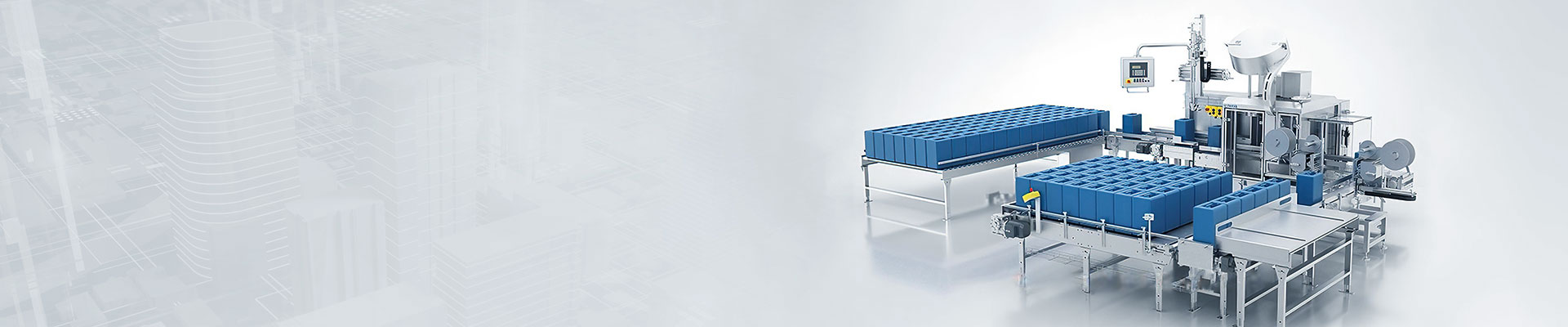
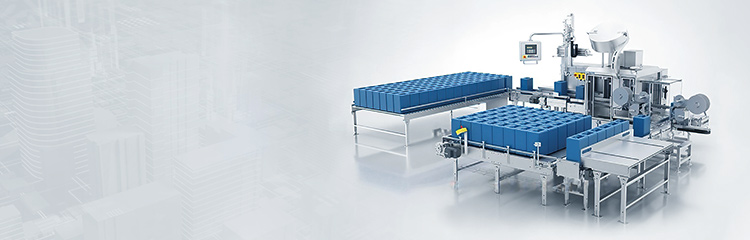
Quantitative filling machine filling adopts stepping motor to drive the filling valve up through the screw according to the pre-set speed: when the filling requirement is reached, the filling is closed. Adopting automatic capping, capping, sealing one by one, the filled pail is accurately sent to the automatic capping machine, the capping machine, through the robot, sucks up one pail cap each time and accurately places it on the top of the filled pail, and the automatic sealing machine will immediately cooperate with the action of the pail cap to accurately squeeze the pail cap, sealing the filled pail.

Automatic Filling machine using the servo unique electronic cam function with the new pr motion control mode, only external encoder as a command source, you can realize the filling speed and bottle feeding speed in real time to maintain high-precision synchronization. At the same time, the use of servo By-pass function, without the participation of expensive motion controllers, to achieve cost-effective multi-axis servo synchronous control of a master multi-slave control scheme.
The synchronized production line of automatic filling machine is mainly divided into 3 parts: bottle feeding axis drag chain, horizontal tracking axis and vertical tracking axis. Synchronization mechanism, bottle feeding axis drag chain, horizontal tracking axis and vertical tracking axis 3 parts of the power source are bottle feeding drag chain motor output. Most of them are synchronized by mechanical cams through multi-stage mechanical transmission, driving two solid cam mechanisms.
Servo filling production line is divided into bottle feeding axis drag chain, horizontal tracking axis and vertical tracking axis 3 components, only in the mechanical structure, abandoned the traditional mechanical cam connection, instead of filling servo system, through the precision screw respectively control the horizontal tracking axis (X-axis) and vertical tracking axis (Y-axis) displacement. The command sources for its servo system are all provided by high resolution encoders mounted on the bottle feeding drag chain.
Filling encoder resolution is 2000p/r, cam one week, weighing and filling machine encoder rotates 2 times, the number of pulses collected 16000ppr, 5v differential signal. The main motor is controlled by frequency converter with working frequency at 0~50hz. the pitch of slide screw is 10mm, the resolution of X/Y servo encoder is set to 100000ppu by electronic gear ratio function. the length of the area where the machine axes are synchronized is A~B=240mm. the distance where the Y-axis is inserted is 40mm. the length of the area where the machine axes are synchronized is A~B=240mm. the distance where the Y-axis is inserted is 40mm.
Technical Parameters
Measuring range: 20kg~30kg
Measuring method: 2-row dosing volume: 30kg
Feeding precision: ±0.1%
Graduated value: 0.01kg
Power supply: AC220V (3-phase) 60HZ
Using air pressure: 5kgf/c㎡