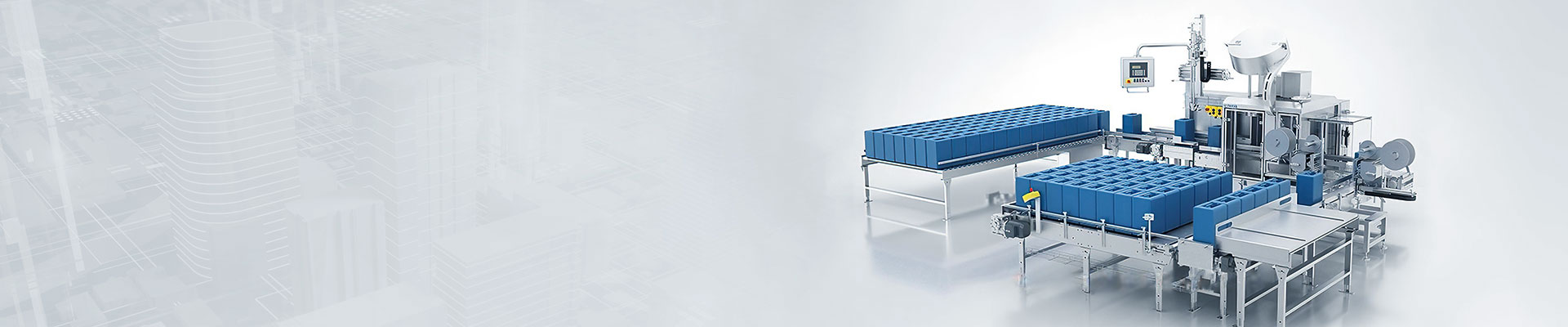
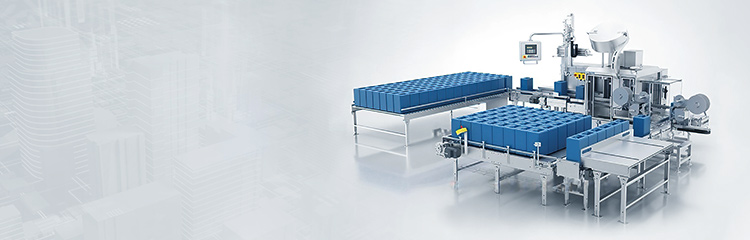
Liquid filling machine is used to send out the request to enter the car number, password, work number, filling and other commands, the weighing system is required to deal with the RF reader, weighing table data, communication of the upper PO and other serial data, the establishment of the barrel ID and information and staff permissions and other databases, so as to facilitate the effective query operation of the lower computer data uploaded when the database receives information indicating the car number and weight, the data is directly recorded in the database When the database receives the information indicating the car number and weight, the data will be recorded into the database directly, and each filling station can output statistics and reports on these data.

The filling system is set to automatic mode of operation by means of a switch. Once started, the drive motor of the conveyor is started and held until the stop switch is actuated or the containers to be filled are conveyed under the filling system; after the containers are filled and capped, the drive motor of the conveyor belt must be automatically started and held until the next container to be filled is conveyed under the filling system or until the stop switch is actuated.
The weighing and filling machine combines a filling device and a capping device to make the filling stable and efficient. The difference of container size is realized by the work of reflective photoelectric module, and the positive level triggering of the counter by the auxiliary relay is used to realize the counting of the produced products.
Once the filling system is powered on, the conveyor belt drives the electric motor, when the empty containers travel to the travel switch, the travel switch closes and the electric motor stops, the filling system controls the filling time through the closing of the valves and the motor resumes rotating after the filling process is completed, so that the cycle realizes the automatic control on the filling machine. The differentiation of the size of the containers on the conveyor belt is realized by the work of the reflective light weight module at the location.
Basic parameters
Weighing range: 10~300kg
Material interface: DN40 material
Inlet pressure: <0.6MPa
Filling speed: 1~2 barrels (200L)/minute (through the diameter of 1.5" material flow rate to ensure 280L/min)
Filling accuracy: 0.2 grade
Spray gun structure: liquid filling scale contact material part of the material material for the 316, 316L stainless steel, the rest of the material for the 304 stainless steel, carbon steel, etc.
Gas source: pressure 0.5±0.1Mpa, consumption 10m3/h, quick connector 8㎜
Air tube power supply: 220 (-15% ~ +10%) VAC, 50Hz easy to operate, easy to install gun lifting rate control barrel collision protection