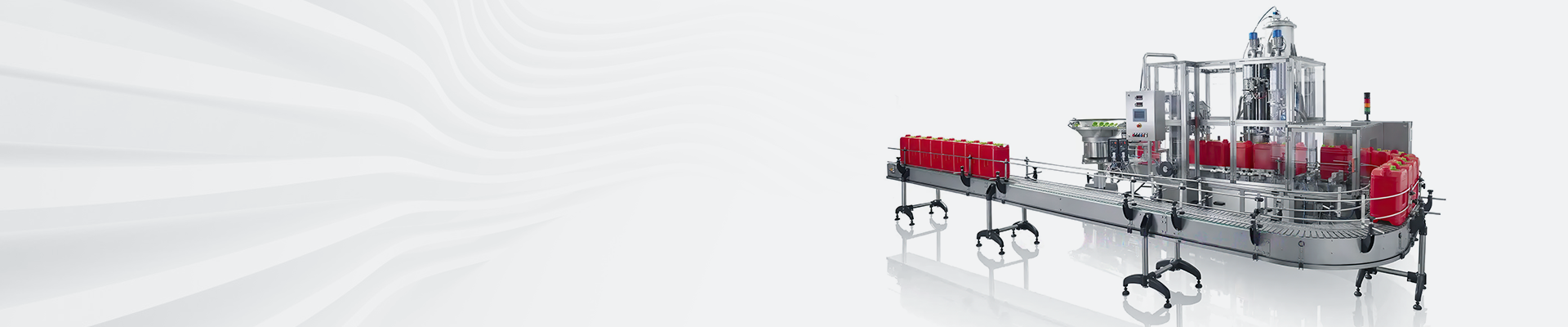
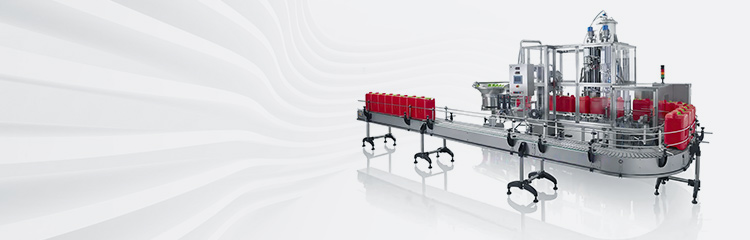

Summary:With the development of industrial control technology, mechanical equipment is integrated into a complex. PLC is a new industrial automatic control device with microprocessor as the core and integrated communication technology. Automatic filling system is widely used in food, chemical and other industries. With the production Driven by factors such as cost compression and consumer demand for diversified products, the traditional production model faces huge challenges. In order to reduce design and manufacturing costs and improve production efficiency, it is necessary to use PLC to develop and design automatic molding and filling systems.
With the rapid development of science and technology, commodity filling has become an important means of enhancing competitiveness, soft filling technology in the field of product filling occupies an important position, China's research on soft filling technology for a relatively short period of time, the domestic soft filling machinery field of technical immaturity, with the accelerated process of industrialization, many new technologies used in the field of filling, the enterprise to make the wax molding automatic filling machine put forward higher requirements. Most of the processing and manufacturing equipment rely on imports, some small factories with a weak economic base, the domestic equipment can not meet the production requirements, the development of small-scale soft package processing enterprises difficult. With the improvement of people's living standards, in order to celebrate special festivals on the craft wax demand is very high, the current wax processing technology in the United States and other developed countries with a high level of automation, China's wax processing equipment mechanization level is relatively low, the production equipment is in the imitation stage. 21st century after the PLC has become the leading control device in the field of industrial automation, and the degree of its application has become a measure of the country's industrial advancement of one of the symbols. Study the use of PLC technology to design automatic wax filling machine to improve production efficiency is of great significance.
1 automatic wax molding metering filling machine process and technology
1.1 Wax molding filling automatic production line process
Industrial production, there are many places need to powder granular bulk solids flow accurate measurement and control, with feeding equipment to form a control system equipment. Many production equipment dosing control system is widely used in cement, metallurgy, power, chemical and other industries, dosing plays an important role in industrial production: to improve the degree of automation of the feeding system is of great practical significance. Traditional mechanical systems and computer control can be combined to improve the economic efficiency of enterprises, mechatronics technology to realize the computer quantitative control is the inevitable direction of development. Computer control system is the use of computers to realize the production of automatic control systems, software technology and automatic control technology combined with the application of technology, the current industrial control computer is divided into PLC, based on the microcontroller measurement and control devices, etc. PLC is widely used and easy to use general industrial control devices, can constitute a single-chip control system with a distributed control system, the centralized control system using PLC control, the controlled object The data state does not need another communication line. Distributed control system controller using each other with the communication function of the PLC composition. Automatic wax filling line for industrial robots, industrial robots are automatic control of multifunctional operators, special automatic machine is adapted to mass production of automation equipment, industrial robots are flexible automation equipment with multiple degrees of freedom of the action function. Wax molding automatic production line is electromechanical integration of high-tech products, can weigh and bag powder and lumps and batch number printing and other operations to achieve automation, through the human-machine interface can be set for the corresponding parameters of the filling, MMI is the PLC's external equipment, through the touch of the keyboard can be to the PLC to enter the data to display the graphic. Wax molding filling automatic production line is the main part of the filling machinery China's filling machinery development began in the 1950s, after the reform and opening up, and gradually become a high-tech modernization industry. Filling machinery industry sector after years of development has begun to take shape, filling machinery industry in the rise of the national economy continues to develop and improve the
Oil dewaxing before storage in large tanks, part of the wax in the oil precipitation direct crystallization will affect the process of wax precipitation effect, must be heated to make the wax fully soluble in oil, after heating the use of plate heat exchanger for heat exchange, cooling the oil to save energy, crystallization tank oil cooling in order to increase the precipitation of wax particles collision aggregation of the need for appropriate stirring, stirring speed of 10 ~ 15r/min is appropriate, the oil crystallization of certain temperatures to maintain Longer time crystallization. Small crystal grain grows up to raise products 12~16h, oil crystallization to raise the crystal accompanied by more solid fat precipitation, the choice of hot unloading winterization filter alternating work to ensure the continuity of production. The dewaxed oil is pumped into the heat exchanger for heat exchange and then put into storage. At present, the domestic filling equipment factory specialization is low, automatic filling machine can only be material filling by workers handling, due to the low level of productivity in China's lack of scientific research personnel lead to, China's filling equipment after many years of development has been a great progress, but at present there is still a low level of product duplication of more than the production of independent development capability is weak, the lack of production of products of high technological content and other issues.
1.2 Wax molding filling automatic production line technology
With the continuous improvement of productivity levels, people are increasingly important to improve the working environment. In order to meet the requirements of various industries on commodity filling, wax molding filling machinery must be adapted to the development of the filling industry, the future development trend of filling equipment is to actively develop general-purpose machines, vigorously develop auxiliary equipment, electromechanical instrumentation technology is the mainstream of quantitative filling machine development. PLC-based automatic wax molding filling system with a high degree of automation, PC as the control core and frequency converter through bus communication, complete the contactor and other controls. Need to understand the wax molding filling automatic production line of the main technology, research and development design to meet the needs of the use of automated production lines.
PLC is a microprocessor as the core, the logic control, data calculation and processing combined with a wealth of software resources, modern industrial automatic controller. PLC has become an important and widely used industrial control microcomputer, the full use of code integrated circuits and communications technology, can be constituted, including the logic of the process control, data acquisition, and other integrated control systems. the IEC defines PLC is a microcomputer-based design of industrial environment. Digital store information desk, complete the logic sequence counting and other prescribed functions, through the output control of mechanical production processes.PLC products in the anti-magnetic, hazardous exhaust corrosion, etc. has a strong ability, the reliability of the average trouble-free time of more than 50,000 hours.PCL is widely used in many industrial areas, because it has real-time, high reliability, simple and flexible system configuration and other advantages. Currently, there are various types of PLC on the market, mainly composed of CPU, I/0 unit and power supply, etc. PLC control system external switching signals are stored in the internal data memory of PLC through the input interface, and then sent to the output interface in the form of output variables after logical operations.PLC operation is carried out according to the program requirements, and is divided into character and graphic modes in accordance with the mode of expression.
The PCL completes the work of cyclic scanning, the CPU develops the sequence according to the system monitoring program, the status update of the output points, the display update and the programmer's keying response and other functions. The method of scanning execution can be carried out by arranging different organizational modules, PLC adopts a centralized sampling and output work. With the increasing development of computer network technology, fieldbus technology has become the focus of attention in the field of industrial control. PROFIBUS is a universal open fieldbus standard, is a German company research institute launched fieldbus, with network configuration simple and so on. PROFIBUS consists of PROFIBUS-PA, DF with the FMS compatible part of the composition of the DP transmission rate of up to 12Mbit/s, with rapid troubleshooting, interchangeability and other characteristics of a wide range of applications. Profibus-DP using the first two layers of the transmission layer and the user interface layer, the network can be a single-master or multi-master structure in the network of DP masters and DP slaves using the master-slave communication principle, the slave sends information to the master to respond back to the master, the slave includes the PCL, decentralized I/0, inverter and drive, and so on. The slave stations include PCL, decentralized I/0, inverter and driver, etc. Wax molding and filling automatic production line system 2 powder is a common form of material in industrial production, soft filling wax molding automatic production line can complete the weighing and filling and shaping processes, the production of good powder material by weighing the material by the drop mouth to support the opening of the empty bag, sealing machine sealing bag in the conveyor belt vertical transmission, ramp conveyor conveyor belt conveyor to the palletizing station according to the process requirements according to the pre-determined palletizing type palletizing. The palletizer automatically replaces the pallets and transports them to the forklift area by means of a conveyor belt, and the indicator light reminds the forklift to transport the pallets to the storage area. The function of the automated wax molding filling system revolves around the filling process, and the main equipment includes electronic scales, integrated intelligent palletizers, etc. Design wax molding filling system is a typical mechatronics system, automatic wax molding filling system is mainly used in chemical grain and other industries in the automatic filling of powder and granular materials.
Automatic filling wax molding production line is electromechanical instrumentation technology to form a high-tech products, mainly to complete the bag for the bag, inverted bag shaping sealing and so on. Automatic production line control system by the PLC integrated control system, usually by the power source, mechanical structure and electronic computers and other elements, according to the system input and output signals for PLC ladder diagram preparation. At present, there are more than 50 kinds of fieldbus in the world different kinds of fieldbus lack of uniform definition, fieldbus has interoperability, the realization of industrial production site communication of various types of equipment, can expand the network structure and other characteristics. Fieldbus breaks the traditional decentralized control system structure form, with communication function does not depend on the controller, control system control program dispersed to the production site at all levels of intelligent field equipment, detection transmitter detection signal can be transmitted to the field actuators to achieve decentralized control. PROFIBUS is a widely used fieldbus control system, with network structure construction form for the main bus type, high transmission rate, strong information transfer capability. PROFIBUS is a widely used fieldbus control system in China, which has the advantages of network structure built in the form of the main bus type, high transmission rate, strong information transfer capability, etc. PROFIBUS enables decentralized distribution of digital controllers to realize unified networked management from the field layer to the control layer, with the master station tasked with controlling the data communication of the bus, and the slave station usually for I/O devices, drives and measurement transmitters and other peripheral devices.
Research using PROFIBUS-DP fieldbus structure for the construction of the control system, suitable for PIC and field distributed I / 0 device communication, so that the PLC and distributed I / 0 to realize the cycle of rapid data exchange. The upper computer consists of PC upper computer, the operator station installs the configuration king monitoring and operating software and authorization license, the configuration interface window can display the current residual material and can modify the PID adjustment parameters of filling, the engineer station installs the configuration king monitoring and controlling software which the operator station has, and can manage the project files of the production line, and the operator station and the engineer station have the operating privilege setting, and the operator of the main station and the PLC's MPI port are converted through the The MPI port of master station operator and PLC is converted and connected by PCAdapter adapter, the host board card is inserted with Siemens special CP communication card, and the ET200M of slave station is a distributed slave station to realize the data exchange between master and slave station. The controller selects Siemens CPU315-2DP to meet the communication requirements of the production line control system, and the MPI interface realizes the communication and data transmission between the PCL and the host computer. MPI interface realizes communication and data transmission between PCL and host computer. 16MB data memory card is chosen to meet the demand of programming storage. The DP slave with distributed I/O ET200M can be mounted with expansion modules. The analog input signal of the weighing and metering signal is at the filling station, and the analog input expansion module SM331 is mounted at the filling slave to reduce the wiring distance.
Electrical schematic diagram is an indication of the role of the electrical operating principle of the equipment representation of the control system electrical schematic design, analysis of electrical circuits to rule out machine tool circuit failures, electrical schematic diagrams mainly include the control circuit protection and other parts of the PLC programming part of the control system is the core of the programming by the network configuration design, detection of the weighing program design and other sub-programming constitutes a PCL module selection is completed, you need to be in the After the selection of PCL module, it is necessary to carry out hardware configuration in STEP7, and PLC assigns the corresponding address for the input variables of the expansion module. PLC program is divided into operating system and user program part, and the operating system is used to realize the function independent of the specific control task. STEP7 software puts the user programming and data into the corresponding program block, and makes the user program have planning by calling each other between the blocks, and there are many kinds of program blocks in the user program. There are many kinds of program blocks. User programs can be composed of a combination of different blocks, OB organization block can call any function block, FB and SFB use need to configure the corresponding background data block.
3 Automatic wax molding and filling system design and implementation
Automatic wax production line control system function is divided into on-site equipment layer, management monitoring and equipment control layer, equipment layer is mainly to complete the production equipment on-site monitoring, including control panel buttons cooling molding temperature sensors and other field equipment, some motors on-site need to be inverter control, through the installation of inverter on the PROFI-BUS communication module CB to achieve the master PLC and the master of the DP communication. Control layer master and slave station communication through the DP bus, the slave station is responsible for the field information acquisition to the master station to send the relevant signals, according to the requirements of the production process control, the master station adopts the S7-300 series CPU315-2DP PLC, the slave station adopts the ET200 remote I / O and Siemens MM440 inverter device.
ET200M slave control cooling heating and crystallization, inverter control of the main motor, cooling motor and compressor, through the communication module CB board and ET200M transmission and the master station DP day constitute a fieldbus network. Production line control system software lower computer programming using STEP7 software to achieve, running under Windows95 standard parts and software packages composed of a new project named generating station, double-click the Hardware option to enter the Hwconfig window, according to the order of hardware installation insert the rack power supply into the line of hardware configuration, the emergence of the Properties - DP dialog box selected for the DP master station. In the hardware catalog to find the ET200M M153 and MM440 slave devices, set to set the address of the DP slave mode, after the completion of the configuration compiled and downloaded to the PLC. The use of STEP7 ladder language programming, the master station running program to solve the system start-stop reset and other functions of the slave program including the master station to send this site to connect to the information programmed to simulate the debugging and then downloaded to the PLC. the upper computer monitoring software using the popular Configuration King software, Windows08/Windows2000/WindowsNT4.0 Chinese operating system as the operating platform, with a good human-computer interface and other features. It is characterized by good man-machine interface. The configuration king has built-in a large number of device drivers, which can realize communication and data exchange with external devices,
Automatic wax filling and molding production line can automatically complete the weighing and bagging functions, the mechanical system includes automatic weighing unit, conveying detection unit, etc. PLC control system is the core part of the automatic filling system, the control system is required to have a high degree of reliability, strong troubleshooting capabilities. Filling system control for the switching quantity, choose Mitsubishi FX2N series PLC for the modular structure. Filling and molding automatic production line control system based on PLC integrated control system, according to the flow chart to prepare the ladder diagram of the PLC, using the Mitsubishi Corporation series programming software GXDeveloper-8 ℃ programming. Debugging stage using simulation software GXSimulatoer6-C on the control system PLC program for software debugging. Joint hardware and software debugging on the hardware, the system to obtain good application results.
4 Conclusion
In this paper, the design of automatic wax production line system using Profibus-DP network technology, through the upper monitoring machine and intelligent field device communication to realize the system of distributed control, easy installation and commissioning and equipment maintenance, network reliability with high cost-effective, to promote the development of China's wax processing technology is of great significance. Production line control system functions to achieve the intended goals to complete the automatic wax molding filling system control system hardware and software design and debugging work, the program uses modular design ideas for the future maintenance and improvement of the software to provide convenience. With the development of science and technology, people pay more and more attention to reducing labor intensity. With the booming development of China's sharing business, wax filling and molding automatic production line will play an important role in promoting the development of industrial automatic production.