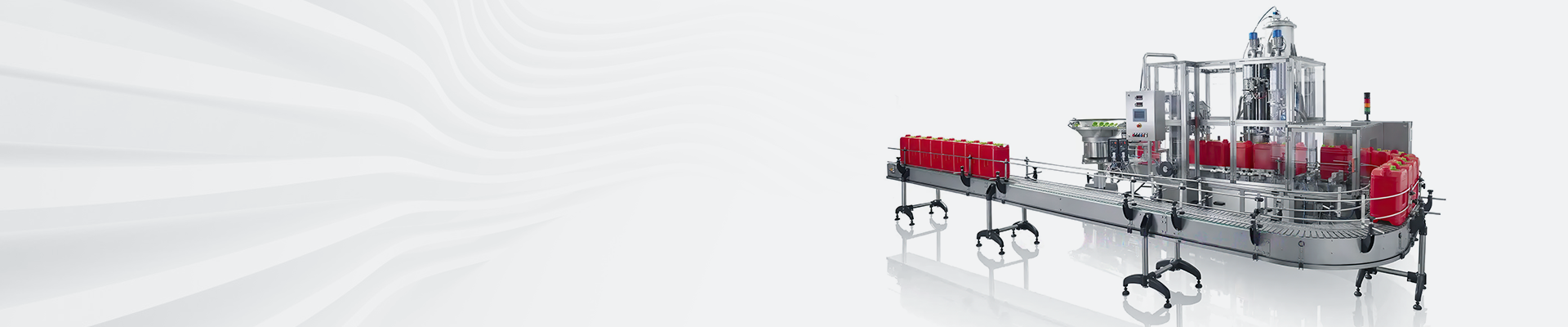
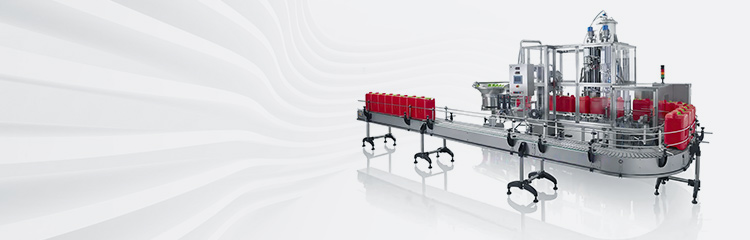

Summary:Automatic filling machines are typical custom-designed products. The design process is divided into layout design, structural design and motion design.This article studies technologies such as logistics simulation for layout design, assembly simulation for structural design, and motion simulation for motion design to provide simulation support for the design of automatic filling machines.
1 Preface
Filling system is a beverage production line for connecting and coordinating a variety of beverage production unit equipment, because the beverage production unit equipment is provided by the professional equipment manufacturers, so the design of the filling system is the main content of the beverage machinery manufacturing enterprises for order-oriented design. In the design stage of the layout, structure and operation of the liquid filling machine, it is difficult for designers to comprehensively consider the production line site, conveying balance, the entire line capacity targets, assembly interference, etc. The application of computer simulation technology to achieve support for the design process of the conveying system is an important way to improve the efficiency and quality of the design.
2 Conveying system design and simulation
2.1 Problem formulation
Automatic filling machine is the filling machinery, cooling / sterilization devices, labeling machines, carton machines and other automation equipment connected to become an important subsystem of the filling production line, to meet the capacity of different beverages under the premise of the target, to ensure that the balance of the entire automatic filling machine and beverage delivery smooth is the primary objective of the conveyor system design and of course, cost and delivery requirements. This is a typical multidisciplinary product optimization design problem, in which to ensure the balance of the production line belongs to the logistics problem, which involves the optimization of logistics planning and layout design; the body of the conveyor system consists of a large number of parts and components, the design of which belongs to the mechanical structure design problem; and the smooth delivery of beverages belongs to the problem of motion mechanics. The application of digital means, especially simulation technology, to support the design process of the conveying system is the key to improve the design quality and efficiency.
2.2 Simulation-based optimal design of conveyor system
The design process of conveyor can be divided into 3 major stages: layout design, structure design and motion design.
(1) Layout design: Layout design is mainly an optimization problem with the objective of balancing the logistics of the conveying system and meeting the production capacity of different beverages, with the workshop site and machine production capacity as the constraints, and with the conveying area of each conveying section (length and width) and conveying speed as the independent variables. Due to the capacity requirements for conveying different products and the speed of different machines to handle different products, and at the same time to consider the uncertainty factors in the conveying process, etc., thus increasing the difficulty of layout design. The logistics simulation model of the conveying system is established to simulate the layout design of the conveying system, so as to realize the optimization design of the conveying system layout.
(2) Structural design: Structural design is mainly to refine the results of layout design from the perspective of the mechanical body, including parts design, component design, and whole line assembly design. Since most of the components that make up the conveyor system are standard and common parts, the key to structural design is to eliminate possible problems in the assembly process, i.e. assembly simulation.
(3) Motion design: the conveying system mainly uses the friction between the motor, the belt and the beverage to realize the linear motion of the beverage, and uses the friction between the beverage and the baffle plate to change the direction of movement of the beverage. As the process of beverage conveying system involves a number of different speeds of conveying section, how to reasonably control the speed to prevent individual or even chain reverse bottle phenomenon, is the key issue to be resolved in the design of the conveying system to run!
3 Layout design-oriented logistics simulation
Conveying system layout focuses on reflecting the location and capacity of each unit of equipment, the form of each conveying section (such as curved, straight, etc.) and parameters (such as length, width, etc.). Layout design-oriented logistics simulation refers to the establishment of the logistics model of the conveyor system, the application of simulation tools to simulate the use of the conveyor system in the process of a variety of situations (such as machine failures), in order to find out the problems in the design of the conveyor system; at the same time, through the adjustment of the length of each conveyor section, width, number of lanes, speed, and other parameters, to provide support for the layout design of the conveyor system. This paper develops an automatic filling machine simulation system based on Witmess, which has the functions of beverage/machine/conveyor belt/buffer zone parameter setting, machine/conveyor belt failure simulation, normal/fast/timed simulation, equipment/conveyor belt/buffer zone/conveyor system simulation result output, etc., and realizes the integration of conveyor system layout design with the CAD environment, which effectively supports the conveyor system layout optimization design. Layout optimization design.
4 structural design-oriented assembly simulation
Measuring and filling machine is a complex product, by more than one designer to complete, the need to apply assembly simulation technology to ensure that the design results completed by more than one person can be correctly assembled.
Assembly simulation should first establish a simulation model that contains the assembly of parts and components in the assembly relationship, the assembly relationship mainly describes the relative position of parts and components with the positioning relationship, describing the relative movement between parts and transmission of the movement relationship, direct connection relationship, the vast majority of current commercial three-dimensional CAD systems support these three kinds of assembly relationship. Because of the many parts of the conveyor system and most of them are general-purpose parts, the establishment of parametric structural models for the parts is a common means to improve the efficiency of conveyor system design. Therefore, in order to support the assembly simulation of the conveyor system, it is necessary to increase the assembly reference and assembly relationship information on the parameterized component model, and the corresponding assembly reference information should be included in each component model, mainly:
(1) Assembly sequence information: it refers to the assembly order of the parts in the assembly body in the assembly process.
(2) Assembly datum information: refers to the datum used in the assembly process to determine the relative position of the parts in the product.
(3) Position and attitude information: refers to the coordinate position R0 and attitude of the parts in the assembly coordinate system, which can generally be expressed by a 4x4 geometric transformation matrix, in which R is a 3x3 positive definite matrix indicating the rotational relationship from the assembly component coordinate system to the assembly coordinate system, and T is a 3x1 matrix indicating the translational relationship from the assembly component coordinate system to the assembly coordinate system.
The assembly simulation process is realized by moving the parts from the initial position to the final assembly position, the initial position is given by the designer, and the spliced modules in the layout scheme contain a lot of information, among which there is the relationship information between the modules, and the relationship information refers to the assembly relationship between the modules, and the assembly relationship is used to describe the constraints between the parts and components, and in general, the product assembly relationship can be divided into three categories: the positioning relationship, the connecting relationship, and the movement relationship. The general product assembly relationship can be divided into three categories: positioning relationship, connection relationship and motion relationship, which can link the assembly relationship between modules and the assembly relationship between specific parts, and the final assembly position is generated by calculation according to the assembly relationship between parts in the layout program. In order to ensure the assemblability of components, it is necessary to check whether there is interference between the parts of the assembly, if there is interference between the parts of the assembly parts can not guarantee reliable assembly, the parts must be adjusted and modified to meet the needs.
Conveyor system assembly simulation process and assembly simulation results are shown in Figure 4 and Figure 5, respectively.
5 Motion Simulation for Motion Design
Motion design is based on the structural design of the beverage bottle conveying motion design, which focuses on the design of the motion speed to ensure that the beverage bottle is smooth in the entire conveying process as the goal. The support for motion design is mainly through the analysis of the smoothness of the movement of beverage bottles to guide the design of the movement speed of the conveying system, if necessary, to adjust the structure of the conveying system.
In the process of beverage production, a series of operations such as filling, capping, labeling, etc. are carried out by automatic filling machines to transport beverage bottles. With the increase in the types of beverages and the diversification of the shapes of beverage bottles, the smoothness analysis of the movement of beverage bottles, which is directly linked to productivity, is becoming more and more important. In the following, we mainly analyze the force acting on the bottles during the delivery process, analyze the possibility of bottle tipping, etc. The main factors leading to bottle tipping are the conveyor system with different speeds and the external force. In order to analyze the simplicity of the Chin material bottle is simplified into a uniform mass of equal straight rods.
(1) bottle dumping situation analysis
Set the radius is d, the center of gravity height is h, gravity G = mg coefficient of kinetic friction, assuming that the bottle model in the external force, the cylinder will swing around the point 0, for the rotational inertia about the 0 point, when the cylinder rotates around the 0 point when the angle of 0, gravity produces a moment of repulsion, the occurrence of dumping, the bottle dumped the critical condition is the center of mass moved to the bottom of the out-of-plane.
(2) speed changes triggered by the mechanical model of the inverted bottle before the first section of the conveyor system speed is, after a section of the conveyor system speed is ", when # and the direction of a straight line, when the cylinder dumped due to the difference in speed generated by the kinetic energy is greater than equal to the increase in the value of the potential energy for the conveyor system motion simulation of the interface.
6 Summary
Automatic filling machine plays an important role in the beverage production line, how to quickly design a filling production line to meet the requirements of beverage production, has become the current beverage machinery manufacturing enterprises focus on content. The application of multidisciplinary simulation technology can effectively support the design of the life cycle of automatic filling machine, is to improve the rapid response of enterprises to customer demand, reduce design and development costs, and improve market competitiveness is an important way.