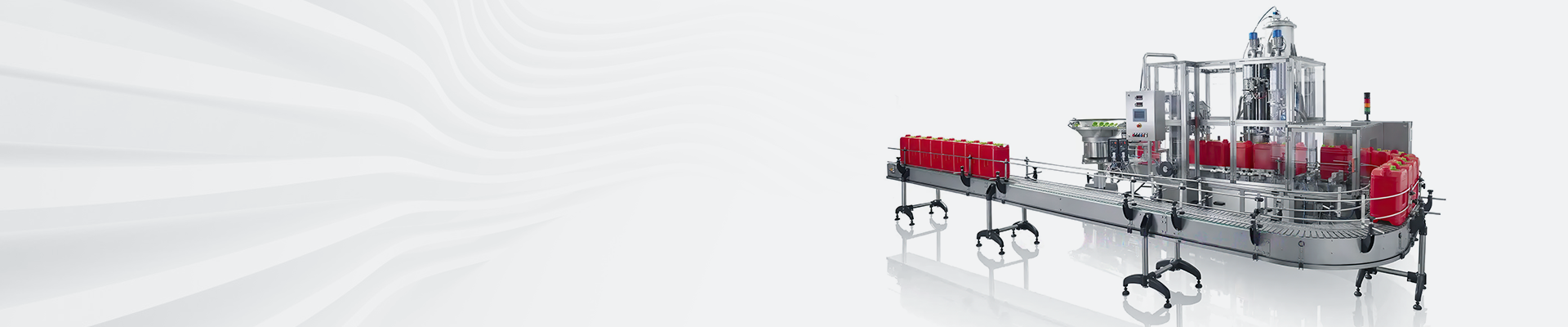
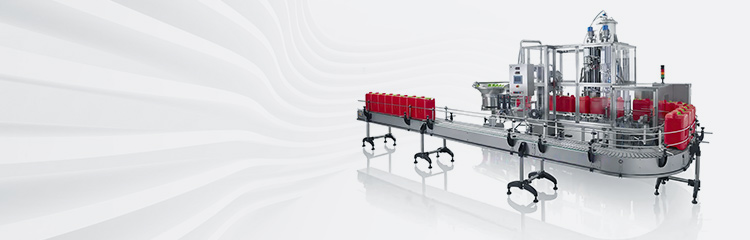

Summary:The batching system monitors and interlocks the mixing tank, realizes the mixing tank batching weighing control, the action of thermal oil, flue gas, cold air, hot air and other valves, and realizes the control process of the mixing tank air supply to combustion, and combustion to air supply.
1 static error and control
Static batching mode, a variety of materials are stored in different silos, generally using electric vibration, spiral or disk and other forms of feeding. Measurement is generally used to measure the warehouse, and equipped with pressure or pull type gravity sensor for force and electricity conversion signal amplified by the second instrumentation processing connected to the PLC or DCS to complete the measurement.
Static error, refers to the feeding system in the weighing part of the weighing accuracy in the non-production state. It depends on the design of the weighing hopper, the accuracy and linearity of the load cell, the consistency of all weighing modules on the same hopper, and whether the installation of the load cell is reasonable.
Generally 3 or 4 weighing modules are used to suspend (or support) the weighing hopper. In the design and installation of the weighing hopper, each weighing module should be subjected to uniform force as far as possible. When installing the tension load cell, the top and bottom should be connected by hook and loop so that it can hang freely without any horizontal torque and lateral force constraints, otherwise the accuracy will be affected. If the user requires high accuracy in weighing, a universal hook can be used. Optional sensor performance may not be exactly the same, need to be compensated. Weighing bucket (empty bucket) installed, first carefully adjust the force of each sensor, try to make it uniform, and then measure the output of each sensor. If a sensor output is low, the sensor should be added between the output and input of a few hundred kilo-ohm resistor; carefully adjust the resistance value, so that the output of the sensor and other sensors the same.
The linearity of the sensor has a great impact on its accuracy. Procurement must be noted that the sensor's linearity error should be smaller than the required static accuracy. However, with the development of sensor technology and data processing technology, the error caused by the load cell can be reduced to very small.
2 Dynamic error and control
This kind of error is also called the working error of the dosage scale, which refers to the error between the weighing value of the dosage scale and the given value. This error can be clearly reflected in the printout.
2.1 Feeding error
Feeding error, mainly due to the feeder failed to stop feeding at the right time and produce. To this end, can be used fast and slow double-speed feeding mode, the first fast feed, to 90% of the amount of material and then slow, to ensure that the amount of material under each time is equal to each time the material under the end of each time to be sure to automatically clear the zero. 1) Mechanical transmission error. At present, the vast majority of domestic feeders are powered by electric motors, and most of the feeding method of the cage or electric vibration type. Motor and cage connection is generally used in direct connection (coupling type) and chain type. Due to the inertia of mechanical movement, so there is always a deviation in the immediate control, the material is more or less. Especially the chain coupling type is worse.
2) Air material column error. From the dosage system stop signal to the feeder to stop, and from the feeder to stop all the materials fall to the hopper, there is always a period of time. This period of time the feeder fed out of the material commonly known as "air column". The error caused by the air column is called "air column error".
Design should minimize this error. First of all, minimize the distance between the feeder outlet and the weighing hopper. This can reduce the falling height of the material, that is, to reduce the "air column", the second can reduce the speed of the material to reduce the impact of the column, and ultimately achieve the purpose of reducing the error. Generally, this distance should be controlled within 300mm. In addition, the hopper does not affect the smooth discharge of materials, should try to reduce the height of the weighing bucket, three, the batching process, should try to first batch large amount of material, quickly increase the height of the material surface in the scale, reduce the "air column".
2.2 Material eccentricity error
Batching equipment design in general each feeding system by a separate mouth into the weighing bucket, so that each feeder feeding position are not the same. Especially distributed in the weighing bucket around the feeder, the feeding process will make the material piled up on one side more, the formation of eccentricity, resulting in "eccentricity error". For this reason, the process design should first try to ensure that the center of the weighing hopper feeding, and in the order to make the first under the material.
Material collapse error 2.3
Chipping is highly contingent. The adaptive function of the microcomputer is sometimes difficult to make a correct judgment, and sometimes the batch error will be carried to the next batch. Its control method, first of all, the feeder outlet near the use of double screw blades, in order to increase the binding surface and binding force of the blades; secondly, will be close to the outlet of the stranded cage blades away from the outlet of 60 ~ 80mm, to ensure that the material out of the outlet of a slanting surface, it is not easy to collapse, and thirdly, to let the feeder outlet slightly tilted up, so that it has a 3 ~ 5 ° angle of elevation, the use of gravity to control the collapse of the material.
2.4 Impact error
In the actual control, the first is to set up a buffer in the weighing hopper, commonly used cone type bulk feeder. First, it can reduce the impact force; secondly, it can make the material uniformly distributed in the weighing hopper, and thirdly, it is to improve the self-recognition ability of the dosage scale software, filter out the impact force, and improve the stability of the system.
Feeding system error
Dosing system error mainly refers to the error caused by the computer software can not correctly reflect the actual dosage situation. There are mainly mechanical vibration, electromagnetic field interference and other interference. Above, the various situations are analyzed separately. In actual production, a variety of errors is often a joint role, and each other's influence, comprehensive reflection. Therefore, in the pursuit of the minimum value of each error factor as far as possible, more attention should be paid to the best combination of the system to find the optimal solution.