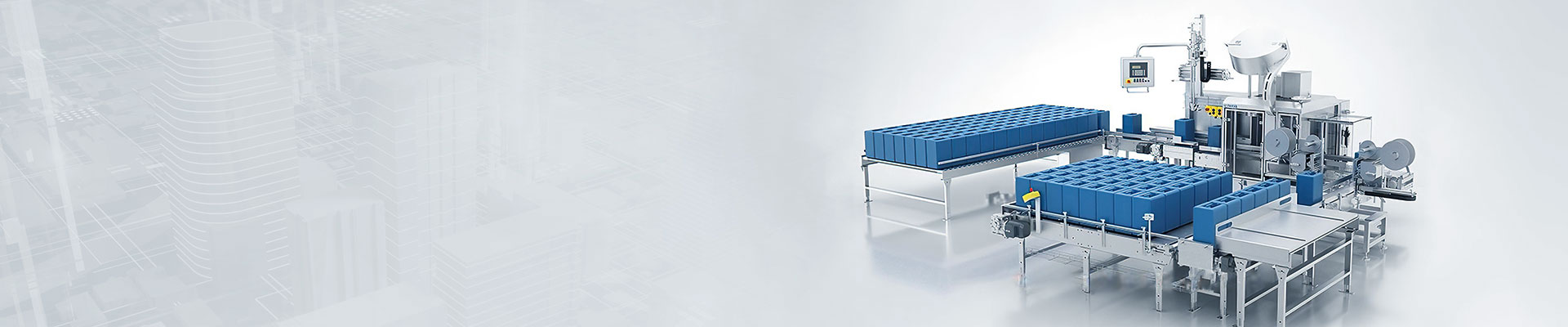
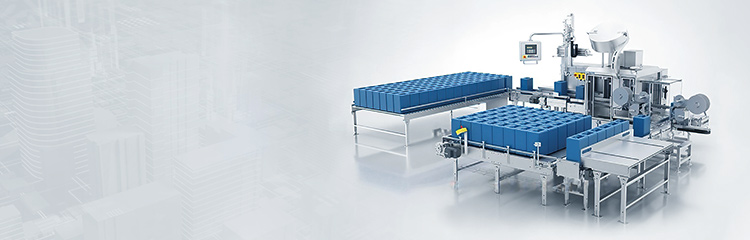
The main use of quantitative filling machine servo motor to realize the rotor pump stroke control, and then realize the filling volume control. Before filling, the front weighing module obtains the weight of empty barrel, after filling, the rear weighing module obtains the weight of filling and transmits it to the weighing instrument, which will read out the filling data in real time to get the weight deviation, and the filling algorithm calculates the control volume of large materials, the weighing system will send the control volume to the servo drive, which will drive the quadratic rotor pump to perform the early closure of the small material volume and then control the filling valve of the small material, and the upper computer will read out the filling data in real time through the Ethernet connection with the weighing instrument. The upper computer is connected to the weighing instrument via Ethernet to read the filling data in real time, and the process parameters can be set to monitor the operation of the production line.

The main automatic Filling machine utilizes servo motor to realize rotor pump stroke control, and then realize filling volume control. Before filling, the front weighing module obtains the weight of empty barrel, after filling, the rear weighing module obtains the weight of filling and transmits it to the weighing instrument, which will read out the filling data in real time to get the weight deviation, and the filling algorithm calculates the control volume of large materials, the Weighing system will send the control volume to the servo driver, which will drive the quadratic rotor pump to execute the early closing of the small material volume and then control the filling valve of the small material, and the upper computer will read out the filling data in real time through the Ethernet connection with the weighing instrument. The upper computer is connected to the weighing instrument via Ethernet to read the filling data in real time, and the process parameters can be set to monitor the operation of the production line.
Liquid filling machine machine vision inspection system software consists of a number of modules to control and monitor the visual inspection system, in the process of use, the user can be flexible according to the actual needs of different modules, through a combination of different modules can be obtained through the different functions of the inspection system, the system software can complete the functions include: liquid bottle body, bottle mouth, bottom of the bottle on-line detection; liquid bottle level height detection; Bottle dirt detection; defective rejection mechanism control and rejection speed and other parameter settings; remote operation and fault code display; historical alarm information storage and generation of fault data report.
Technical Parameters
Measuring accuracy: less than 100 grams
Pipe caliber: Inlet φ40
Medium temperature: 0-60℃
Gas source pressure: 0.8Mpa
Single-channel gas consumption: 0.6m3/min
Working voltage: 220V
Measurement: Mass (kg)
Production capacity: 180L/h specification 200L (according to the degree of proficiency and the viscosity of the liquid is different from the increase or decrease)
Measuring range: 50-250Kg
Filling speed: 8 seconds can fill 20 liters