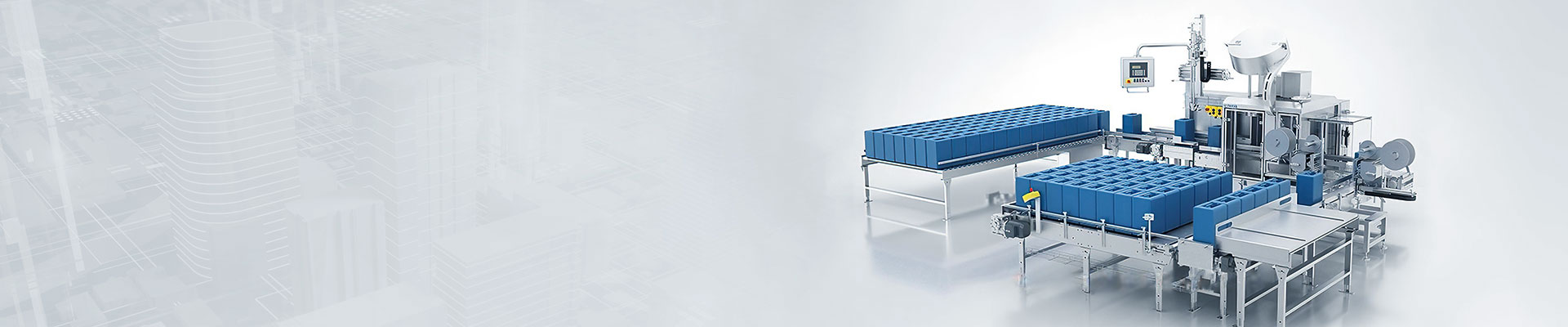
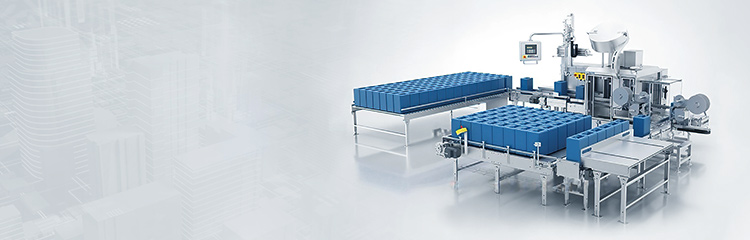
The automatic filling machine adopts Siemens S7300 series and ET200 module to control the filling according to a certain ratio, and at the same time, it gives the discharging system according to the information of the material level of each material reaction tank. According to the weight and chemical composition of the raw materials for proportion filling control. Adopting two-stage adjustable filling methods for large and small materials, the filling machine improves the accuracy and production capacity; equipped with top barrel automatic protection function for automatic lifting of the filling gun when the gun is not inserted into the barrel and not performing filling; the filling gun is professionally designed for ink, and it is easy to dismantle and install it quickly with bare hands and convenient for maintenance.

Automatic Filling machine using capacitance edge effect using the load cell detection area of the capacitance rate change and the spirit degree distribution characteristics of detection imaging capacitance chromatography imaging technology, to meet the requirements of non-destructive testing. Including the data acquisition part and control system, due to the simple operation and measurement principle of the Filling system, the capacitance edge effect is utilized to detect the safety of unknown liquids in insulated closed containers, in addition to ensuring the sensitivity, accuracy and speed of the detection, it can also significantly reduce the production and maintenance costs of the equipment and instruments.
Automatic filling machine adopts WIN7 system platform, stable operation, fast speed; real-time dynamic production screen, show the production process, operation is intuitive, clear, with automatic recovery function; the system contains a report function, data storage and recording function, tabulation and printing function, each time after the completion of production, automatic printing of ingredient reports, and record the date, time, report number and the actual amount of consumption of each type of material and other information; report The reports are stored in the hard disk of the computer, which guarantees the correctness and completeness of the production reports and can be read at any time.
The weighing and filling machine adopts fully automatic production from the picking up link of lifting buckets, only need to place the buckets of the same specification and model neatly in the designated position, the professional manipulator will accurately take out one bucket at a time, and accurately convey the buckets to the bottom of filling nozzle through the power track.
Basic parameters:
Maximum weighing capacity: 30kg
Minimum Sensitivity: 0.1kg
Filling error: ±0.1-0.2kg
Filling speed: 20L about 1500-1800 barrels/hour
Control mode: 2-speed control
Filling method: Insertion, liquid level up
Gun head line: Teflon gun head, valve + Teflon hose
Structure material: host SUS304 stainless steel, conveying palletizing carbon steel anticorrosion paint.
Weighing platform size: 400 × 800mm (304 stainless steel power raceway)
Empty barrel raceway: 400mm × 2500mm (304 stainless steel power raceway) with another 1200mm slope without power roller
Heavy drum raceway: 400mm×2500mm (304 stainless steel power raceway, 2 sets)
Separate barrel device: for 20L barrels, carbon steel anticorrosive paint structure, 304 stainless steel raceway.
Palletizing equipment: pan-transfer type, suitable for pallets 1200×1200×140mm, including supplying pallets, palletizing, and lower pallet conveying.
Pipe pressure: 0.2-0.6MPa (related to material properties).
Material interface: DN40 flange connector 4, according to the user to provide interface standards
Air Connection: User supplied 12mm air hose connector for quick coupling connection
Power supply: AC220/50Hz (user-supplied to one side of the machine)
Using air source: 0.4-0.8Mpa (provided by the user to the side of the machine)
Use temperature: -10℃-50℃
Basic conditions: horizontal solid concrete floor, concrete thickness should be more than 10 cm. optional models: standard, explosion-proof filling scale