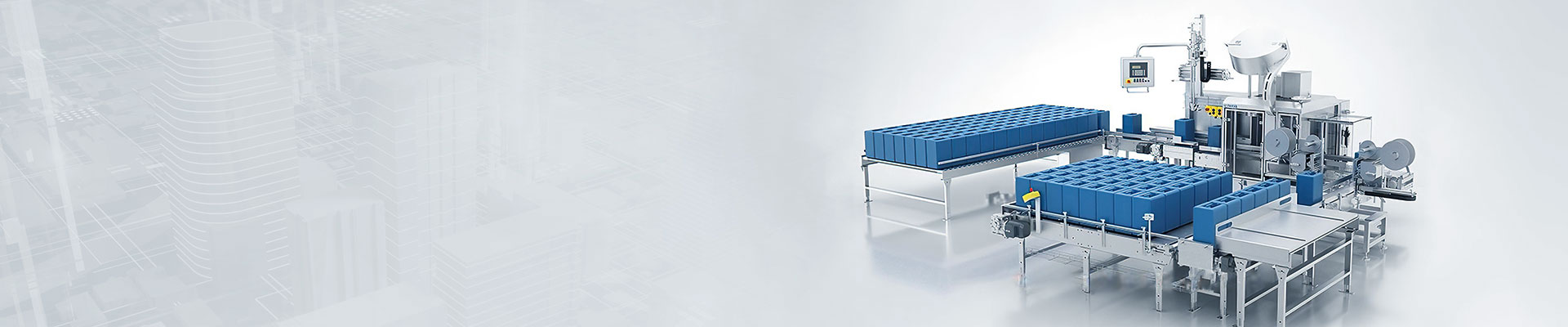
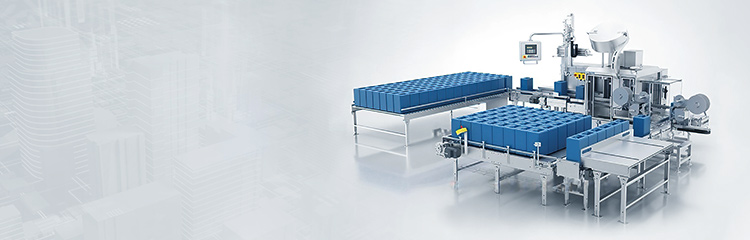
The batching control system includes screw conveyor, storage bin, gate, cutting device, weighing body, support, electrical control device, etc. The feeding device is fast and slow two-stage feeding mode. The PLC sends a signal to the cylinder to drive the plunging plate to work, and the material in the hopper flows into the weighing bucket, and the weighing module above the weighing bucket sends a signal to the PLC, so as to control the operation of the cylinder. When the weight is approaching the required weight, the PCL sends a signal to the cylinder with plunging plate, so as to slow down the discharge speed. When the value reaches the weighing module, the PLC sends a signal to the cylinder and the plunging plate seals the material port.

Batching scale is a measuring equipment for continuous weighing of bulk solid materials transmitted by screw in the process of industrial production, the screw conveyor of the whole weighing device completes the task of measuring the amount of materials, the Feeder completes the task of adjusting the amount of materials and the hopper completes the task of storing and buffering the materials, which constitutes a set of batching device by the batching screw scale, the feeder and the hopper. The mechanical part of batching screw scale is composed of weighing frame and screw transmission, in which the weighing frame is the load bearing and gravity transmission device of the screw scale, and the electropneumatic part of the batching machine is composed of load cell, speed sensor, weighing instrument and speed control motor, and so on. The working condition of each part is as follows: when the material in the silo is put into the dosing screw by the feeding equipment, and the material runs with the screw to the weighing point, the weighing module converts the weight of the material into electric signal, and the speed sensor converts the speed value of the screw into electric signal, which is summarized by the junction box and then sent to the weighing instrument, and the instrument carries out the corresponding arithmetic and processing on the collected signals and finally converts them into the instantaneous flow rate and cumulative flow rate. The instrument will calculate and process the collected signals, and finally convert them into instantaneous flow rate and cumulative flow rate. At the same time, the weighing instrument outputs a standard control signal to the speed control motor to adjust the feeding speed, so as to keep the material flow rate stable, and finally make the system more accurate.
The function of the feeder is completed by the dosing screw machine, in the population of the feed hopper, usually in the horizontal direction is equipped with a cut-off gate; in the outlet of the feed hopper and the vertical direction of the spiral surface is installed with up and down movement of the feed gate. Cut off the gate is usually used to cut off the feed hopper of the lower material, in order to complete the dosage of zero and other operations. The feeding gate usually has a fixed opening, and when the flow rate setting value changes, only the speed of the screw machine changes, while the material load on the screw always remains stable; however, when the flow rate setting value changes considerably and exceeds the speed regulation range of the dosing screw machine motor, the feeding gate is operated manually, so that the Dosage system can work under a new value of the material load on the screw.
The supervisory system mainly consists of database server, PC workstation and Electronic scale, in which the database server saves the brand name formula and daily operation task data, etc.; the workstation carries out the maintenance of the brand name formula, operation task management and historical data query, etc.; the weighing module in the electronic scale is connected with the control terminal of the IND560, and transmits the weight data to the workstation through the IND560; in the process of the work, the theoretical weight of the single material is compared with the actual weight. The theoretical and actual weight of the single material, the equipment communicates with each other via industrial Ethernet with TCP/IP protocol.
PC recipe maintenance, add new grade recipe, edit or delete the existing grade recipe, browse all the recipes saved by the dosage system; task management: select the current grade recipe that needs to be configured, enter the total mass that needs to be configured for the current recipe, and the system will automatically generate the theoretical mass of each single material for the current task. And can browse the completed history of the task, the current task and not start the task, add new tasks, edit and delete the task has not begun; task query: query, print the history of the task data; user management: registered management system for the use of personnel, and will be divided into software operators, field operators and so on.
At the initial stage of dosage creation, the recipe maintainer will input each brand's recipe into the dosage database, this step only needs to be completed once, and when the recipe is changed, only the recipe database can be modified. After initializing the dosage and completing the maintenance of the brand name formula, the main steps are as follows: select the brand name formula and input the quality of the brand name to be configured, and the dosage automatically calculates the quality of each single material of the formula according to the formula; get the list of unfinished tasks from the database; according to the order of the task list, the weighing terminal determines whether the single material is the single material of the current task; if it is not the single material of the current task, it will give the error If it is not the single material of the current task, give an error message, if it is the single material of the task, compare the shelf life of the single material and get the theoretical mass of the current single material; put the single material into the electronic scale and weigh it, and transfer the quality information obtained from the electronic scale to the PC workstation; the PC workstation will forward the actual mass to the theoretical mass of the current single material for comparison, when the actual mass of the single material is in accordance with the theoretical mass (error within the permissible range), the single material is finished and the next single material is calibrated. Carry out the next single material calibration, when the formula of all single material are completed calibration, that is, to complete the current task. In the process of task completion, the dosage will automatically record the data related to the task, such as operator, batch code, and quality of each formula.