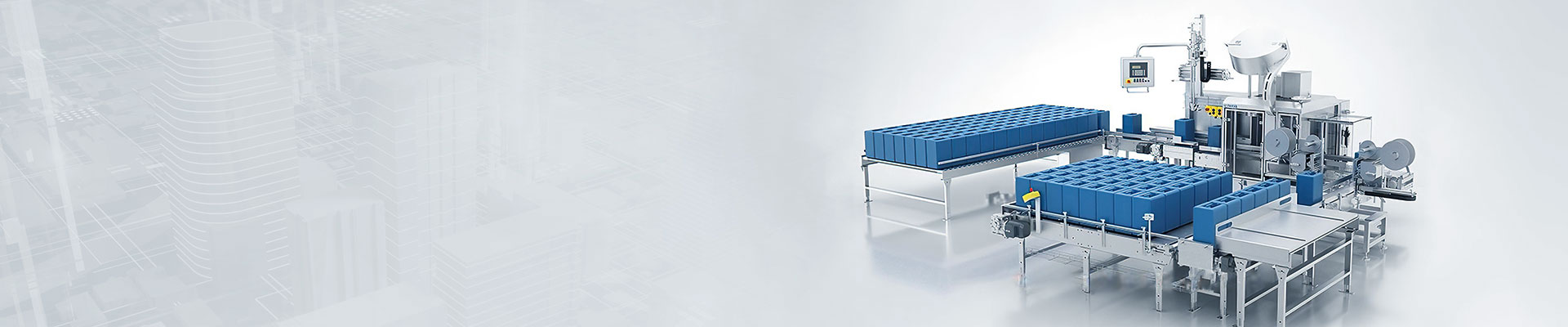
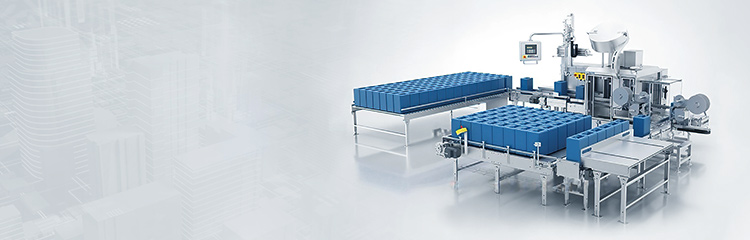
The hardware structure of the dosing system is mainly composed of UPS, PC, printer, serial conversion card and PLC, electronic scale, valve, motor, position detection device and other actuators. Through the electronic scale to continuously collect the amount of feed, RS232/RS485 serial conversion card and PLC communication, high-speed, stable and accurate transmission of data, when the dosage set value of one advance stop, dosage of real-time control process is completed by Siemens 115U PLC controller, and at the same time the use of communication with the upper PC, in the upper computer to complete the dosage parameter settings, data management, statistics, reports, prints and other functions. report, printing and other functions.

The Batching system is to weigh and measure all kinds of materials dynamically according to the formula, which is composed of sub-systems such as storage, batching, mixing, discharging, etc. According to the batching production control process, when entering the batching program, the batching will firstly detect the hopper scale to determine whether it is smaller than the preset value, if it is smaller than the preset value, it will start the material silo feeding device (the powder material needs to be conveyed by the feeding mechanism), and the material will enter into the hopper scale. The weighing module of the hopper scale inputs the measured dynamic data into the weighing instrument after the completion of A/D conversion by the intelligent unit; the weighing instrument compares the collected dynamic weighing data in real time with the pre-set expected dosage set value (i.e., the matching ratio parameter), and utilizes the algorithm to carry out the dosage control to ensure the dosage error; the controller will issue a directive to shut down the unloading device and the feeding mechanism when the set weight is reached; when all the materials are weighed and measured, the various materials will be fed according to the set value. When all the materials are weighed and measured, all kinds of materials are fed into the reactor according to the set program, waiting for mixing. Single material dosage.
The feeding system has raw material tank, weighing tank, mixing tank, when working by the motor driven pump to the weighing tank in order to inject different raw materials tank liquid materials, the target weight of the material set by the touch screen, each raw material weighing after injection into the mixing tank. When all the 5 kinds of raw materials are injected into the mixing tank after mixing, to complete the whole process. In the dosing control system, PLC and PT650D weighing instrument, PLC and touch screen use RS232 serial communication for data exchange. The OMRON PLC comes with two communication ports, and the CP1W-CIF01 option board is used to configure COM1COM2 as RS232C communication port, which is connected to PT650D weighing instrument and touch screen respectively.
The feeding system controls the frequency converter through different combinations of output switching quantities to realize fast feeding, slow feeding and fine feeding. At the beginning of weighing fast feeding, when reaching the given value of fast feeding prediction, start slow feeding; when reaching the given value of slow feeding prediction, start fine feeding; when the total weight of feeding reaches the "target weight - pipeline material weight a permissible error" when the feeding stops, in which the pipeline material weight is the material weight remaining in the pipeline that will continue to flow into the weighing tank after the motor stops rotating. After the motor stops rotating, the weight of material remaining in the pipeline will continue to flow into the weighing tank. The percentage of target weight is taken as the optimum value from the actual dosage, and the target weight and allowable error are set by the touch panel.