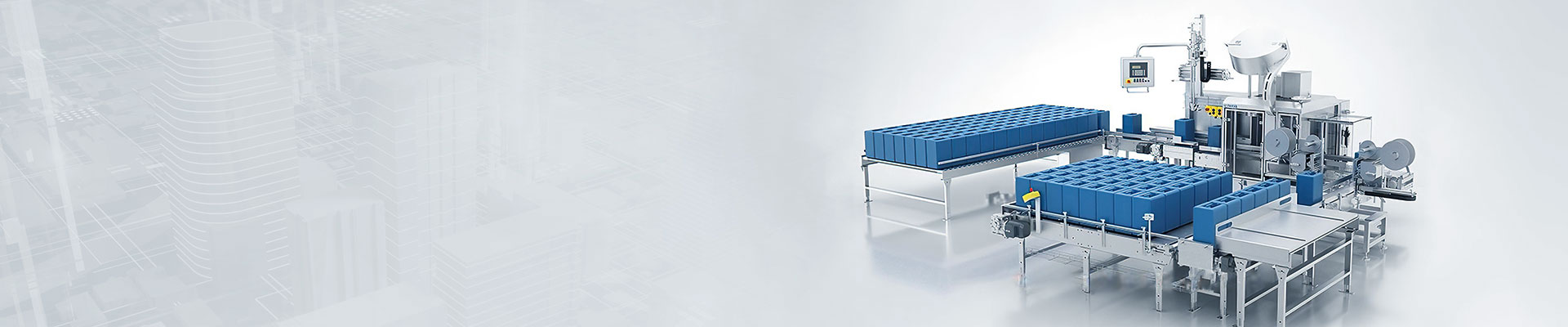
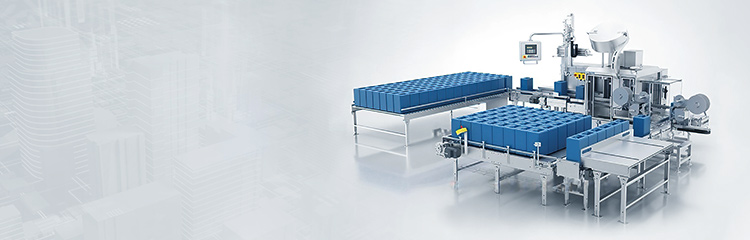
The filling system is made of high quality polyoxymethylene copolymer replacement parts can be changed quickly, can easily process a variety of containers. Through the peristaltic pump or ceramic piston liquid metering system, the scale detects the container in place to start filling, the filling is completed and enters the capping area, respectively, to put the inner cap, seal the inner cap and press the outer cap, the integration provides a powerful filling platform to realize the ease of use of the PLC programming configuration as well as integration and unity with the upper unit configuration system.

The automatic Filling machine has two working modes: automatic driving and manual. Through the computer interface to switch between manual and automatic switch to switch, generally use the automatic state to let the PLC automatically track and set parameters for automatic control, when the equipment needs maintenance, debugging or special circumstances can be used to manually drive a single device start, stop. Generally used through the pump to add directly to the filling method, neither good for filling the amount of real-time control, but also can not automatically record the amount of real-time addition, so the consumption of solvents, solutions, waste is relatively large, the filling ratio is not accurate; another method of controlling the speed of the pump motor through the frequency converter to add the amount of filling to the given process requirements, this method of control is not accurate, slow response, can not realize automatic closed-loop control and meet the control requirements. This method has low control accuracy and slow response speed, and cannot realize automatic closed-loop control and meet the control requirements.
Liquid filling machine is mainly composed of four parts: transfer device, filling device, suction and sealing device and detection and sensing device. Transmission device consists of conveyor belt, transmission gear, conveyor belt, conveyor motor and lifting cylinder; filling device consists of filling gun, filling barrel, synchronous motor, rodless cylinder and roller arm; suction capping device consists of suction capping device; detection and sensing device consists of photoelectric sensors, proximity switches and weighing sensors.
Weighing filling machine each sensor signal to carry out directly into the corresponding weighing controller, through the serial port or Modbus protocol weighing controller will be the weight of the signal transmitted to the computer, the computer according to the automatic filling machine weighing control of each raw material silo dosage of the final control valve, add the required weight of raw materials.
Technical Parameters
Maximum weighing capacity: 300kg
Quantitative range: 100kg~300kg
Graduated value: 100g
Canning accuracy: OIMLR61 x (0.2)
Canning speed: 10~20 cans/hour
Power supply: AC220V50Hz
Using air pressure: 0.5MPa
Control mode: 2-speed control
Conveying method: the tank adopts manual conveying method valve material: SUS-304 (optional: SUS-316)